LCMC type long bag jet pulse dust collector for NPK compound fertilizer production line
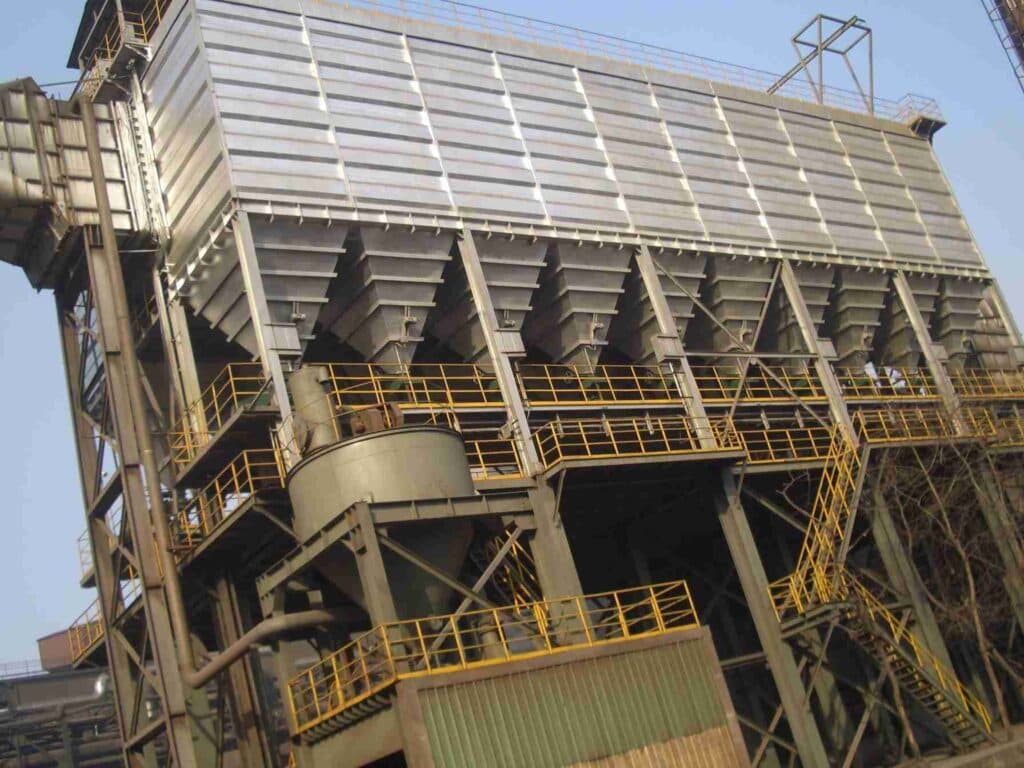
Jet pulse bag dust collector designed for fertilizer industry
- The LCMC type compound fertilizer production line low-pressure long bag pulse dust collector is a new generation of low-pressure long bag pulse dust collector developed and designed based on the design and manufacturing experience of the LCM type low-pressure long bag pulse dust collector and combined with the ultra-low emission requirements of the fertilizer industry.
- The product retains the advantages of the original long bag pulse dust collector and gives full play to the advantages of pulse injection dust cleaning. The product adopts temperature-resistant, anti-corrosion, high-precision filter media and is used in ultra-clean filtration in the fertilizer and steel industries to meet ultra-low emission requirements.
- The product has been developed to form a high-efficiency bag dust collector that meets various air volume requirements for compound fertilizer production, and can also be used in other types of large-scale dust removal projects.
Jet dust collecotor strucutre how does it work?
- The Tongli LCMC type fertilizer jet pulse dust collector adopts a divided chamber and middle air duct air inlet structure. The dust-containing flue gas enters the ash hopper of each chamber through the middle inlet and wedge-shaped air duct. In the ash hopper and before entering the filter chamber, it passes through the folding and blocking of the baffle.
