High tower prilling
fertilizer Production line
Tongli high tower granulation compound fertilizer production line, with its high output and full compound fertilizer particles, represents the most advanced compound fertilizer production process ranging from 150,000-300,000 tons/year.
High Tower Fertilizer Production Line Equipment List

Raw Material Handling System
- Chainmill
- Dap crusher
- Doubel cage crusher
- Automatic-batching System

Granulation System
- High Pressure Spray granulator
- Emulsification tank
- Urea melting tank
- Stirring tank
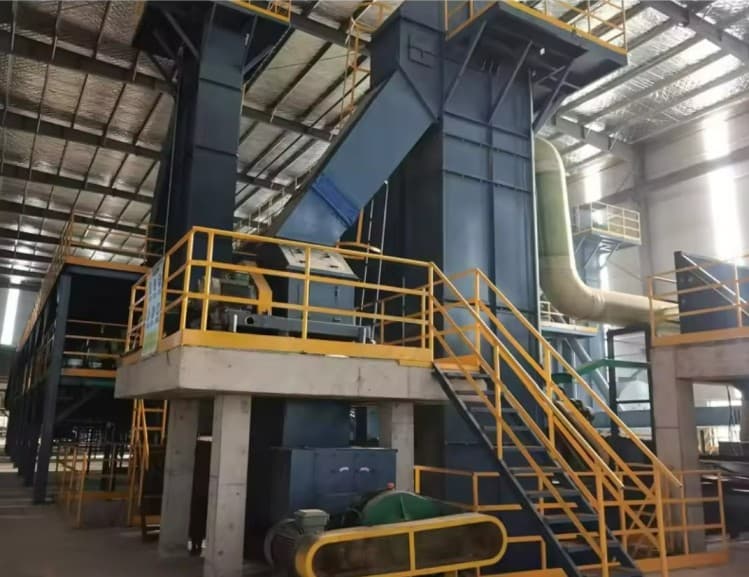
Conveying Equipment
- Belt Conveying Equipment
- Bucket Elevator
- Scraper Conveyor
- Screw Conveyor

Sieving Equipment
- Rotary screener/Trommel
- Vibrating Screener
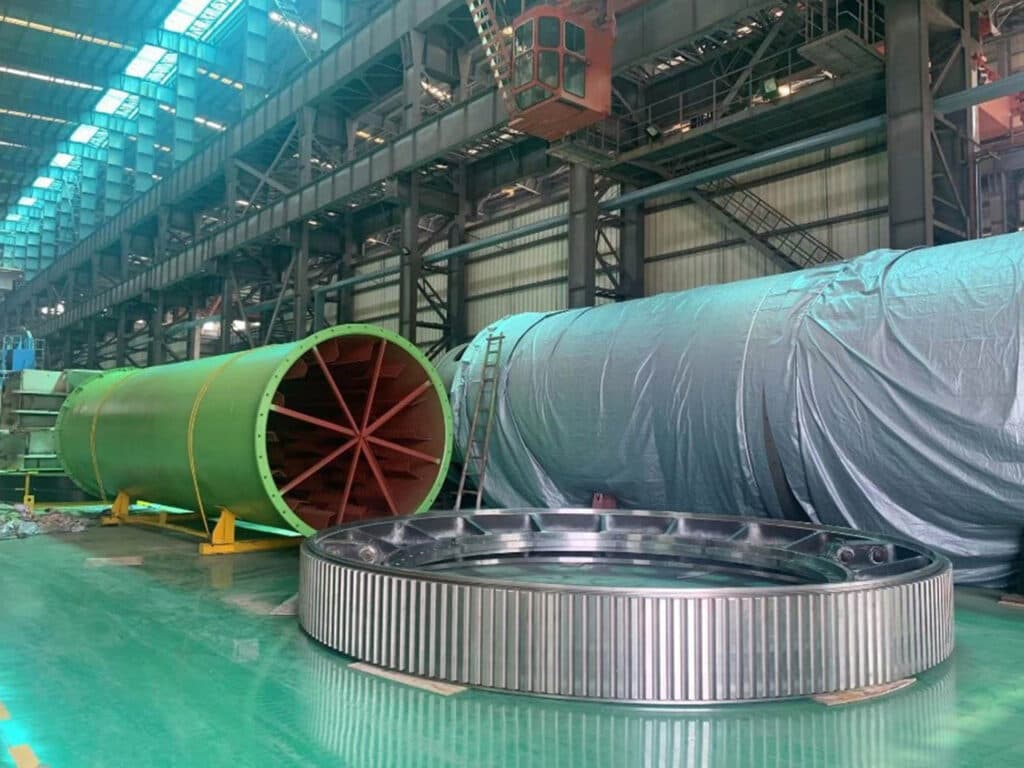
Cooling Equipment
- Drum cooler
- Powder flow cooler

