Granulator Machine for Fertilizer
Fertilizer granulator is an indispensable machinery and equipment in modern agricultural production, which is capable of accurately processing all kinds of fertilizer raw materials into granules with specific shapes and sizes. These granular fertilizers are not only easy to store and apply, but also significantly improve the uniformity and application efficiency of fertilizers, thus optimizing nutrient uptake by crops.
As the right-hand man for fertilizer manufacturers, granulators can be used to produce a wide range of fertilizers, including organic, bio-organic, and compound fertilizers. When you’re considering investing in a fertilizer pelletizer, we have an extensive product line that offers a wide range of high-quality pelletizing solutions. With years of experience in fertilizer machinery manufacturing, we are able to not only provide highly efficient equipment to accommodate the wet pelletizing process, but we can also custom design dry pelletizers to meet your specific needs, ensuring that your production requirements and business goals are met.
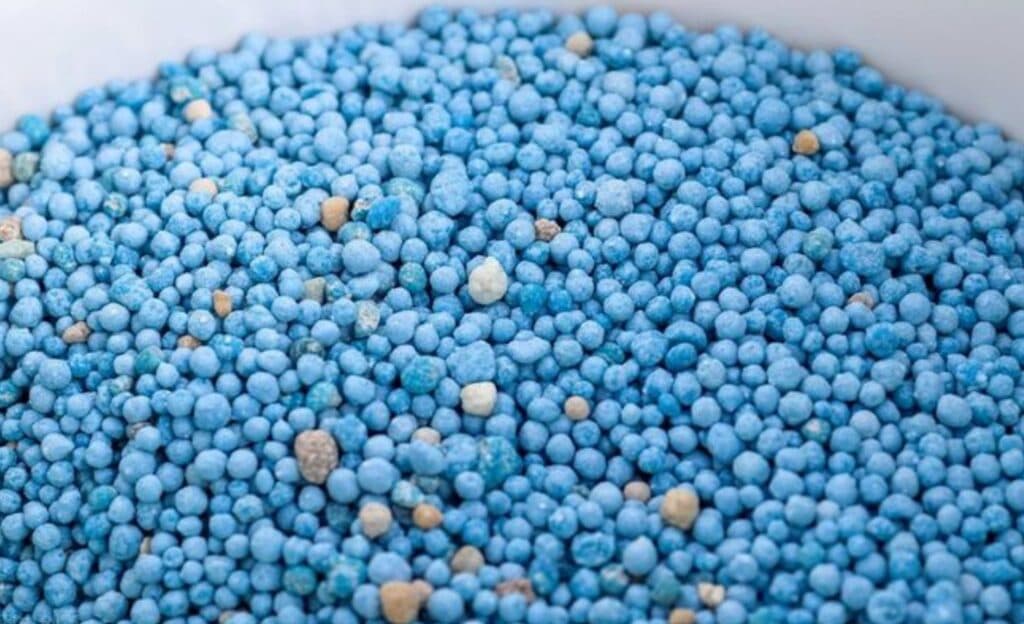
Common methods of fertilizer granulation
Fertilizer granulation technology is a key part of the fertilizer production process, which is mainly divided into two methods: wet granulation and dry granulation. Each method has its own unique conditions and operational advantages.
Wet granulation
Wet granulation is particularly suitable for raw materials with high moisture content, typically between 40% and 50%. The process involves adding the right amount of water and binder to the feedstock to facilitate particle formation. Wet granulators utilize mechanical forces or chemical action to efficiently agglomerate and shape the feedstock particles into the desired shape. This method not only improves the agglomeration of the raw material, but also ensures uniformity and stability of the granules.

Dry granulation
In contrast to wet granulation, dry granulation is suitable for raw materials with low moisture content. In this process, no additional water is added, but rather the powdered raw material is directly converted into solid granules by mechanical forces, such as extrusion or compression. The design of dry granulators allows direct granulation of the raw material without relying on moisture by adjusting pressure and temperature, thus saving drying costs and reducing energy consumption.

Common fertilizer granulator
According to the granulation method, fertilizer granulator can be roughly divided into two main types:
Wet method granulator
Wet granulation is to add water or binder to the powdered raw materials, so that the raw materials are bonded to form particles when passing through the granulator. This method is usually used to produce organic fertilizer and compound fertilizer with high water content.
Common wet granulation granulator:
Disc Granulator
The disc granulator, also known as flat disc granulator, is a widely used tool in the field of fertilizer manufacturing. It operates through a stacked pelletizing concept that converts powdered resources into granules through centrifugal force and the addition of liquid binders.
The disc pelletizer consists of pelletizing disc, drive unit, angle adjusting unit, frame, liquid nozzle, scraper and so on. In addition, the equipment is equipped with three discharging ports, which facilitates intermittent production, reduces labor intensity and improves work efficiency.