- The effect of inertial gravity causes larger dust particles to fall directly into the ash hopper. Other dust particles rise with the airflow and enter the filter bags in each filter chamber.
- After being filtered by the filter bags, the dust particles are blocked outside the filter bags, and the purified gas It enters the clean air chamber box from the inside of the filter bag, then passes through the offline valve (disc poppet valve), enters the air outlet channel, and is discharged into the atmosphere through the air outlet, fan, and exhaust pipe.
- The dust in the ash hopper is transported to the ash storage silo through the ash unloading valve, cut-out scraper, collection scraper, and bucket elevator. The dust in the ash silo is discharged and transported out by a humidifier or suction device.
Jet dust collecotor self-cleaning how does it work?
- The self-cleaning working principle of jet bag house dust collector are as follows: as the filtration time continues to extend, the dust accumulated on the outside of the filter bag continues to increase, causing the resistance of the bag dust collector itself to gradually increase.
- When the resistance reaches the preset value, the PLC control system sends a signal, first instructing the poppet valve of a blowing unit to close to cut off the filtered air flow in the chamber, and then giving an instruction to open the electromagnetic pulse valve, and the compressed air flows in a very short time. 0.1~0.2 seconds, spray into the filter bag through the blow pipe and special nozzle.
- Due to the induction effect of compressed air, a large amount of clean air in the clean air box is sucked into the filter bag. The surface of the filter bag begins to expand sequentially from top to bottom, and sequentially Reaching the extreme position, reverse acceleration is generated under the action of the tension of the filter bag, so that the filter bag produces high-frequency vibration deformation, causing the dust cake adsorbed on the outside of the filter bag to deform and fall off.
- After the dust settles for a certain period of time, the poppet valve opens, the blowing unit is in the filtering state again, and the next blowing unit enters the cleaning state. In this way, dust cleaning stops ➔ filtering, so that the dust collector resistance is always at a certain value. Within the range, long-term continuous operation can be achieved.
Bag house jet dust collector data model table
Model | # of chamber | # of filter bag | Filter Area | Air to cloth ratio |
---|---|---|---|---|
LCMC192-6 | 6 | 1152 | 4500m2 | 194545~285254m3/h |
LCMC192-8 | 8 | 1536 | 6200m2 | 259390~371567m3/h |
LCMC216-10 | 10 | 1920 | 7750m2 | 325454~465730m3/h |
LCMC216-12 | 12 | 2592 | 10424m2 | 437750~625783m3/h |
What are the other types of bag house jet dust collector cleaning method?
Reverse Air (R/A) Baghouses characteristics:
- Use low-pressure air to remove solids.
- Gentle cleaning extends bag life.
- Compartmentalized design allows for selective cleaning.
- Requires filtered cleaning air.
Shaker Baghouses self cleaning characteristics:
- Mechanically shake or vibrate to dislodge particulate matter.
- Simple design but cannot operate in high temperatures.
- More energy-intensive and requires more space.
- Positive pressure reduces efficiency.
Pulse-Jet (P/J) baghouses dust collector:
- Use high-pressure air pulses to remove particulates.
- Can be cleaned while online. Offers more thorough cleaning and lower pressure drops.
- Requires dry compressed air and special fabrics for high temperatures.
summary
- R/A baghouses are gentle and compartmentalized.
- Shaker baghouses are simple but less efficient.
- Jet dust collector baghouses offer thorough cleaning but require specific conditions.
Dust cleaning control system jet dust collector:
- The jet dust collector adopts PLC to control the dust cleaning system of the dust collector. According to the different requirements of the project, it is divided into manual control and automatic control.
- The automatic control method is divided into time program and pressure difference control and time-pressure difference mixed control.
- The time control method generally sets parameters such as pulse interval and period interval. The pressure difference control selects the total pressure difference as the basis for each start.
- The pulse width is generally 0.1~0.15s, the pulse interval is generally 10~20s, and the period interval is generally 30~90min.
