Anatomy of a Disc Granulator
Disc granulators, also known as pan granulators, are ideal for making uniform granular products from dry or slightly moist materials. Because of its ability to produce high-quality granules, the disc pelletizer is popular in a variety of fields, from soil conditioners to chemical products.
The working principle of disc granulator is to utilize the rotating disc and added binder to make the materials roll on the disc and form spherical particles gradually. The size and quality of the granules can be controlled by adjusting the inclination and speed of the disk.
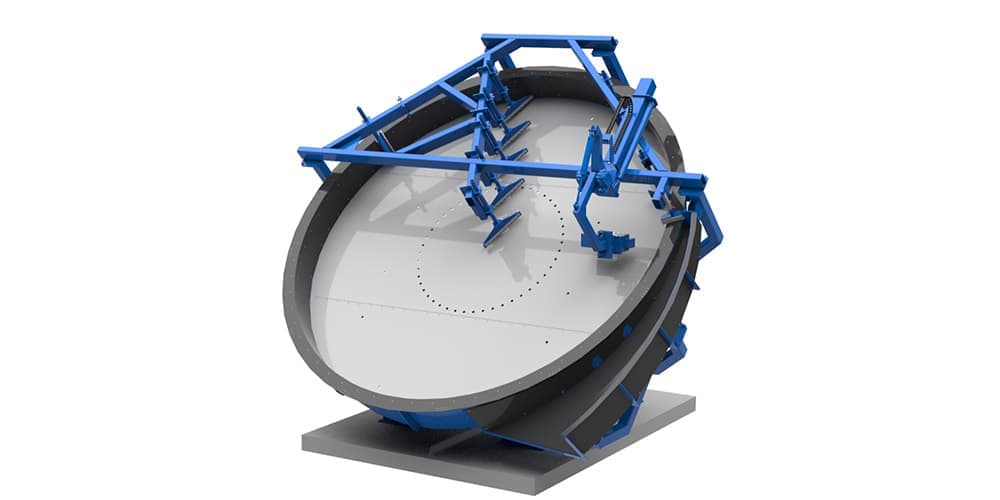
Standard Disc Pelletizer Components
A standard disc pelletizer consists of the following components.
- Base: made of structural steel and heavy welded steel plate, providing a solid foundation for the entire machine.
- Drive unit: comprising motor, reducer and V-belt drive system. The motor and reducer are mounted on a bracket behind the disk, and the disk is mounted on the output shaft of the reducer.
- Discs: Made of heavy gauge carbon steel, the discs are available in diameters ranging from 24 inches to 25 feet. The discs are welded and reinforced to strengthen the overall structure. Discs over 6 feet in diameter are lined with a metal mesh to promote the formation of a wear-resistant material.
- Plow Blade/Scraper: Individually mounted, blade-type assemblies are used to control the tumbling layer of material on the disc surface. Scrapers on larger diameter discs have a wear-resistant ceramic coating on the surface.
- Plow Blade Support: Made of heavy welded structural members that provide rigidity to the disc support system and allow for quick adjustment of the disc angle.
- Spraying System: Used to spray liquid and binder onto the discs and consists of nozzles, needle valves, pressure gauges, piping connections and spray lines.
- Infeed and Outfeed Chutes: The infeed chute (optional) directs the material onto the disk and the outfeed chute directs the finished pellets away from the disk.

Optional Disc Pelletizer Components
TONGLI can provide customized disc pelletizers to meet any product specification, including a variety of optional components and retrofit options:
- Disc material options: In addition to carbon steel, discs can be made of stainless steel for corrosion resistance.
- Hard Surface Scrapers: standard on smaller disc pelletizers, but also available for larger pelletizers.
- Hopper liners: To prevent sticking or to increase wear resistance, hoppers can be lined with ultra-high molecular weight (UHMW) thermoplastics.
- Inclination Indicator: Indicates the degree of inclination of the disk.
- Partial and Full Vent Covers: Partial and full vent covers minimize dust problems that can occur as material moves over the disc and through the discharge chute.
- Motorized Tilt Adjustment: The motorized tilt adjustment option automatically changes the tilt of the disc (replacing the manually operated jackscrew).
- Special Spray Configurations: A variety of special spray options are available to vary the delivery of liquids and adhesives. These options can be customized to the material and process application.
- Variable Frequency Drive: Variable frequency drive allows adjustment of disc speed.
- Zero Speed Switch: Indicates if the disc is rotating.
