Everything You Need to Know on Rotary Kiln Refractory
Rotary kiln refractory is a key component of a rotary kiln, used to protect its internal structure from high temperatures, chemical attack and mechanical wear. It is essential to ensure the efficiency of the rotary kiln process, extend its service life, reduce operating costs and maintain safety. Choosing the right refractory and maintaining it properly is therefore critical; this article will provide a comprehensive overview of rotary kiln refractories, including how they work, what types they are, and maintenance best practices.

The need for rotary kiln refractories
The rotary kiln is an important piece of industrial equipment, widely used in cement, chemical and metallurgical industries. It causes chemical reactions or physical changes in materials through high temperatures to achieve production purposes. Rotary kilns typically operate at temperatures as high as 1600°F to 3200°F, and unprotected carbon steel shells can be quickly damaged in these extreme heat environments.
For this reason, rotary kilns must use refractory materials to protect the kiln shell. Refractory materials are resistant to heat, corrosion, and abrasion, and can effectively resist high temperatures, chemical attack, and mechanical wear, thus protecting the kiln shell from damage and extending the service life of the rotary kiln.

Refractory materials are mainly used in direct-fired rotary kilns. In direct-fired rotary kilns, combustion occurs inside the kiln and the flame directly contacts the kiln shell, resulting in higher temperatures inside the kiln and higher requirements for refractory materials. In indirect-fired rotary kilns, the combustion chamber is located outside the kiln, and the heat is transferred to the materials inside the kiln by radiation, so the requirements for refractory materials are relatively low, and some kilns do not even use refractory materials.
Refractories not only protect the kiln shell and extend the life of the equipment, but also minimize heat loss and improve the overall process efficiency. Qualified refractory materials can effectively block heat transfer to the outside, making the temperature inside the kiln more uniform, thus improving the firing quality of materials and reducing fuel consumption.
Main types of refractories
Castable refractories
Castable refractory is a refractory material in powder form that needs to be mixed with water on site before it can be used. Prior to pouring the mixture, anchor bolts need to be installed to strengthen the lining. These anchor bolts are similar to rebar in cement. After the mixture is poured, it is left to cure for several days.
Advantages:
- Lower total cost: Castable refractories have similar material costs to refractory bricks, but are more economically efficient overall due to easier installation and lower labor costs.
- Ease of Repair: When problems occur with castable refractories, it is usually just a matter of removing the damaged portion and re-pouring new material, making the repair process relatively quick and easy, with little downtime.
Disadvantages:
- Problematic installation: If not installed properly, the quality of castable refractories may be affected, even leading to a shortened service life.
- Poor abrasion resistance: compared with refractory bricks, castable refractories have poor abrasion resistance and are not resistant to wear when dealing with highly abrasive materials.

Refractory bricks
Refractory bricks are fired at high temperatures under tightly controlled conditions, resulting in excellent properties and wear resistance.
Advantages:
- Better quality: refractory bricks are denser and stronger, providing a longer service life at high temperatures and in corrosive environments.
- Better abrasion resistance: refractory bricks excel in handling highly abrasive materials, making them ideal for such application scenarios.
Disadvantages:
- Higher cost: refractory bricks have a slightly higher material cost than castable refractories and require more labor for the installation process, resulting in a higher overall cost.
- Difficult to Repair: When refractory bricks are damaged, it is often necessary to replace the entire damaged area, not just individual bricks, making the repair process cumbersome and time-consuming.

Choice Advice:
- Castable refractories are an affordable option when budgets are limited, but care needs to be taken to select reputable suppliers and builders to ensure a quality installation.
- For application scenarios where highly abrasive materials need to be handled or a longer service life is required, refractory bricks are a superior choice.
- When selecting refractory materials, specific application conditions should be considered, including kiln temperature, operating cycles, material abrasiveness and other factors.
- It is recommended to consult a professional refractory engineer for the most suitable solution for you.
Customization of refractories for rotary kilns
To meet the specific needs of different applications, rotary kilns are often constructed using multi-layer refractory construction. This approach involves using a combination of working and insulation layers to optimize performance and energy efficiency.
The working layer: a barrier against harsh conditions
The working layer is the front line of defense against the extreme temperatures and abrasive forces inside a rotary kiln. The layer is usually made of high-density, durable materials, such as high-alumina bricks or castables. Its main function is to withstand direct contact with the process material and the intense heat generated during operation.
Insulation: protecting the rotary kiln structure
The insulation layer plays a vital role in protecting the rotary kiln shell from high-temperature damage. This layer is usually made of less dense and lighter materials, such as insulating bricks or mineral wool. Its main purpose is to minimize heat transfer from the working layer to the kiln shell, preventing potential damage and improving overall thermal efficiency.