Coating Equipment-high tower
- Rotary drum coating machine

Dedusting Equipment
- Bag house filter
- Cyclone dust collecor
- FRP chimney
- Tail gas washing tower(FRP)

Disc compound fertilizer collector
- Disc compound fertilizer collecting machine

Packing and Palletizing Equipment
- Semi-automatic packaging system
- Fully Automatic packaging system
- Automatic packaging scale
- Automatic Palletizer
Hight tower NPK Compound Fertilizer Production Line Technical Parameters
Equipemnt Name | Capacity | Parameter | Quantity | Power(kw) |
Measuring belt scale | 20t/h | B650,L=2200mm | 8 | 1.5+1.5 |
Buffer silo | 1.72 m3 | 1200x1200x1200mm | 8 | N/A |
Chainmill/Bulk crusher | 50t/h | FS800 | 3 | 22kw |
Bucket elevator | 50t/h | TGD500x108m | 3 | 35kw |
Urea melting tank | 30t/h | 2200*2000*2000mm | 1 | 5kw |
Fluid Mixing tank | 50t/h | 1800*2000mm | 2 | 3kw |
Emulsifier | 80t/h | TL-800 | 2 | 3kw |
High tower granulator | 80t/h | H:108m D:20m | 2 | 22kw |
High tower rotary cooler | 150t/h | 2.0x24m | 1 | 132kw |
Screening machine | 150t/h | 2.2x8m | 1 | 22kw |
Powder flow cooler | 150t/h | 2000x1500x8000 | 1 | 15kw |
Coating machine | 150t/h | 2.2x8m | 1 | 45kw |
Automatic Packing system | 75t/h | LCS-50 | 2 | 7.5kw |
Bagging Machine | 75t/h | TL-500 | 2 | 10kw |
Palletizing robot | 75t/h | ZJ-75 | 2 | 22kw |
Raw materials for high-tower fertilizer production line

Urea
Urea is the main raw material of high tower compound fertilizer. It is an organic compound composed of carbon, nitrogen, oxygen and hydrogen. Its chemical formula is CO(NH2)2, molecular weight is 60.06, and density is 1.335g/cm3.The main principle of high tower compound fertilizer is to use the clean characteristics of urea after melting

MAP
Monoammonium phosphate, also known as MAP, is the main source of phosphorus in high-tower compound fertilizers. Its chemical formula is NH4H2PO4. When heated, it decomposes into ammonium metaphosphate (NH4PO3), which can be made by reacting ammonia water and phosphoric acid.

Potassium chloride
Colorless, elongated rhombus or cubic crystals, or white crystalline small granular powder, looks like table salt, odorless, and tastes salty. It is often used as an additive for low-sodium salt and mineral water, and is also a major raw material for fertilizer production.

Potassium sulfate
Potassium sulfate is an inorganic salt with the chemical formula K2SO4. It has good physical properties and is easy to apply. It is a very good water-soluble potassium fertilizer and the main raw material for making chlorine-free nitrogen, phosphorus and potassium ternary compound fertilizer.

