Dedusting Bag Filter System
Dedusting Bag Filter System
On the basis of the design and manufacturing experience of the Dedusting Bag Filter System, a new generation of low-pressure long-bag pulse dust collectors has been developed and designed in combination with the requirements of ultra-low emission in the steel and machinery industries.
The product retains the advantages of the original long-bag pulse dust collector and gives full play to the advantages of pulse blowing. The product adopts temperature-resistant, corrosion-resistant, and high-filtration precision filter media, which is applied to the ultra-clean filtration of flue gas from iron and steel yards, mine slots, converters, electric furnaces, and sintering machines to meet the requirements of ultra-low emission.
The products have been developed to meet the requirements of various air volumes of iron and steel high-efficiency bag filters and can also be used in other types of large-scale dust removal projects.
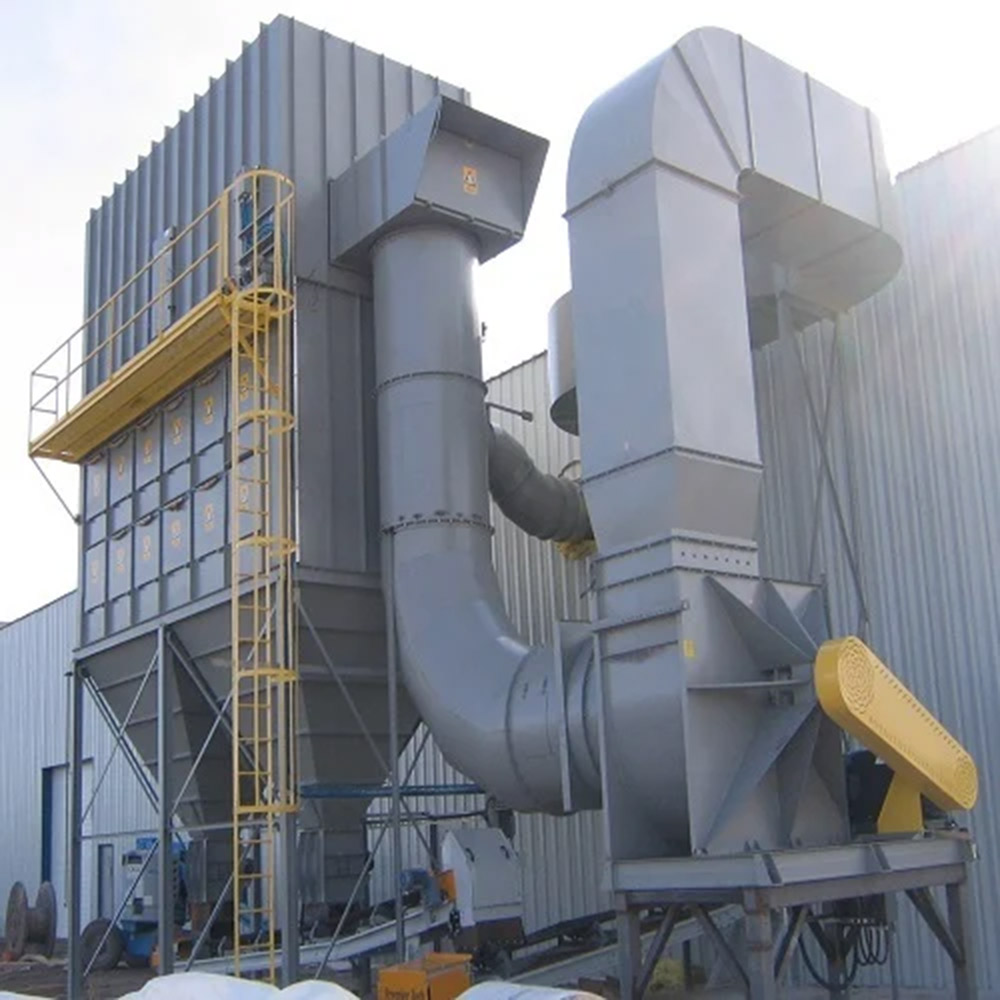
Advantages of Fertilizer Dedusting Bag Filter System
- High reliability design, long-term stable operation, and less maintenance.
- High adaptability design, the dust collector can be adapted to a wide range of dusty gases
- Optimized inlet and outlet duct design, conducive to uniform airflow distribution;
- Anti-leakage design ensures that the air leakage rate of the bag collector is reduced to a low level;
- Split structure design, easy transportation and installation of the equipment, and ensure the manufacturing precision of the equipment.
- Perfect series design, can meet the dust treatment needs of a variety of dust sources.
Dedusting Bag Filter System Applicable Materials

Iron and steel industry
Dedusting of Blast Furnace Gas, Converter, Electric Furnace: The dust in the blast furnace gas is characterized by high concentration, viscous, easy to condensation, etc. Capturing the soot generated in the steelmaking process, the baghouse dust collector can effectively remove these dusts and protect the subsequent equipment.


Crushing Compound Fertilizers
Double Cage Crushers are used to break down compound fertilizers into smaller particles, ensuring consistent nutrient distribution and improved handling characteristics.


