Roller Press Round Granule
Extrusion Line
Tongli provides an extruded fertilizer production line with an annual output of 50,000 tons to 350,000 tons, which is controlled by Siemens PLC and has a lower output but is flexible.
It is able to meet the application scenarios of fertilizer manufacturing/chemical/mining industry.
Production Line Equipment List

Roller Press Granulator
- Roller Compactor: To compact the raw material into dense sheets or flakes.
- Granulator: To crush and granulate the compacted material into round granules.

Raw Material Feeding System
- Hopper: To store and feed the raw materials.
- Conveyor: To transport raw materials to the granulation system.

Mixing System:
- Vertical Mixer/Blender: To ensure raw materials are uniformly mixed.
- Chainmill: To crush the returned material and serve as blending function.

Crushing and Screening System
- Bulk Crusher: To break down larger granules to the desired size.
- Rotary Screener: To separate granules of different sizes and ensure uniformity.
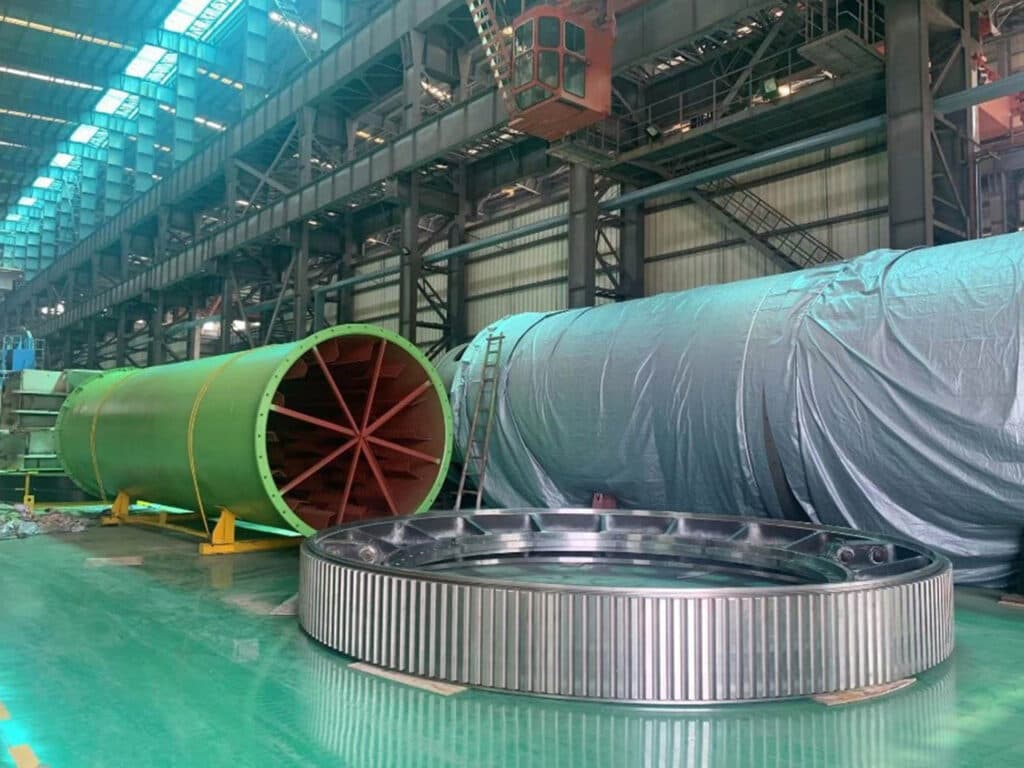
Dryer And Cooler System
- Rotary Dryer or Fluid Bed Dryer: To remove moisture from the granules.
- Cooling Machine: To cool down the granules after drying to prevent caking.