Ammonium chloride
Ammonium chloride, with the chemical formula of NH4Cl, contains 24% to 26% nitrogen. It is white or slightly yellow in the form of small square or octahedral crystals. It is easy to store. Powdered ammonium chloride is mostly used as a basic fertilizer for the production of compound fertilizers.
High Tower fertilizer Production Process
Urea, monoammonium phosphate, potassium chloride, potassium sulfate, ammonium chloride, ammonium sulfate and additives are transported to the pit feeding port manually, and the raw and auxiliary materials are put into the pit for temporary storage through the feeding port. The raw material metering configuration of this project adopts a computer automatic batching system. Each raw material is equipped with a metering belt as the feeding port. The feeding port is leveled with the floor of the workshop feeding area for easy operation. This project has 3 groups of raw material batching systems. Batching and metering are all completed in the pit. For easy operation, the pit is designed to be wide enough and all covered.
Group 1 raw material batching system: 2 metering belt scales are set up, mainly for urea metering. After being measured by the batching metering scale, urea is transported to the melting tank by the urea scraper and the urea high tower bucket elevator. It is heated by steam to 120℃ and melted into liquid. After melting, it is transported to the primary mixing tank. Urea is unstable when exposed to heat. It will deaminate into biuret at 160℃. The condensation reaction formula is: 2 (NH2) 2CO = NH2CONHCONH2 + NH3. The temperature of this process is controlled at 120℃. The material will not decompose in large quantities. Only a small amount of material will decompose to produce a small amount of NH3. Steam is provided by a natural gas steam boiler, which will produce natural gas combustion exhaust gas.
Group 2 raw material batching system: 4 metering belt scales are set up, mainly for potash fertilizer and ammonium fertilizer (potassium sulfate, potassium chloride, ammonium chloride, ammonium sulfate). The agglomerated potash fertilizer and ammonium fertilizer are first crushed by bulk crusher or chaincrusher or sometimes cage crusher, then measured by metering belt, and then conveyed to the first mixing tank by scraper and high tower hoist for mixing and then conveyed to the second mixing tank.
Group 3 raw material batching system: 2 weighing scales are set up, mainly for phosphate fertilizer (monoammonium phosphate). The agglomerated phosphate fertilizer is first crushed by the cage crusher or ton bag crusher, then weighed by the weighing belt, and then conveyed to the secondary mixing tank by the scraper conveyor and the high tower elevator.
The mixed raw materials enter the emulsifier for emulsification. In the emulsification process, an appropriate amount of water is added to make the materials melt into liquid faster. No chemical reaction will occur during the emulsification of the raw materials in this project. The temperature is controlled at 120℃ when the materials are heated and mixed. According to the physical and chemical properties of the raw and auxiliary materials in this process, urea is unstable when exposed to heat. It will be deaminated into biuret at 160℃. The condensation reaction formula is: 2(NH2)2CO=NH2CONHCONH2+NH3; monoammonium phosphate will decompose at 190℃, lose ammonia and water, and form a mixture of ammonium metaphosphate and phosphoric acid. The reaction formula is:
2NH4H2PO4=NH4PO3.H3PO4+NH3+H2O. At 100°C, only a very small part of it will be decomposed by heat (in actual production control, ammonium phosphate is added to the secondary mixing tank and stays there for no more than 2 minutes. The purpose is to shorten the contact time with urea and reduce the decomposition to produce NH3). It can be seen that when the temperature of this process is controlled at 120°C, the material will not decompose in large quantities. Only a small amount of urea and monoammonium phosphate will decompose and produce a small amount of NH3 during the heating, melting and mixing process. The heat source for emulsification comes from the natural gas steam boiler, which produces natural gas combustion exhaust gas.
The working principle of high tower granulation is to first emulsify the mixed material into the high pressure spray granulator for granulation. The mixed slurry with certain fluidity and viscosity is sprayed into small liquid particles through the nozzle at the top of the 117m high tower. Due to surface tension, it becomes spherical small liquid particles when scattered. During the descent of the liquid particles in the high tower, they interact with the resistance of the cold air entering from the bottom of the tower and exchange heat with it, so that the liquid particles are cooled and solidified to form compound fertilizer particles with a certain strength. The particles collide with each other and fall into the disc collector at the bottom of the tower under the action of gravity. Then the finished product out of the tower is collected by the belt to send the semi-finished compound fertilizer to the rotary cooling machine first and then lifted to the powder flow cooler. After the temperature of the particle is cooled down, the finished product will enter the rotary coating machine to apply the coating on the surface and proceed to the packaging process. High tower granulation is mainly the process of cooling the liquid material into solid granular material by gravity and cold air. The production process does not involve chemical reactions. The high tower granulator is located inside the granulation tower. The granulation tower works in a closed manner. The exhaust gas is discharged through the exhaust port of the granulation tower equipment to the 2# cyclone dust collector + 2# bag dust collector + 2# washing tower water washing + demister treatment, and then discharged through the tower top exhaust pipe DA003 to meet the standards.
