Complete equipment configuration of organic fertilizer production line
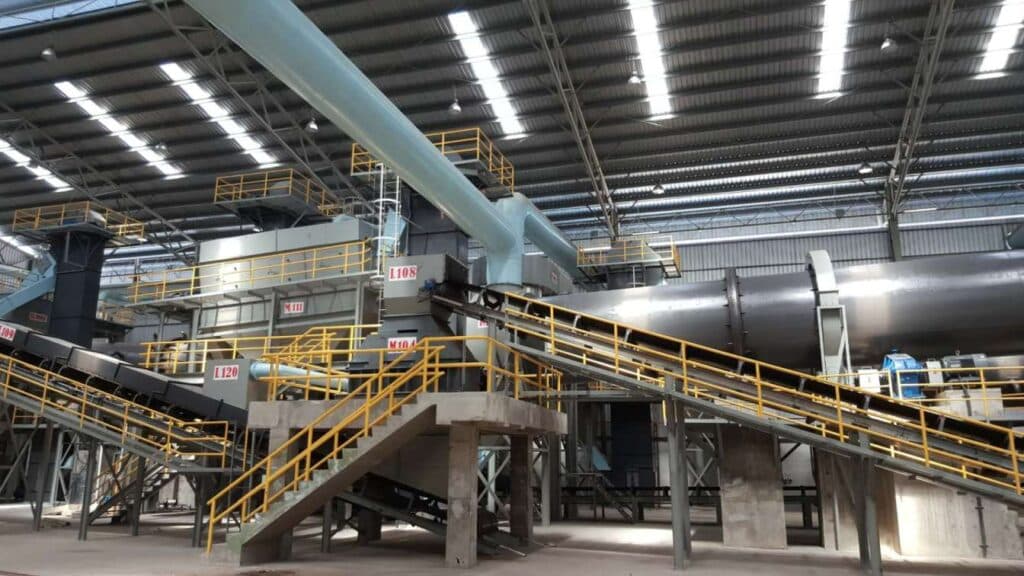
Introduction:
- The construction scale of chicken manure organic fertilizer production line equipment configuration is generally 30,000-200,000 tons per year. Generally, local resources, market capacity, and market coverage should be comprehensively considered. 1. The investment scale and product plan design need to be formulated based on the following conditions: raw material resource characteristics, local soil conditions, local planting structure and main crop varieties, factory site conditions, degree of production automation, etc.
- The process flow of the chicken manure organic fertilizer production line – the organic fertilizer project has a short construction period, high profit return on investment, low market risk (organic fertilizer generally has a shelf life of at least 5 years), a short payback period (when the farming season is busy, supply exceeds demand), and the market potential is large.
Chicken manure organic fertilizer production line process flow diagram
- Raw material selection (chicken manure, etc.) → drying and sterilization → ingredient mixing → granulation → cooling and screening → metering and sealing → finished product storage.
- The more complicated production process of chicken manure organic fertilizer is as follows: after fermentation, the organic fertilizer raw materials (animal manure, domestic garbage, dead branches and leaves, biogas residue, waste bacteria, etc.) enter the semi-wet material crusher for crushing, and then added Nitrogen, phosphorus, potassium and other elements (pure nitrogen, phosphorus pentoxide, potassium chloride, ammonium chloride, etc.) are used to make the mineral elements contained reach the required standards, and then stirred by a mixer, and then enter the granulation mechanism to make the particles, and then dried, screened by the screening machine, qualified products are packaged, and unqualified products are returned to the granulator for granulation.
Chicken manure organic fertilizer production line equipment list
- The organic fertilizer production process flow is closely related to the equipment configuration of the organic fertilizer production line. Generally, the complete set of equipment of the organic fertilizer production line mainly includes:
- Fermentation system
- Drying system
- Deodorization and dust removal system
- Crushing system
- Batching system
- Mixing system
- It consists of ten systems: granulation system
- cooling and drying system
- screening system
- finished product packaging system.
The equipment requirements for each link of the organic fertilizer production process are described in detail below:
Organic fertilizer fermentation system:
Characteristic of Organic fertilizer fermentation compost turner
- It consists of a feeding conveyor, a biological deodorizer, a mixing mixer, a proprietary lifting and throwing machine, and an electrical automatic control system.
- The organic fertilizer fermentation compost turner is suitable for continuous fermentation in organic fertilizer plants. Features of this model include: compact structure, advanced technology, short fermentation cycle (7-10 days), low energy consumption, and stable product quality.
- The thickness of the fermentation materials in the tank is 70-90cm. Continuous aerobic fermentation relies on natural ventilation and the oxygen provided by the contact between the materials and the air during turning. The fermentation and turning process realizes fully automatic and intelligent control.
Working principle of organic fertilizer fermentation compost turner
- The working principle of the organic fertilizer fermentation compost turner: under the transportation of the vertical and horizontal traveling mechanisms, the high-speed running rake throws up, scatters and produces a certain displacement of the fermentation materials, so that the materials can be gradually and regularly moved at an equal distance in the pool.
- The fermented materials are moved away from the end of the fermentation tank every day, and the space vacated at the front of the fermentation tank (one day’s processing capacity) is replenished with new fermentation materials, thus forming a continuous fermentation process.
Organic fertilizer Drying system:
- The main equipment includes belt conveyors, drum dryers, coolers, induced draft fans, hot blast furnaces, etc.;
Deodorization and dust removal system:
- Composed of settling chamber, dust removal chamber, etc.
Crushing system:
- New semi-wet material crusher, LP chain crusher or cage crusher, belt conveyor, etc.;
Semi-wet material crusher technical specification:
- Semi-wet material crusher: It is a new type of high-efficiency single-rotor reversible crusher with strong adaptability to the moisture content of the material, especially for grinding decomposed garbage after fermentation or other materials with a moisture content of ≤30%.