- The compressed air pressure for dust cleaning control needs to be determined according to the pulse valve specifications and upper injection parameters, generally 0.25~0.35MPa.
Tongli jet pulse bag house filter dust collector features:
Modular design
- Standard modular design of separate chambers and a variety of filter bag parameter combinations to meet the needs of various situations. The product is designed with 3 flower panel arrangement units. 12 specifications of single row and 15 specifications of double row are designed to meet the requirements of various flue gas volumes.
Ultra-low emission
- The LCMC type ultra-low emission jet pulse dust collector adopts a profiled plate structure in the steel structure design, which is not only beautiful but also increases the strength of the wall plate. It also eliminates thermal expansion deformation at high temperatures and prevents the welds from being pulled apart and causing damage to the dust collector. Air leakage; the dust collector adopts a divided chamber structure and modular design combination. There is a large space at the bottom of the filter bag, so that the dust-containing gas can settle before reaching the filter bag, reducing the burden on the filter bag and extending the service life of the filter bag.
Most advanced low-pressure jet cleaning technology
- The world’s most advanced low-pressure large-diameter jet cleaning technology is adopted to further improve the cleaning intensity and ensure that each filter bag maintains the highest working efficiency.
Anti-corrosion Interior coating tailored for fertilizer industry corrosive matter
- Shot blasting and high-quality coating are used inside the dust collector, which greatly extends the life of the dust collector. The life of the main equipment is >15 years.
High quality stiff jet dust collector bag cage
- The number of longitudinal bars of the filter bag skeleton is generally 12 according to the requirements of the filter material. The longitudinal bars are made of high-quality steel wire and are produced by automatic welding lines. The skeleton has high strength and no burrs to reduce friction with the filter bag. The surface is sprayed with plastic to prevent it. Use ordered long.
Ultra-small injection area jet dust collector enhance dut cleaning
- A smaller injection unit is used to reduce the injection area and minimize the impact of dust cleaning on the air volume of the system.
Ultra-small injection area jet dust collector enhance dust cleaning effect
- Electrical control can provide centralized control (DSC remote control) and machine-side control. It adopts an advanced PLC program control system and can provide two cleaning methods with fixed resistance and timing. Large projects are equipped with HMI host computer monitoring, and the operating parameters can be adjusted accordingly. display and mobilize.
Baghouses and Baghouse Filters Selection Guide LCMC series
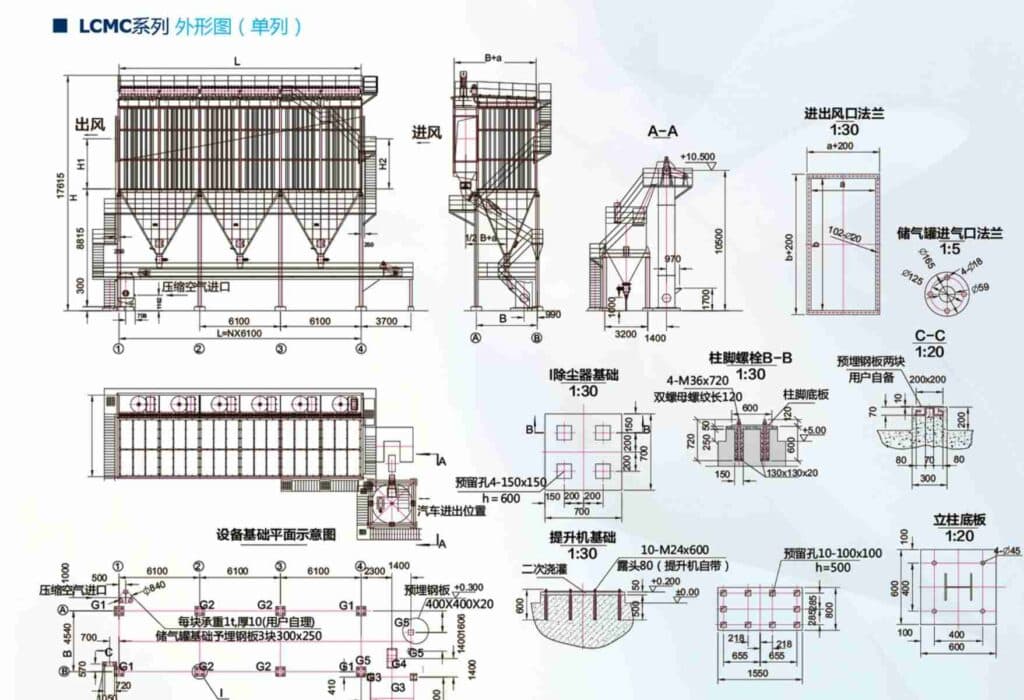
Selection of jet bag dust collector air volume aka air to cloth ratio
- The filtration air volume aka air to cloth ratio is the wind speed passing through the filter material of the filter bag (m/min).