Balancing the working and insulation layers
The thickness of each layer is carefully determined according to the specific application and operating conditions. In general, thicker refractory layers should be used for processes involving highly abrasive materials or extreme temperatures, while thicker insulation layers should be used for applications where energy efficiency is a priority.
Optional ceramic fiber liner for extreme insulation
Where extreme insulation is critical, an optional third layer of ceramic fiber liner can be used. This thin but effective layer provides an additional thermal barrier and is particularly suitable for extreme high temperature applications. However, its use needs to be carefully considered and monitored, as any cracks or damage to the refractory system can expose the ceramic fiber liner to direct heat, leading to potential safety hazards.
Preventive maintenance of rotary kiln refractories
The harsh operating conditions of high temperatures, high loads, abrasion and corrosion in rotary kilns pose a serious threat to the kiln refractory, and can even lead to catastrophic consequences. Therefore, it is vital that refractories are properly maintained after installation and use.
While high-quality refractories can last for many years when properly installed, certain factors can shorten their life. While early signs of refractory failure are difficult to detect, fortunately, many of the causes of refractory failure are preventable. Among them, cyclic stress and chemical incompatibility are the leading causes of refractory failure.
Cyclic stress refers to the repeated heating and cooling processes of a rotary kiln. Each time the kiln heats up, the refractory expands with the kiln and contracts when it cools. Frequent starts and stops can put tremendous stress on the refractory, leading to cracks. Similarly, too rapid heating up or cooling down can also cause cracks. Therefore, minimizing the number of starts and stops and keeping the kiln running continuously can extend refractory life.
Chemical incompatibility is another common problem. Refractories are not resistant to certain chemicals, such as chlorides. Chlorides are highly corrosive and accelerate refractory wear. Identifying these chemicals in advance and designing the refractory according to their properties can reduce the risk of excessive wear. In addition, unknown components in the material or changes in the raw material can lead to excessive refractory wear.
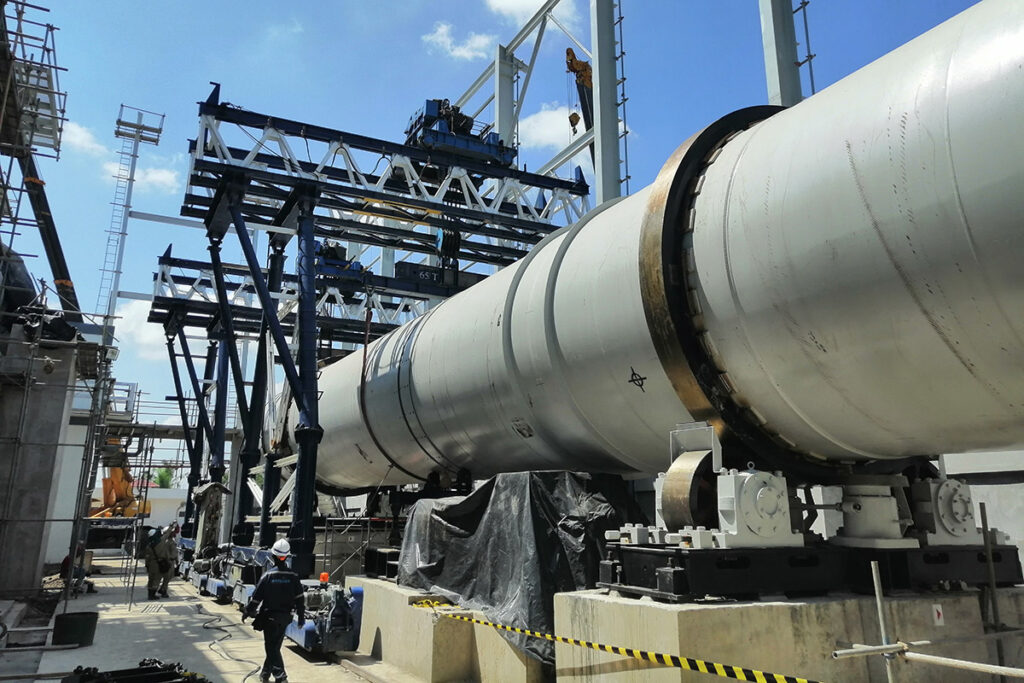