- The particle size of the powder can reach 20~30 mesh, which can meet the feeding particle size requirements of general fertilizer granulation equipment.
- The surface of the produced particles is smooth, making it an ideal equipment for the production of organic fertilizers.
Batching system:
- Includes equipment such as electronic batching system, disc feeder, vibrating screen, which can configure 6-8 kinds of raw materials at a time;
Mixing system:
Horizontal mixer:
- Horizontal mixer: high mixing uniformity and low residue, suitable for mixing compound feed, concentrated feed, and additive premix. The specific characteristics are: the materials are fully mixed.
- Thereby improving the mixing uniformity; using a novel rotor structure, the minimum gap between the rotor and the shell can be adjusted to close to zero, effectively reducing the amount of material residue; the machine is equipped with a grease adding pipeline, the overall structure is more reasonable, and the appearance is beautiful. Easy to operate and maintain.
Granulation system:
- Granulator equipment is required. The optional granulator equipment is: compound fertilizer double-roller extrusion granulator, disc granulator, flat film granulator, bio-organic fertilizer spherical granulator Machine, special granulator for organic fertilizer, drum granulator, rounding machine, special granulator for compound fertilizer, etc.;
Special granulator for organic fertilizer:
- Chicken manure organic fertilizer granulator. This wet granulator is also called an internal rotating tooth granulator and is widely used for granulating organic fertilizer.
- Typical application materials: chicken manure, cow manure, charcoal, clay, kaolin, etc. It is specially used for granulating organic fermentation fertilizers from urban domestic waste such as livestock and poultry manure, compost fertilizer, green manure, sea fertilizer, cake fertilizer, peat, soil fertilizer, three wastes, microorganisms and other organic fertilizer raw materials. properties, the particles are irregular spherical particles.
- The qualified granulation rate of this machine is as high as 80-90%, which is suitable for a variety of different formulas. The compressive strength of organic fertilizer is higher than that of discs and drums, and the large ball rate is less than 15%. The uniformity of particle size can be passed according to user requirements.
- The machine has stepless speed adjustment function. This machine is most suitable for direct granulation of organic fertilizer after fermentation, saving the drying process and greatly reducing manufacturing costs.
Cooling and drying system:
Rotary dryers, drum coolers and other equipment can be used for drying and cooling.
Rotary dryer organic fertilizer production line
- Rotary dryer: Rotary dryer is mainly used for the production of compound fertilizer, drying fertilizer with a certain humidity and particle size, and can also be used for drying other materials.
- The main body of the rotary drum dryer is a slightly inclined cylinder that can rotate. The rotary drum dryer is mainly composed of a rotary body, a lifting plate, a transmission device, a support device, a sealing ring and other components.
- It has the advantages of reasonable structure, excellent production, high output, low energy consumption, convenient operation, reliable performance, high heat energy utilization, uniform drying, less cleaning of materials, and easy use and maintenance.
Screening system:
- It is mainly completed by a drum screening machine. It can be equipped with a first-level screening machine and a second-level screening machine to achieve a higher yield and better particles;
Finished product packaging system:
- Finished product packaging system: generally includes electronic quantitative packaging scales, silos, automatic bag sewing machines, etc. In this way, fully automatic and intermittent production of the organic fertilizer production line can be realized.
Finished product packaging system working principle:
- Principle of quantitative packaging scale: When the quantitative packaging scale enters the automatic operation state, the weighing control system opens the feeding door and starts feeding.
- The feeding device is a fast and slow two-stage feeding mode; when the material weight reaches the fast feeding set value when the material weight reaches the final set value, close the feeding door and complete the dynamic weighing process; at this time, the system detects whether the bag clamping device is in a predetermined state.
- When the packaging bag has been clamped After tightening, the system sends a control signal to open the discharging door of the weighing hopper, and the material enters the packaging bag.
- After the material is discharged, the discharging door of the weighing hopper automatically closes; after the material is discharged, the bag clamping device is released, and the packaging bag automatically falls;
- After the packaging bag falls, it will be sewn and transported to the next station. This cycle runs automatically.
Introduce powdered poultry organic fertilizer production double roller extrusion technology:
- For example, the raw material is chicken manure + straw powder. First, mix the chicken manure with an appropriate amount of straw powder. The amount of mixing depends on the moisture content of the chicken manure. Generally, fermentation requires a moisture content of 45%, that is, it can be kneaded into a ball with your hands and can be seen between your fingers. Water, but not dripping, it will disperse as soon as you let go.
- Then add cornmeal and bacteria. The function of cornmeal is to increase the sugar content for bacterial fermentation, so that the biological bacteria decomposition agent will quickly take over. Then add the prepared mixture into the mixer and mix. The mixing must be even and thorough without leaving any lumps.
- The mixed ingredients are piled into a long strip with a width of 1.5 meters to 2 meters and a height of 0.8 meters to 1 meter, and are turned with a turning machine every 2 days. It takes 2 days to heat up, 4 days to become odorless, 7 days to become loose, 9 days to become fragrant, and 10 days to become fertilized. Specifically, on the second day of stacking, the temperature can reach 60℃-80℃, killing pests and diseases such as E. coli and insect eggs;
- On the 4th day, the odor of chicken manure was eliminated; on the 7th day, the compost became loose and dry, covered with white mycelium; on the 9th day, it gave off a aroma of distiller’s yeast; on the 10th day, the bacterial manure was fermented and matured, and can be used after a little drying The semi-wet material is crushed by a crusher and then screened by a screening machine. The powdered organic fertilizer is ready and can be packaged and stored.