After the materials are collected from the Disc collector of the high tower compound fertilizer, they are transported to the drum screener through long-distance belt conveyors and bucket elevators. Drum screeners are usually used for high tower compound fertilizers because vibrating screeners have high dust emissions and are not suitable for high tower compound fertilizers. During the screening process, two screenings are performed: primary screening and fine screening. Unqualified size materials will be returned to the chain crusher for re-crushing and then lifted to the top of the tower for re-granulation. Finished products with qualified size enter the next cooling process to ensure product quality and uniform particle size. This process optimizes production efficiency, reduces dust emissions, and improves the quality of finished products.
The temperature of the compound fertilizer particles produced by high tower granulation is about 70~80 degrees. After being screened by the drum screener, they will enter our drum-type compound fertilizer cooler. The main function of the cooler is to cool the compound fertilizer particles, because high temperature will affect the quality of the particle coating and thus affect the appearance and preservation performance of the compound fertilizer. Our cooler adopts a convection design, with air supplied by the centrifugal fan at the tail, and the material contacts the opposite direction of the air supply airflow, thereby improving the cooling effect. Similarly, a hammer device is also installed at the tail to reduce the material sticking to the wall.
Coating is a key process in compound fertilizer production. Its function is to introduce the finished product after the rotary screening machine and the cooler into the coating machine for surface treatment. The coating process of organic fertilizer is slightly different from that of inorganic fertilizer, mainly because the color of inorganic fertilizer can be adjusted freely. Inorganic fertilizer is usually pure white, and can be made into finished products of various colors through coating. However, organic fertilizer has brown color due to the addition of organic matter (such as cow dung and sheep dung). The color of the finished product can only be brown, and it cannot be brightly colored. This is the main difference between organic fertilizer and inorganic fertilizer in the coating stage.
The coating machine system is relatively complex. In addition to the coating machine itself, it also includes a coating oil tank for providing coating oil, and an automatic batching scale for controlling the amount of compound fertilizer entering the coating machine. The amount of coating oil needs to match the proportion of the finished product ingredients, so a DCS control system is required to adjust the speed of automatic batching and the amount of coating oil.
During the coating process, an anti-caking agent screw conveyor is also provided to prevent the organic compound fertilizer particles from agglomerating or flying. The anti-caking agent is quantitatively supplied to the coating machine through DCS control to ensure that the anti-caking agent and coating oil are evenly distributed in the finished product to prevent the particles from agglomerating or flying. The strength of the organic compound fertilizer particles after coating can usually reach about 15 Newtons.
Regarding the finished product packaging machine of compound fertilizer, we provide two solutions: one is a semi-automatic packaging system and the other is a fully automatic packaging system. The traditional double-cylinder packaging scale has been eliminated, and now the main automatic quantitative packaging scale with servo motor is used. This servo motor packaging scale is faster and more accurate, and the packaging speed can reach 800 to 1,000 bags per hour. The scale body of the packaging scale is made of S304 stainless steel, with a thickness ranging from four to eight millimeters. The main electronic components are from Schneider, and the pneumatic components are imported from Japan. After the material comes out of the fertilizer coating machine, it first enters the buffer silo of the product packaging scale, and then passes through the automatic quantitative packaging below. The system is also equipped with automatic folding and automatic sewing systems to achieve semi-automatic packaging. If you have high requirements for automation, then the fully automatic packaging system will better match your needs. The difference lies in whether the automatic bagging machine is used in the bagging process. The automatic bagging machine can improve efficiency and save labor, but the investment cost is higher.