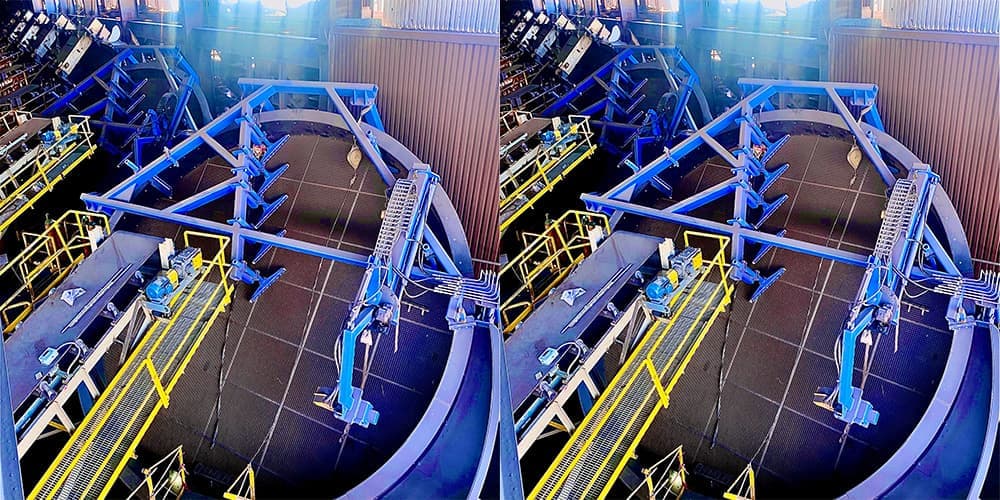
Application Scenario of Disc Granulator
Disc granulator is a versatile industrial equipment that can be used to make uniform granules from various powdery, granular or small pieces of materials. Its application scenarios cover a wide range of fields, including:
- Fertilizer industry: used to produce compound fertilizer, organic fertilizer, water-soluble fertilizer and other fertilizer products.
- Feed industry: for the production of pellet feed, concentrated feed, premix and other livestock and poultry feed.
- Food industry: for the production of food additives, food ingredients and other food processing materials.
- Pharmaceutical industry: for the production of granular drugs, pre-drug mixtures and other pharmaceutical raw materials.
- Metallurgical industry: used in the production of pelletized ore, sintered ore and other metallurgical raw materials.
- Environmental protection industry: used in the treatment of sludge, garbage and other solid wastes.
- Other industries: used in paper, ceramics, chemical and other industrial fields.
The reason why disc granulator is applied in such a wide range of fields is mainly due to its following advantages:
High granulation rate: disc granulator can make more than 90% of the materials into granules, minimizing the waste of materials.
Good quality of granules: the granules produced by the disc granulator are characterized by uniform size, high strength and good fluidity.
Simple structure and convenient operation: the structure of disc granulator is relatively simple, convenient operation and easy maintenance.
Strong adaptability: the disk granulator can be used to process a variety of materials of different properties.
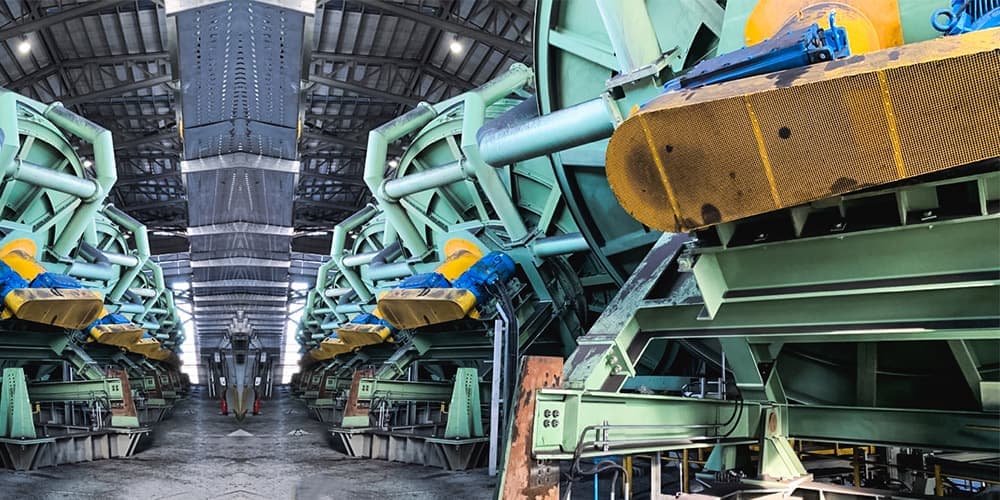
The following are some specific application examples:
Compound Fertilizer Production: In compound fertilizer production, disc granulators are usually used to make granules from well-mixed powdered fertilizer raw materials. The disc granulator can make the fertilizer particles with uniform size and strength, which is conducive to improving the fertilizer application efficiency and fertilizer effectiveness.
Feed production: In feed production, disc pelletizer is usually used to make granules from powdered feed materials. Disc pelletizer can make feed particles with good fluidity, convenient transportation and storage, and can improve the digestive absorption rate of feed.