Dust Removal System
- The dust generated during the granulation process is collected by the ducting bag filter system/ Cyclone dust collector/ Centrifugal blower/ FRP chimney/ Exhaust gas scrubber(FRP)/ Ventri washer(FRP).
Double roller press fertilizer production line technical parameters
Equipemnt Name | Capacity | Parameter | Quantity | Power(kw) |
Electric belt scale | 1~10t/h | B650,L=2200mm | 8 | 1.5+1.5 |
Finished product scale | 2.5~25t/h | B800,L=3000mm | 1 | 2.2+2.2 |
Chainmill | 25~30t/h | FS800 | 1 | 7.5kw+7.5kw |
Bulk cruhser | 5~12t/h | PD800 | 1 | 7.5kw |
Pre-screener | 1.8x4m | TL1840 | 1 | 10kw |
Double shaft mixer | 25~40t/h | TL500 | 1 | 5.5kw |
Double roller press extrusion granulator | 0.6~1.2t/h | ZJ800 | 16 | 3kw |
Primary screener | 20~25t/h | 8000*2000*1500 | 1 | 15kw |
Fine screener | 20~22t/h | 8000*1800*1500 | 1 | 10kw |
Rotary drum drying machine | 20~30t/h | 1.8x18m | 1 | 85kw |
Rotary drum cooling machine | 20~30t/h | 1.6x16m | 1 | 55kw |
Rotary drum coating machine | 20~30t/h | 1.6*(6+1)m | 1 | 35kw |
Automatic Packing system | 75t/h | LCS-50 | 1 | 7.5kw |
Bagging Machine | 75t/h | TL-500 | 1 | 10kw |
Palletizing robot | 75t/h | ZJ-75 | 1 | 11kw |
Roll Extrusion Pelletizing Line Application Scenario

Agricultural Production
In fertilizer plants, extruded fertilizer lines with a capacity of 50,000-350,000 tonnes per annum usually process and produce fertilizer pellets of 3-10 mm, which can be used to meet the demands of commercial and continuous fertilizer production using animal manure, humus, etc. In addition, many plants use dry pelletizers to produce NPK fertilizer pellets such as urea, diammonium phosphate, potash, and others.

Chemical industry
Roller pelletizing production line can process all kinds of chemical raw materials (mineral powders such as limestone powder, gypsum powder, borax, etc. into different shapes and sizes of pellets) Mining industry (e.g., fly ash, coal slag, etc.) Produces pellets that can be easily transported and stored. Compare to steam drum fertilizer production line, the capacity is lower however it is more flexible, because the number can be adjusted.