Cement Industry
Cement production line: Bag filter is used to capture the dust generated during the cement production process, such as the dust generated by the raw mill, cement mill, packing machine, etc. The bag filter is used to capture the dust generated during the cement production process.

Dust collector working principle

Pulse dust collector working principle and characteristics summary
The dust collector is a kind of highly efficient dust removal equipment, which mainly realizes the purification of dusty gas through the following ways:
- Split chamber structure and middle duct air inlet: This design distributes the dusty gas to each filter chamber and improves dust removal efficiency.
- Multi-stage dust removal: Before entering the filter bag, the dust particles go through multi-stage treatment, such as baffle folding, inertia gravity, and ash hopper settling, which significantly reduces the load of the filter bag.
- Low-pressure and large-diameter-blowing dust cleaning: Advanced dust cleaning technology is adopted to ensure that each filter bag can be thoroughly cleaned, prolonging its life.
- Corrosion-resistant materials: the internal use of shot blasting and high-quality coatings to extend the service life of the equipment up to 15 years or more.
- Well-designed filter bag skeleton: adopts multiple longitudinal bars with high strength and smooth surface, reducing friction with the filter bag and prolonging the filter bag’s service life.
- Small blowing unit: reduces the blowing area and has a negligible impact on the system air volume.
- Flexible control mode: provides centralized control and machine-side control, realizes two kinds of ash cleaning mode with fixed resistance and timing, and can be monitored by the HMI upper computer.

Serving People for More Than 12 Years With Over 95% Satisfied Customers.
- Dust Accumulation: Dust accumulates on the filter bags over time.
- Pressure Increase: The pressure drop across the filter increases as dust accumulates.
- Cleaning Cycle Initiation: When the pressure reaches a preset level, the PLC control system initiates a cleaning cycle for a specific compartment.
- Airflow Isolation: A solenoid valve isolates the airflow in the designated compartment.
- Compressed Air Injection: A short burst of compressed air is injected into the filter bag through a jet nozzle.
- Bag Inflation: The compressed air creates a venturi effect, drawing clean air from the clean air chamber and inflating the bag sequentially from top to bottom.
- Bag Vibration: The inflated bag fabric rapidly vibrates at a high frequency due to the exerted force.
- Dust Dislodgement: This rapid vibration dislodges dust cake adhering to the outer surface of the bag.
- Filtration Resumption: After a brief pause for dust settling, the solenoid valve reopens, allowing the compartment to resume filtration.
- Cycle Repetition: The cleaning sequence then moves on to the next compartment, and this cycle repeats continuously.
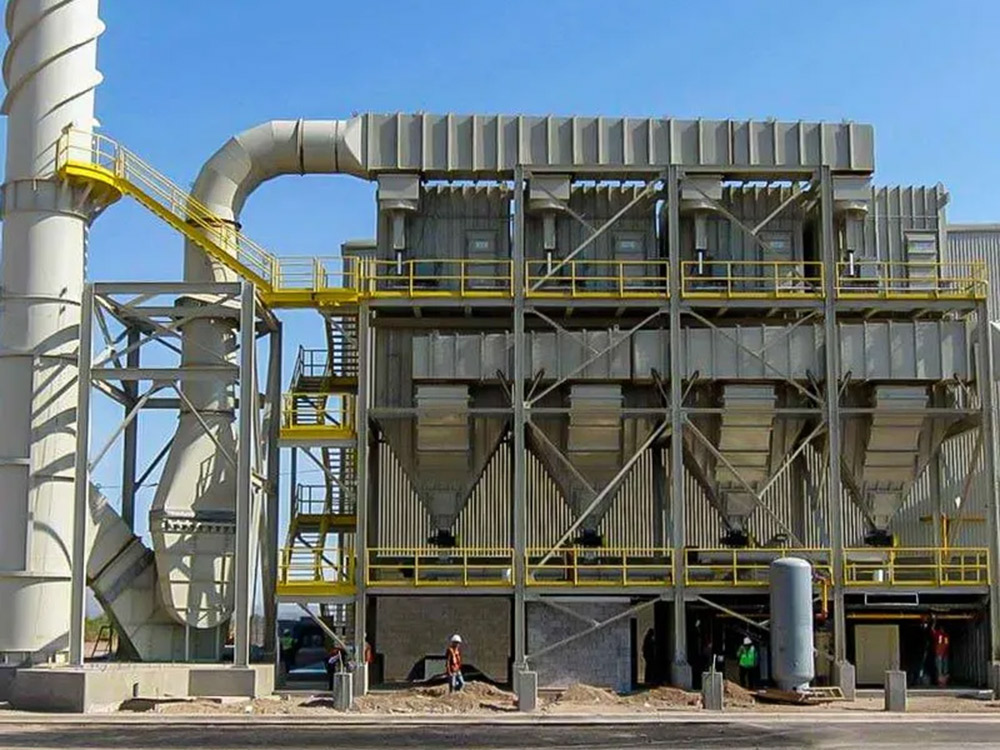
Serving People for More Than 12 Years With Over 95% Satisfied Customers.
- Diversified control methods:
Manual control: manual operation to control the ash cleaning process. - Automatic control: The PLC control system automatically performs ash cleaning according to the set parameters.
Time program control: cleaning according to the preset time interval, suitable for relatively stable working conditions.
Differential pressure control: Trigger the ash cleaning according to the change of differential pressure on the filter bag, which can respond to the blockage of the filter bag in a more timely manner.
Time-differential pressure hybrid control: combining time and differential pressure control, taking into account the advantages of the two methods, is more adaptable. - Flexible setting of critical parameters:
Pulse width: generally 0.1~0.15 seconds, control the time of compressed air blowing, affecting the effect of ash cleaning.
Pulse interval: generally 10~20 seconds; control the interval between two clearing times, affecting the clearing frequency.
Cycle interval: generally 30~90 minutes; control the whole cycle’s time, affecting the ash cleaning efficiency.
Compressed air pressure: generally 0.25~0.35MPa, according to the pulse valve’s and blowing parameters’ specifications, affecting the ash cleaning’s intensity. - PLC control system: The PLC control system realizes the automatic control of the ash-cleaning process, which improves the efficiency and accuracy of ash-cleaning
Dedusting Bag Filter System Outline Drawing