- Some call it the air-to-cloth ratio and use unit ft/min anyways it is essential the same thing, which refers to the amount of air passing through the filter material per unit area in unit time, m2/min/m2, which is m/min.
- The selection of filtration wind speed must be based on the characteristics of dust and flue gas, temperature and humidity, dust concentration, cleaning method and selection depends on the properties of the filter material.
- The filtration wind speed not only determines the size of the dust collector, but also has a great impact on the resistance of the filter material, dust collection efficiency, dust cleaning efficiency and the service life of the filter bag.
- In order to ensure that the dust collector can be used stably and normally, the filtration wind speed must be determined after comprehensive consideration.
Selection of filter bags materials
- The filter material and filter bag are the core components of the bag dust collector. The quality of the filter bag material will directly determine the specifications, operating resistance, emission concentration, service life and other indicators of the dust collector.
- Selection principle: According to the material of the filter material, it is divided into conventional polyester, anti-static and corresponding ultra-fine needle felt filter materials or film-coated filter materials. The weight of the filter material can also be adjusted according to requirements, and the commonly used one is 550g/m2.
How to select pulse valve for your dust collector?
- The pulse valve is equipped with a 3″ submerged type, and the injection pressure is 0.25~0.35Mpa. It depends on the number of filter bags to be injected and the pulse valve.
Filter bag cage frame rib dust collector
- The number of longitudinal ribs of the filter bag frame is selected according to the filter material. The normal number is 12, and the composite filter material is 16. The surface is treated with silicone.
Off-line dust cleaning
- Cleaning control mode, offline cleaning mode, time sequence control, cleaning cycle is adjusted according to resistance changes. The operating resistance of the dust collector is generally controlled at 1000~1500Pa, and time/pressure difference sharing can also be used.
Jet filter Ash transportation and 2 types of layout:
Ground layout:
- Star unloader – ash conveyor scraper – collection scraper machine – bucket elevator – ash storage bin – dust humidifier or vacuum suction device.
Rack platform layout:
- When arranged on an elevated rack: star unloader-ash conveyor scraper-collecting scraper-ash storage bin-dust humidifier or vacuum suction device. Or unload directly into a tanker truck.
7 Remarks for this type of jet dust collector
- When ordering, please indicate the product name, model and quantity, the temperature used, the moisture content, the nature and concentration of the dust, and the type of filter material required.
- Product scope of supply, shell, air inlet, air outlet, filter bag, bag cage, porous plate, air inlet valve, ash hopper, rotary air lock feeder, pulse valve, lift valve, air source inlet A complete set of equipment including pressure reducing valve, cylinder, air distribution tank, injection system and cleaning program controller, bag dust collector control box, attached inspection platform and steel ladder.
- The scraper conveyor can be supplied as required, and the height of the bracket can be made as required by the orderer.