After the finished compound fertilizer is weighed and bagged on the packaging scale, it enters the palletizing system. The system mainly consists of an all-stainless steel SS304 conveying system and support legs. After the fertilizer bags are packaged, they are transported one by one by the conveyor belt to the bottom of the palletizing robot for palletizing. We usually use ABB or Fanuc robotic arms, with reliable steel trusses and speeds of up to 1,000 to 1,200 bags per hour. There are three types of palletizers: one machine and one rudder, which is the most common form; one machine and two rudders, suitable for high-output production lines; and a single-grip palletizer system, although double grippers are less commonly used. In addition, the system is also equipped with a conveying system and an automatic rewinding system.
For companies that attach great importance to factory modernization, our terminals are also equipped with a pallet warehouse to make the entire process fully automated, but the cost is also higher. The automated pallet warehouse has very strict requirements on the material and shape of the pallet, so for companies with limited budgets, we do not recommend a palletizer system with a pallet warehouse. On the contrary, if the automation requirements are not high, you can choose a conventional wooden pallet system without a pallet warehouse. This setting is not only economical but also meets basic production needs.
The high tower granulation tower is a highly efficient fertilizer granulation equipment, mainly used for granulation of solid fertilizer melt. The main equipment includes three parts:
- The first is the tower body. The granulation tower is the main equipment for high tower granulation to produce granular compound fertilizer. The main function of the granulation tower is to crystallize the compound fertilizer and cool and exchange heat in the tower. The diameter and height of the granulation tower are the main indicators of the equipment, which are closely related to the production capacity and quality of the product.
- The second is the granulator Equipment, the granulator can meet the requirements of compound fertilizer granulation for various slurries according to needs, especially for the granulation of medium and low nitrogen varieties of compound fertilizers. It has very good performance;
- The third is the mixing tank. The main function of the mixing tank is to fully stir and mix the materials in the equipment to achieve the purpose of preparing mixed slurry with good flow properties. The working principle of the high tower granulator is to first emulsify the material, and then spray the mixed slurry with a certain fluidity and viscosity on the top of the 117m high tower through a nozzle. Due to surface tension, the mixed spherical liquid particles are formed when scattered. During the process of the liquid particles falling in the high tower, they interact with the resistance of the rising cold air entering from the bottom of the tower, and exchange heat with it, so that the liquid particles are cooled and solidified to form compound fertilizer particles with a certain strength. The particles collide with each other and fall into the disc collector at the bottom of the tower under the action of gravity.
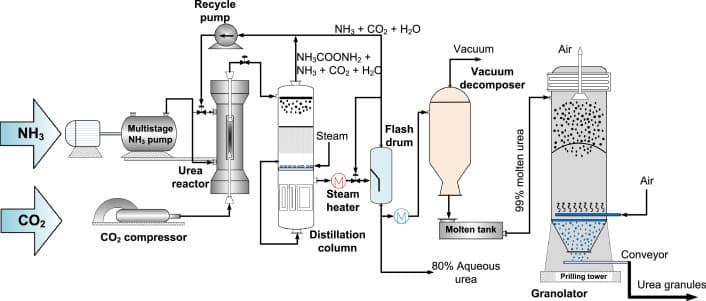
High tower fertilizer Production Line Advantages
- The first advantage of high-tower compound fertilizer is its high yield. The height of domestic high towers is usually between 120 meters and 128 meters, and the annual output can reach about 250,000 tons to 300,000 tons, which gives high-tower compound fertilizer a significant advantage in output.
- The second advantage of high-tower compound fertilizer is that it adopts a urea melting process, and the compound fertilizer produced is a real compound fertilizer, while the one created by traditional drum process can only be called compound fertilizer. Urea is quickly cooled and crystallized after melting, making the granule composition more uniform and the appearance more beautiful.
- The third advantage of high-tower compound fertilizer is that its process route is short, the high-tower melting process is adopted, the number of equipment is small, the degree of automation is high, the production efficiency is significantly higher than the traditional drum compound fertilizer production process, and the equipment failure rate is also low.
- The fourth advantage of high-tower compound fertilizer is stable product quality. Due to the short process route, the fertilizer produced is very stable in both composition and strength and is not easy to stratify, thus ensuring the consistency and reliability of the product.
- A significant advantage of high-tower compound fertilizer is its small investment and small footprint. Generally speaking, the equipment required for a high-tower compound fertilizer production line (excluding the raw material warehouse and finished product warehouse) occupies an area of about ten acres. Compared with the conversion production line with the same output (such as an annual output of 250,000 tons or 300,000 tons), the investment cost of the high-tower production line is lower. This not only reduces the company’s initial investment, but also reduces the space requirements for production facilities, making it more suitable for factories with limited land resources. At the same time, the high-tower production line also has advantages in process efficiency and product quality, further enhancing the competitiveness of the company.