Other Industrial Fields
For feed companies it is often necessary to process e.g. cereals, pulses, oilseeds, fishmeal, bone meal etc. Therefore, our double roll pelletizers can process these raw materials into tubular and rod-shaped pellets for animal feed. It is also possible to utilize biomass waste such as straw, sawdust, wheatcake, etc. to produce e.g. calcium oxide pellets or sodium alginate in the form of square bars.
Roll Extrusion Pelletizing Line Production Process
The first step in extrusion granulation is the preparation of raw materials. Common raw materials include potassium sulfate, monoammonium phosphate (MAP), diammonium phosphate (DAP) and urea. Powdered raw materials can directly enter the next process, while block raw materials need to be crushed by a bulk crusher or a double cage crusher first. After reaching the particle size required by the process, they are weighed with a belt scale. This process ensures that the particle size of the raw materials meets the requirements of the granulation process and ensures the quality and consistency of the final product. In the double-roll granule extrusion production line, the main purpose of raw material crushing is to change the physical properties of the raw materials to make them more suitable for double-roll extrusion. After crushing, the raw material particles become smaller and more uniform in shape, which can flow and transport more easily in the production line, thereby achieving higher production efficiency. This crushing process significantly affects the quality, output and production efficiency of the final product, ensuring the stable operation and efficient output of the production line.
The second process of extrusion granulation includes several key links. First, the production line is equipped with seven high-precision belt weighing scales. When the raw materials are crushed to the size required by the process, they are sent to the chain crusher through the raw material conveyor belt and elevator for further crushing and mixing. Then, the crushed raw materials are conveyed to the drum coarse screen for pre-screening through the scraper conveyor and bucket elevator. The screened raw materials then enter the comprehensive weighing scale and are sent to the double-shaft mixer or vertical mixer through the elevator for final mixing and mixing. In this way, the entire raw material preparation process is completed.
After the raw materials are prepared, they enter the granulation process. Our extrusion granulation production line, for example, the conventional 150,000-ton output, each production line is equipped with 16 round particle extrusion granulators with an output of 0.8 tons per hour. The raw materials after crushing and mixing are transported to these 16 extrusion granulators through scraper conveyors. In the extrusion granulator, stainless steel rollers roll and rub against each other to extrude the raw materials to form small particles. The extruded particles are sent to the rotary drum screener for screening through the discharge belt and the screening bucket elevator. Particles that do not meet the size standards are returned to the raw material crushing section through our unique scraper conveyor return system for re-granulation, realizing the recycling of raw materials.
When the material comes out of the granulator, the size of the particles is uneven. To achieve the qualified particle size, we set up a screening process after granulation. After the particles are formed from the double roller extrusion granulator, they will enter the rotary drum screener or vibrate screener, where they will continue to tumble and screen out unqualified particles and powders. Oversized particles and undersized powders are screened out separately. Fine powder will be returned to the granulator through the fine powder return scraper conveyor for re-granulation, while oversized particles will enter the bulk crusher through the coarse particle return scraper. After being crushed, they will return to the granulator for re-granulation. The screening process can effectively improve the uniformity and quality of the particles. The most important thing is that this process of cyclic screening and crushing return can increase the output of the production line while reducing losses. Generally, 100 tons of products can recover 2 tons of raw materials through our return system, increasing production and reducing losses by up to 2%.
The drying system of the extrusion fertilizer granulation production line is similar in principle to the drying system of the traditional drum fertilizer granulation line. Our drying process uses low-temperature and high-volume co-current drying. After the semi-finished material comes out of the granulation extruder roller press, it enters the drum dryer through the drying feed conveyor belt, and exchanges heat with the hot flue gas generated by the hot air furnace in co-current, evaporating and removing moisture from the material. The temperature of the dried product is generally between 50 and 70 degrees, so it cannot be directly packaged and needs to be cooled by a rotary cooling machine. A significant feature of the extrusion granulation dryer is that due to the low moisture content in the extrusion granulation process, the temperature requirement for the hot air furnace is also low. In addition, the selection of the dryer is also smaller accordingly. For example, under the same output conditions, the hot air furnace temperature of the extrusion granulation dryer is usually around 150 to 200 degrees Celsius, while the hot air furnace temperature of the traditional drum granulation process needs to reach around 250 to 300 degrees Celsius. This is why the roller extrusion fertilizer production line is more energy-efficient and more flexible compare to the steam drum method.
The drying system of the extrusion fertilizer granulation production line is similar in principle to the drying system of the traditional steam drum NPK fertilizer plant. Our drying process uses low-temperature and high-volume co-current drying. After the semi-finished material comes out of the granulation double roller extruder, it enters the drum dryer through the drying feed conveyor belt, and exchanges heat with the hot flue gas generated by the hot air furnace in co-current, evaporating and removing moisture from the material. The temperature of the dried product is generally between 50 and 70 degrees, so it cannot be directly packaged and needs to be cooled. A significant feature of the extrusion granulation dryer is that due to the low moisture content in the extrusion granulation process, the temperature requirement for the hot air furnace is also low. In addition, the selection of the dryer is also smaller accordingly. For example, under the same output conditions, the hot air furnace temperature of the extrusion granulation dryer is usually around 150 to 200 degrees Celsius, while the hot air furnace temperature of the traditional drum granulation process needs to reach around 250 to 300 degrees Celsius.
The material coming out of the cooler will be sent to the fine rotary screener through the fine screen bucket elevator for secondary screening. Then, the unqualified particles will be returned to the granulator through the return scraper for re-granulation, and the finished compound fertilizer that meets the requirements will enter the finished product metering belt scale for weighing and metering. We set up two screening processes in this production line because the screen size and function of each screening are different. The first screening is pre-screening, the purpose of which is to screen out unqualified particles before the material enters the drying and cooling, to prevent unqualified particles of different sizes from entering the subsequent steps, thereby improving the overall efficiency of the production line. The second screening is fine screening to ensure that the finished compound fertilizer meets the required specifications. This double screening design ensures the quality and consistency of the finished product.
The finished compound fertilizer weighed by the finished product metering scale will be coated by the coating machine. The purpose of this coating is to form a very thin film on the surface of the compound fertilizer particles. Block the direct contact between fertilizers to achieve the effect of anti-caking. At the same time, the system is also equipped with anti-caking agent screw conveyor, oil injection metering pumps and finished product metering scale. These three devices are interlocked and controlled by DCS Siemens. The oil injection amount and the powder spreading amount will be automatically adjusted according to the real-time material flow, thereby saving costs. Then the coated particles will be sent to the automatic quantitative packaging machine through the finished product elevator for packaging.scale
Regarding the finished compound fertilizer packaging machine, we offer both semi-automatic and fully automatic solutions. The servo motor automatic quantitative packaging scale is fast and accurate, with a packaging speed of 800 to 1000 bags per hour. The main body of the packaging scale is made of S304 stainless steel with a thickness of 4 to 8 mm. The main electronic components are from Schneider, and the pneumatic components are imported from Japan. After the material comes out of the film wrapping machine, it enters the buffer bin and then passes through the automatic quantitative packaging system. The system includes automatic folding and automatic sewing systems to achieve semi-automatic packaging; if high automation is required, a fully automatic packaging system can be selected. The difference lies in whether an automatic bagging machine is used. The latter is more efficient but has a higher investment cost. The packaged compound fertilizer passes through a stacking system made of SS304 stainless steel, using ABB or Fanuc robot arms, with a stacking speed of 1000 to 1200 bags per hour. There are three types: single gripper, double gripper and single machine double steering. Usually a single gripper stacking system is used. The system also includes a conveying and automatic rewinding system. For enterprises that value modernization, our terminals are equipped with pallet warehouses, which are fully automated, but the cost is higher and the requirements on the material and shape of the pallets are strict. For enterprises with limited budgets, conventional wooden pallet systems can be selected.
This extrusion granulation production line uses a two-stage dust removal system to effectively remove dust during production. First, the bag house dust filter removes most of the dust, and then the washing circulation pump injects spray water into the FRP chimney to wash the exhaust gas. The washing water is discharged into the circulating water tank, and the qualified exhaust gas is discharged through the chimney. The rotary drum screen and dryer, cooler, feeding area and packaging area are equipped with dust removal interfaces connected to the bag filter and FRP pipes to ensure efficient dust removal at each dust removal point.