What Else Does TONGLI offer?
Our Products
We are the industry heads and produce the most reliable and trendy fertilizer production line solution you are looking for.
NPK compound fertilizer steam granulation solution
Suitable for making compound fertilizers, organic fertilizers and mixed fertilizers with diversified formulas with large output
NPK roller extrusion granulation method production
Save energy consumption, flexible output, small investment
High tower prilling method npk fertilizer production
Large investment, large output, suitable for making high-nitrogen NPK compound fertilizer
BB fertilizer blending line
Small investment, flexible output, and can mix a variety of formulas
The only place where you’ll get the perfect solution for fertilizer industry needs.
Frequently Asked Questions
1. Installation: After the machine arrives at the factory, it will be installed in conjunction with the process, indicating the elevation and horizontal position, tilted installation, generally tilted at 2-5 degrees (which can be adjusted to make the user’s needs), and the machine bracket and transmission frame even ground angle holes, which can be mounted on rolled condensed soil.
① machinery each base and the foundation between the pad into the deed-shaped mat board thickness should not be greater than 30-35mm;
② the height of the base with the deed-shaped pad to adjust the height of the base to make the base 5 degrees of inclination;
③ After each base is adjusted properly, put the cylinder on the support and adjust the carrier wheel;
④ Install the drive part of the film wrapping machine;
⑤ Be sure that the bracket wheel, transmission device and cylinder are properly adjusted and start pouring cement, and after 8-10 days, start the no-load test run after the cement is solidified;
⑥ Method of adjusting the position of the machine body:
a. On the full length of the left and right sides of the machine body, install two parallel steel wires with a diameter of 0.5-1mm and check the level of the wires with a level meter;
b.Lower two phase hammers tangent to the rolling circle from each rolling circle down the sides of the dryer;
c.Measure the distance from the steel wire to the wire drop to detect the body in the horizontal position;
d. Measure the relative vertical elevation of the two rolling circles to check the position of the machine body in the vertical plane;
e. Use the method of moving the electric torque wheel to adjust the measurement of the two articles c and d, so that the machine body is in the correct position;
2. No-load test run:
1). Uninterrupted no-load for 8 hours, the temperature of each bearing should rise smoothly, and the temperature of the bearing should not be higher than 50 degrees Celsius at the termination of the test run;
2). The noise of gears should be average and should not be high or low;
3). After the test run, the bearings shall be observed without serious wear and abrasion.
A.Starting the machine
1. The following preparations should be made before starting the film wrapping machine;
a. Check and adjust the powder feeding device and protection equipment;
b. All bearings and lubricating devices of friction surfaces should have appropriate quantity of grease;
2. It is forbidden to start the film wrapping machine without checking the film wrapping machine and auxiliary mechanical equipment;
3. The steps to start the film wrapping machine are as follows:
a. Start the motor of the film wrapping machine.
b. Start the feeding and discharging conveying equipment.
B. Stopping
1. The steps to stop the film wrapper are as follows:
A. Stop adding raw material to the wrapper;
B. Turn off the drive motor of the wrapping machine;
C. Stop the equipment for transporting granular materials;
1. Dry grease should be smeared at the gears before starting the machine;
2. Dry grease to be smeared on the surface of rolling belt once in 7 days;
3. Bearing housing to be hit or renewed with new dry grease every three months;
4. Add gear oil once before the reducer is used and replace it every four months thereafter;
Pinion gear is worn, install pinion gear upside down, if both sides are worn, new gear is needed.
The intermediate connection between the large gear and the cylinder is damaged, adjust the connection and make appropriate treatment if necessary.
Clamping roller belt to the side of a concave joint
Clamp the belt to the concave joints with pads or wedges, but beware of over-clamping, which can lead to accidents, but uneven tensioning can cause the machine to jump and vibrate.
Wheel wear Refurbish or replace the wheel according to the degree of wear
Block wheel wear Repair, move, or replace with new block wheel depending on degree of wear
Simple body vibration