The production output of a disc pelletizer depends on a variety of factors, including:
- Disc Diameter: In general, the larger the diameter of the disc, the higher the production output. For example, the annual production capacity of 2-meter diameter disc pelletizer can reach more than 10,000 tons, while the annual production capacity of 2.2-meter diameter disc pelletizer can reach more than 15,000 tons.
- Material nature: different nature of the material on the production output of the disk granulator also has an impact. For example, materials with good fluidity are easier to be granulated, so the production output is higher.
- Material moisture content: material moisture content is too high will affect the effect of granulation, reduce production output.
- Disc speed: the higher the disc speed, the higher the production output. However, too high rotational speed will also lead to material fragmentation, affecting the quality of particles.
- Spray volume: the size of the spray volume will also affect the production output. Too little spraying will cause the material not easy to form granules, while too much spraying will reduce the strength of granules.
According to the experience, generally speaking, the diameter of 2 meters disc granulator in normal operation, the production capacity of 5-20 tons per hour.
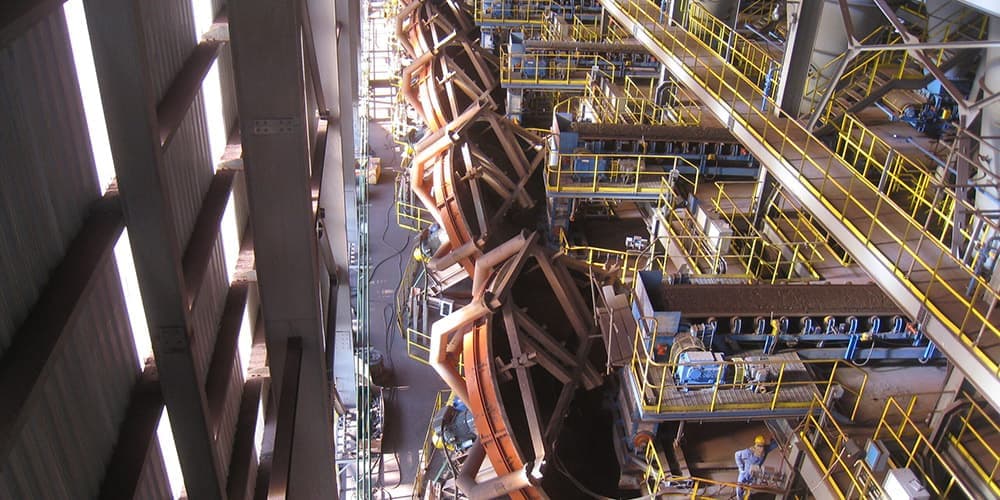
TONGILI Fertilizer Production Line Manufacturer
As a professional manufacturer of fertilizer production equipment, TONGILI provides customers with high quality granulation equipment and complete production line solutions. Our product line includes a wide range of wet and dry granulators such as disc granulators, rotary drum granulators, double roller granulators and new organic fertilizer granulators, with production capacities ranging from 0.3t/h to 50t/h.
TONGILI strictly controls the quality standards to ensure the reliability and durability of the equipment. Whether you need to build a new production line or upgrade the existing equipment, we can tailor the best solution according to your actual needs.TONGILI is committed to providing customers with efficient, environmentally friendly fertilizer production solutions, to help the sustainable development of agriculture. Welcome to contact us for the latest granulation equipment quotes and technical support.
Why choose TONGLI fertilizer production equipment?
TONGLI’s equipment has the following competitive advantages in the market:
1. High quality standard: All TONGLI products are ISO 9001 certified to ensure the high quality and reliability of the equipment. Strict quality control makes TONGLI’s equipment enjoy a good reputation in the market.
2. Rich experience: TONGLI has more than 60 years of manufacturing experience and has accumulated a wealth of technical and technological knowledge, which enables us to provide customers with professional operational guidance and technical support.
3. Wide range of product lines: TONGLI offers a wide range of pelletizing equipment, including disc pelletizer, drum pelletizer, double-roller pelletizer and new organic fertilizer pelletizer, etc., which can meet the needs of different customers. In addition, TONGLI also provides other related equipment, such as drying system, bulk material handling equipment, etc., forming a complete production line solution.
4. Customized service: TONGLI is able to provide customized equipment and solutions according to the specific needs of customers, and this flexibility enables TONGLI to meet a variety of special production requirements.
5. Global Market Coverage: TONGLI’s products are not only popular in China, but also exported to Central Asia, Southeast Asia, North and South America, etc., which has a wide market coverage.
6. Advanced Manufacturing Processes: TONGLI adopts advanced manufacturing equipment and processes, such as CNC machining equipment and automated production lines, to ensure the precision and consistency of our products.
7. Comprehensive after-sales service: TONGLI provides comprehensive spare parts and service support to ensure that customers can get timely technical support and maintenance services during the use process.