Roll Extrusion Pelletizing LineAdvantages
A small investment in extrusion granulation equipment.
Extrusion granulation equipment occupies a small area.
Extrusion granulation equipment is flexible.
Extrusion granulation equipment is easy to install.
Extrusion granulation equipment has low requirements for operators.
some materials due to their properties can only be granulated using this method such as ammonium chloride
Noted: For Material that has a high moisture level and high phosphorus concentration or organic-inorganic fertilizer this type of granulation method can not be used, otherwise the material will stick to the machine.



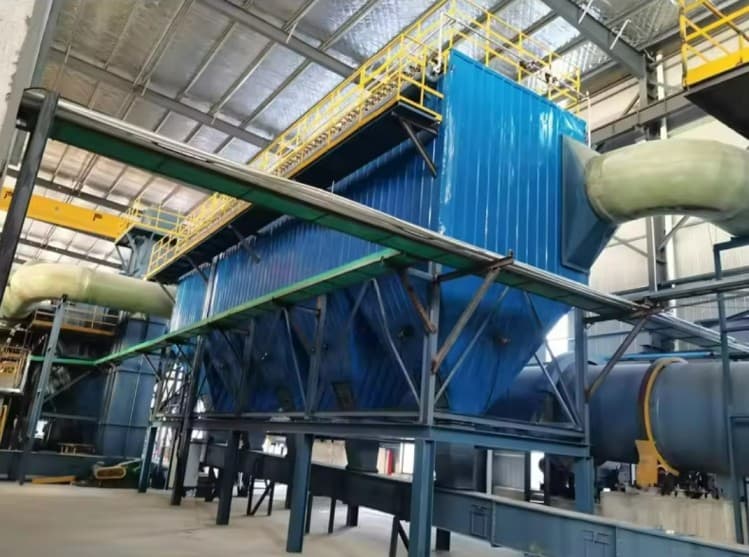
Project Case 2024
- In 2024, Tongli undertook 8 extrusion granulation production lines, 6 projects are in progress, and two projects have been put into production.
- Tongli’s extrusion granulation production line is divided into two types, one is a round granule extrusion granulation production line and the other is an irregular potassium sulfate particle extrusion production line.
- The extrusion production process is increasingly favored by developed countries due to its flexibility and low energy consumption. Although the output is not as good as that of the drum granulation production line, it can be used to make some single-element fertilizers.