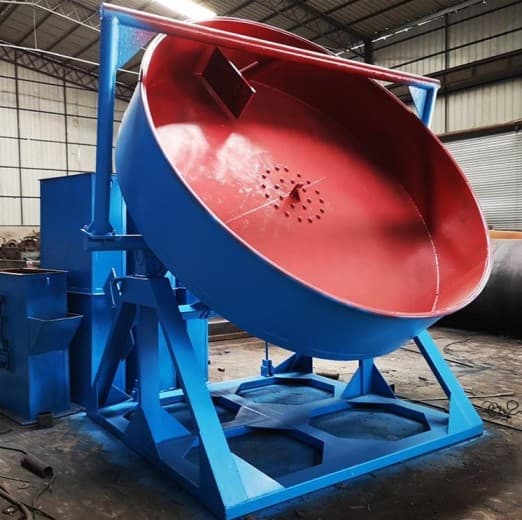
Working Principle
The working principle of disc granulator is based on wet granulation technology. The fermented organic fertilizer powder is conveyed into the granulator, and with the rotation of the granulating disc, the fertilizer powder moves along the edge of the disc under the action of gravity and centrifugal force. At the same time, the spraying equipment sprays binder or water to transform the fertilizer powder into granules. After several cycles, the granules gradually become bigger and bigger, and finally form qualified granules, which accumulate in the lower part of the disk and overflow from the edge to the next production stage.

Disc Granulator for Sale
Applicable raw materials
Our granulator is suitable for all organic fertilizers made from fermented organic waste, including livestock and poultry manure, agricultural waste, municipal sludge, food waste and other organic waste. In addition to organic fertilizers, the disc granulator is also suitable for the granulation of compound fertilizers.
Our disc granulator adopts the whole round structure, and the granulation rate is as high as 93%. In addition, the machine adopts the wet granulation principle, which allows you to add the right amount of granule binder during the granulation process and even some functional bacteria to produce bio-organic fertilizers.
New Organic Fertilizer Granulator
New Organic Fertilizer Granulator, also known as Wet Stirring Granulator, makes the granulation process easier by using a certain amount of liquid or steam to moisten the powdered organic fertilizer. The equipment utilizes the mechanical stirring force of high-speed rotation and the resulting pneumatic force to achieve granulation. By this method, the organic fertilizer powder completes the mixing, granulating, balling and densification process inside the machine, finally forming uniform granules.
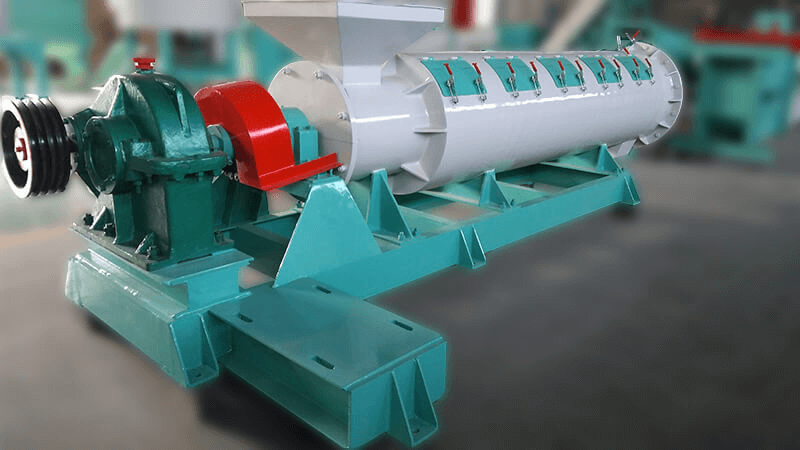
Structure of new organic fertilizer granulator
The granulating equipment consists of main frame, granulating rotor with spiral arrangement of stirring teeth and transmission parts. Raw materials are added through the funnel-shaped inlet, and under the rotating action of the spiral stirring teeth, the powdered organic fertilizer is gradually transformed into granules and pushed to the discharging end. Then, the finished granules can be collected at the discharging end for further processing.
New organic fertilizer granulator applicable raw materials
As our patented product, the new organic fertilizer granulator is suitable for granulation of organic fertilizers made from various organic wastes, including but not limited to:
- Livestock and poultry manure: chicken manure, pig manure, cow manure, etc.
- Agricultural waste: corn stalks, rice straw, edible fungi waste, etc.
- Household waste: food waste from canteens and restaurants, food waste, etc.
- Industrial waste: soybean meal, sugar mill filter sludge, etc.
- Other uncommon wastes: sludge, earthworm fertilizer, bat guano, etc.