- Electronic control method. Our company generally uses timing electronic control. If constant voltage control is required, it will be calculated separately. If the electronic control system needs to be configured with an HMI host system and connected to the operation monitoring of systems such as fans, corresponding requirements must be provided.
- The insulation and anchor bolts of the dust collector are generally not suitable. If necessary, please ask for them and negotiate the price separately.
- A top rainproof shed needs to be installed on the top of the dust collector, and our company can also process the matching.
6. In addition to the main machine and random accessories, if the orderer needs, additional spare parts, such as pulse valves and filter bags, can be ordered. The additional quantity shall be determined by the orderer. - Various pipelines other than the dust collector body, fans, air compressors, electric control cabinets and connecting wires between the terminals on the dust collector, power lines, power supply of the electric control cabinet, lighting of the dust collector, and the foundation of the dust collector etc. are all handled by the user themselves.
Basic static and dynamic loads of jet dust collector equipment:
- Static load: G1=6.296t, G2=7.557t, G3=12.592t, G4=15.114t
- Maximum load: G1=8.321t, G2=11.607t, G3=16.642t, G4=19.164t
- Maximum load of ash silo foundation: G5=35t
- Maximum load of bucket elevator: G6=23t
- Chain conveyor platform support G7: 1T
Note: The above loads do not include wind load, snow load and earthquake load. These loads should be determined by civil engineering workers. The engineer will decide according to the specific local conditions and include the equipment load together.
Note:
- Ash chain transport machine: FU200, power 5.5kw/unit, 2 units in total
- Collection chain transport machine: FU270, power 7.5kw/unit, total 1 unit
- Bucket elevator: DT30, power 7.5kw/unit, total 1 unit
- Star unloader: HWD-26, power 2.2kw/unit,
- Ash bin vibrator: MVE200/3, AC380V, power: 0.09kw/set, 1 set in total.
What materials of filter bag suitable for Jet pulse bag dust collector?
- Polyester (PE): Offers good resistance to abrasion and chemicals, suitable for general applications.
- Polypropylene (PP): Resistant to acids and alkalis, ideal for applications involving corrosive gases.
- Aramid (Nomex): Provides excellent resistance to high temperatures, making it suitable for hot gas filtration.
- Polytetrafluoroethylene (PTFE): Known for its chemical resistance and ability to handle high temperatures, suitable for demanding applications such as pharmaceutical or chemical industries.
- Polyimide (P84): Offers superior resistance to high temperatures and oxidation, often used in applications with high gas temperatures.
- Acrylic (AC): Provides good resistance to abrasion and low temperatures, suitable for general industrial applications.
- Fiberglass: Offers high-temperature resistance and excellent dimensional stability, commonly used in high-temperature applications.
Anti-corrosion design features LCMC baghouse dust collector
- Material Selection: Choosing corrosion-resistant materials for construction, such as stainless steel, fiberglass-reinforced plastic (FRP), or coated carbon steel, depending on the severity of the corrosive environment.
- Lining and Coating: Applying protective coatings or linings to the interior surfaces of the collector to create a barrier between the corrosive gases and the equipment. Common coatings include epoxy, polyurethane, or fluoropolymer coatings.
- Chemical Resistant Components: Using chemical-resistant components for critical parts such as filter bags, cages, and inlet and outlet ductwork to withstand exposure to corrosive substances.
- Proper Ventilation: Ensuring adequate ventilation to prevent the buildup of corrosive gases within the collector, which can accelerate corrosion.
- Drainage Systems: Implementing drainage systems to remove any accumulated moisture or corrosive liquids that may collect within the collector, preventing corrosion and prolonging equipment life.
- Regular Maintenance: Conducting routine inspections and maintenance to identify and address any signs of corrosion promptly. This includes cleaning, repairing damaged coatings, and replacing corroded components as needed.
- Corrosion Monitoring: Installing corrosion monitoring systems to continuously assess the condition of the equipment and detect any corrosion-related issues early on.