In order to extend the life of the refractory and minimize unexpected failures, the following preventive maintenance measures should be taken:
- Monitor Temperatures Regularly: Regularly checking the temperature of the rotary kiln shell using a temperature gun can help identify hot spots in the refractory in a timely manner. Uneven temperatures may indicate that the refractory has begun to fail and needs to be repaired.
- Visual and Audible Inspections: Operators should familiarize themselves with the normal operation of the rotary kiln and perform regular visual and audible inspections to detect any abnormalities. These inspections can help detect cracks or other damage to the refractory material at an early stage.
- Specialized technician inspections: Specialized technicians should be invited to carry out detailed inspections and evaluations at regular intervals, usually once a year, although more frequent inspections may be required for demanding environments. These inspections can provide specialized maintenance recommendations to help extend the life of the refractory.
- Preventive Maintenance: Based on the results of regular inspections, a preventive maintenance program is developed to repair or replace damaged refractory materials in a timely manner to prevent minor problems from becoming major ones.
- Operator Training: Provide regular training to operators to improve their knowledge and maintenance skills of refractory materials to ensure that they can operate and maintain the rotary kiln correctly and minimize refractory damage caused by human factors.
- Record and analyze: Record the results of each inspection and maintenance, and analyze them to find out the pattern and causes of refractory damage, and continuously improve the maintenance measures to increase the maintenance efficiency.
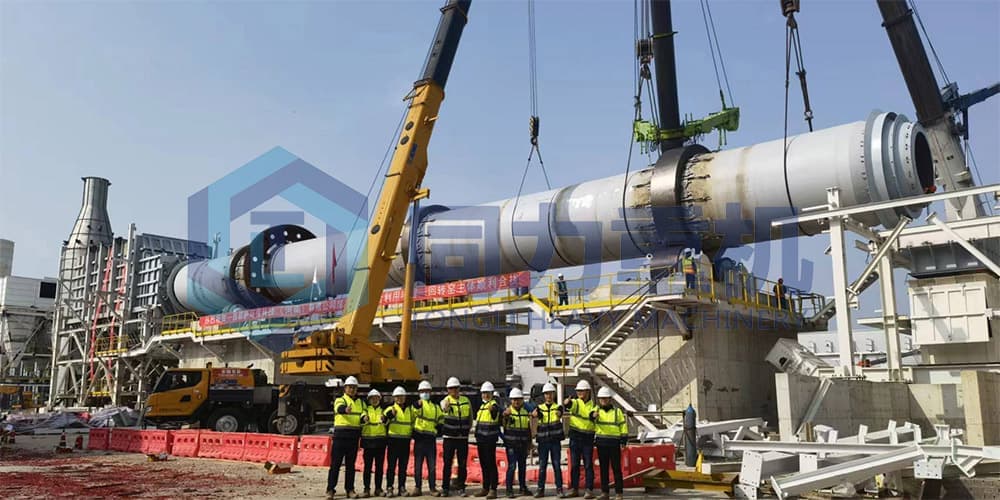
Conclusion
Refractories are an important part of a direct-fired rotary kiln, and are vital for protecting the equipment and improving efficiency. Choosing the right refractory material configuration and doing routine maintenance can significantly extend the service life of rotary kiln and improve the production efficiency.
TONGLI is a professional rotary kiln manufacturer with over 60 years of industry experience. Our professional team will provide you with comprehensive technical consultation and customized solutions to meet your needs in the fields of cement and building materials, mining, environmental protection, metallurgy and chemical industry. Contact us today to explore the unlimited possibilities that rotary kilns can bring to your production!