Rotary Drum Granulator
Rotary Drum Fertilizer Granulator, plays a vital role in the compound fertilizer industry. Capable of converting raw materials into uniform spherical pellets, this machine is favored for its excellent processing capacity, economical energy consumption, and low maintenance costs. It is not only suitable for hot and cold granulation processes, but also efficient for large-scale production and suitable for manufacturing compound fertilizers of various consistencies.
Optimized features of rotary drum fertilizer granulator
- High-efficiency anti-adhesive lining: The internal PVC plastic plate or stainless steel plate is used as the lining, which effectively prevents the material from adhering and ensures the smooth production process.
- High-strength granule production: Ensure the granules have high compressive strength and excellent appearance, which enhances the market competitiveness of fertilizers.
- Durable design: The anti-corrosion and wear-resistant characteristics of the equipment significantly extend its service life, while simplifying the operation and maintenance process.
- High granulation rate: the granulation rate is more than 70%, which significantly reduces the return material and waste material, optimizes the production efficiency, and enables regranulation of even small granular fertilizers.
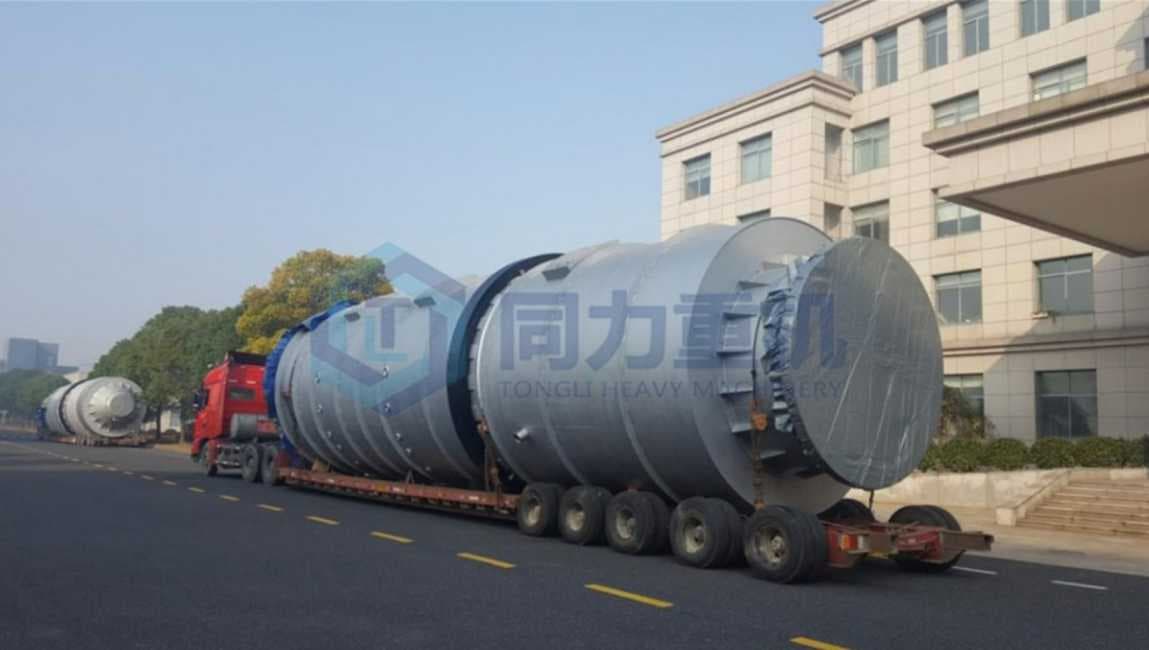
Working Principle of Rotary Drum Fertilizer Granulator
The working process of rotary drum fertilizer granulator is highly efficient and automatic. Raw materials are fed into the rotating drum of the granulator through a belt conveyor. The continuous rotation of the drum drives the material to form a rolling bed that moves along a preset path. The material aggregates into small particles as it rolls and extrudes to form a pellet core, to which the powdered raw material then adheres and gradually develops into qualified spherical pellets. The inclined design of the drum allows the pellets to flow smoothly out of the outlet, while the internal shovel plate assists in pelletizing the material and cleaning the equipment.
Application of Rotary Drum Fertilizer Granulator
The Rotary Drum Fertilizer Granulator is suitable for tens of thousands of tons of fertilizer production lines per year, providing a stable and reliable granulation solution for both large-scale production and medium-scale manufacturing needs.
The advantage of wet granulation is that it can produce firm spherical particles at 20%-40% moisture content, saving energy and equipment, and improving efficiency. However, drying is required after granulation.