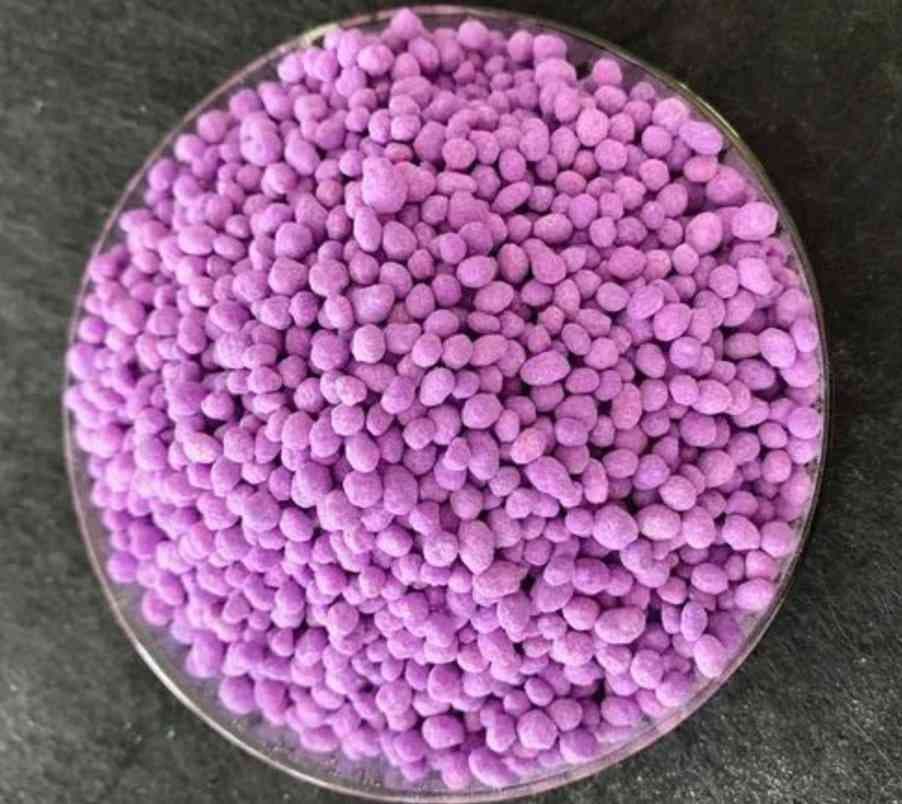
Project Case 2024
- As of 2024, Tongli has EPC more than 25 production lines in China, with an annual output ranging from 200,000 tons to 300,000 tons.
- As the largest high-tower compound fertilizer equipment manufacturer in China, Tongli has been committed to the production and research and development of high-tower compound fertilizer equipment for many years.
- Since the height of the high-tower compound fertilizer is 120 meters and the design of the granulation tower body requires approval from many government departments, Tongli currently has no overseas cases. Currently, it is negotiating with Jordan’s 300,000-ton annual high-tower compound fertilizer production line and Thailand’s 200,000-ton annual high-tower compound fertilizer production line.