Dry Granulator
For scenarios where wet granulation is not suitable, dry granulators offer an effective solution. Dry granulators can press and mold powdery or granular raw materials directly at room temperature without the need for wetting treatment and drying process. Common dry granulators include:
NPK fertilizer double roller extrusion granulator
Fertilizer double roller extrusion granulator is the key equipment in the process of compound fertilizer granulation. As a new research and development of fertilizer roller compaction granulation equipment, it can realize the granulation of materials at room temperature, without drying process, significant energy savings and cost reduction. It is characterized by low investment, high return and quick effect, which brings greater economic returns for investors. It is suitable for the production of high, medium and low concentration compound fertilizers.

Advantages of Fertilizer Double Roller Extruding Granulator
- Reasonable structure: compact design, light weight, smooth running, high precision and rigidity. The pressure roller is made of new metal material, which is corrosion-resistant, oxidation-resistant and abrasion-resistant, ensuring perfect performance, reliable operation, easy maintenance and long service life of the equipment.
- Wide range of applications: 20 kinds of raw materials have been applied to extrusion pelletizing, including urea, ammonium nitrate, potassium chloride, bentonite, chicken manure, pig manure and other livestock and poultry manure waste. With extrusion pelletizing technology, the product formula can be changed flexibly and quickly, and one set of equipment can produce more than 30 product formulas.
- One-time granulation: the double-roller compaction granulator has a high granulation rate of more than 85%, and the finished granules are oval in shape.
- Environmentally friendly features: reliable motor drive, no three-waste emission, in line with environmental protection requirements.
- Low energy consumption: no need for drying process, no need for fuel or gas, which brings low-cost and high-return economic benefits for fertilizer investors.
Poultry manure fertilizer flat die granulator
Poultry Manure Fertilizer Grade Flat Die Pelletizer It is a state-of-the-art equipment specially designed to convert poultry waste into granular fertilizer. This pellet mill is particularly suitable for organic farming practices where recycling waste into usable fertilizer is essential for sustainable agriculture. Flat die pellet mills are known for their ability to process a wide range of organic materials, converting them into uniform and durable pellets.
One of the main advantages of using a flat die pellet mill to process poultry manure is its efficiency in processing high-moisture materials. Unlike other pellet mills, flat die pellet mills can process poultry manure with high moisture content without extensive drying, resulting in lower operating costs and energy consumption. This makes it an environmentally friendly option for organic fertilizer production.

Poultry Manure Fertilizer Flat Die Pelletizer is mainly used for pellet processing in the organic (bio) fertilizer and aquaculture processing industries. The granules produced by this equipment are cylindrical with smooth surface and moderate hardness. Simple structure, easy to operate, and can save a lot of energy.
How to choose the right fertilizer granulator?
Choosing the right fertilizer granulator is a key decision in the fertilizer production process and requires consideration of several factors:
Fertilizer type and raw material characteristics
- Organic and compound fertilizers: wet granulation is usually used, such as disc granulators or rotary drum granulators. These machines are suitable for handling raw materials with high moisture content.
- Inorganic fertilizers such as NPK: dry granulation, such as double-roller extruders, is used when the moisture content is low.
Production scale
- Small fertilizer plant: disc granulator is easy to operate and suitable for small-scale production.
- Large and medium-sized fertilizer plant: rotary drum granulator with large production capacity of a single machine, suitable for large-scale production.
Particle requirements
- Pellet shape: disc pelletizer and rotary drum pelletizer are suitable.
- Special shape pellets: Extruder pelletizer can produce many shapes of pellets.
Process control
- Material Moisture: Wet pelletizing usually needs to adjust the material moisture to 50%~55%.
- Pelleting temperature: Some fertilizers (e.g. bio-fertilizers) need to be pelletized at low temperatures to protect the active ingredients.
Equipment Characteristics
- Airtightness: The drum granulator is airtight, which is good for controlling dust and exhaust gas.
- Energy consumption: Dry granulation usually consumes less energy and does not require additional drying.
Operation and Maintenance
- Skill Requirement: Disc granulator requires high skill for operators.
- Degree of automation: rotary drum granulators are easy to set up automatic control.
When choosing, the above factors should be considered together with the actual production requirements and budget. Meanwhile, regular maintenance and calibration of the granulator are crucial to ensure production efficiency and product quality.

About the latest prices of TONGLI granulators
After understanding the performance and usage of various types of granulators, price is undoubtedly the most concerned issue. Different types of granulators use different production processes and materials, even if the same type of granulator, due to the difference in production capacity, the price will be different.TONGLI company promises that all fertilizer granulators use reasonable factory price.
If you want to know the latest price of TONGLI fertilizer granulator, you can contact us,we will provide you with detailed price information and considerate service of the granulator free of charge. In addition, if you have any questions about fertilizer granulator, please feel free to contact us. Our professional team will provide you with comprehensive technical support and advice to help you choose the most suitable granulation equipment for your needs.