8 Types of npk compound fertilizer production granulation method.

What is the drum granulation NPK fertilizer production method?
The Drum granulation NPK fertilizer production method is materials are agglomerated and granulated with the help of the rolling drum while using water or steam, or water and steam to provide the liquid phase necessary for granulation. Chemical reactions may or may not occur during the granulation process, depending on the materials being granulated. When this granulation method was first implemented, a disc granulator was used and operated intermittently. Today, it is rarely used except by a few small batch producers. The most widely used one at present is the drum granulation process.
What is srpay slurry NPK fertilizer production Method?
The spray granulation fertilizer production method is to spray the material into the granulator in the form of slurry and coat it on the surface of the returned particles, and then send it to dry; then it enters the granulator as the return material and is coated with the slurry again, and then sent to Drying; this is repeated until the particles are continuously coated with the slurry and gradually increase layer by layer like onion skins until they meet the required size range. Therefore, it mainly relies on accumulation and granulation. In actual production, due to the wide particle size distribution range of the returned material and the rotation of the granulator, some fine particles will also agglomerate into granules.
What is dry compaction(roller extrusion) NPK fertilizer production Method?
The extrusion granulation method uses pressure to agglomerate dry materials into granules. In actual production, various raw materials are first metered and fed into the mixer to mix evenly, and then the screw feeder feeds the mixture into the extruder at a given speed. (If it is a single raw material, there is no need to mix it and it will be fed directly into the extruder through the screw feeder.) The extruder consists of two pressure rollers installed in parallel and rotating in opposite directions. Usually one pressure roller has a fixed bearing, and the other can move relatively through the hydraulic system as needed to adjust the distance between the two pressure rollers.
What are the 6 steps of dry compaction roller extrusion NPK fertilizer production method?
- The material is forced to pass between the two pressure rollers and is squeezed into thin sheets. The flakes are broken into small pieces by a coarse crusher (which can also be set up separately) installed in the extruder and then screened. Particles that are larger than the required particle size will be crushed and screened again, and particles that are smaller than the required particle size will be returned to be re-extruded. Those that meet the required particle size can be packaged as finished products before leaving the factory.
- The purpose of conditioning is to bind dust and prevent the finished product from clumping. When using certain materials that are not easy to process and produce by extrusion granulation, or when there are special requirements for granular fertilizer products, it is necessary to add a refining process after backlog, crushing and screening.The refining process generally consists of three units: grinding, particle polishing and solidification, and wrapping.
- The grinding unit is designed to remove irregular edges and corners from the crushed particles, while removing those particles whose strength does not meet the requirements as well as the fine powder produced during the grinding process and sending them back for re-extrusion.
- The particle polishing and solidification unit impregnates the ground particles with a small amount of water, steam or slurry before granulating, drying and screening. For granular fertilizers made of certain materials, a cooling system should be installed after screening.
- The wrapping unit coats the surface of the granular fertilizer processed by the above two units with a layer of liquid or solid wrapping agent to prevent the product from caking. If necessary, the granular fertilizer can also be surface treated here to produce slow-release fertilizer.
- Finally, sieving is performed to remove any clumps that may have occurred during the wrapping process.Due to the increase in refining processes, investment, energy consumption and production costs are bound to increase. Therefore, unless necessary, no additional refining process is generally required.
What are the factors that affect the extrusion granulation effect and products?
- The factors that affect the extrusion granulation effect and products are the raw materials used and the extrusion operating conditions. The raw materials include material characteristics, moisture content, particle size distribution, plasticity, temperature and hardness. On the premise that the moisture content does not exceed 2%, the characteristics of the material have the greatest impact.
- Materials that have been used for extrusion granulation in industrial production and experimental equipment include: potassium chloride, ammonium sulfate, ammonium bicarbonate, urea, ammonium chloride, calcium nitrate, phosphate rock powder, ordinary superphosphate, and heavy superphosphate. , monoammonium phosphate, diammonium phosphate, steel slag phosphate fertilizer, gypsum dihydrate, potassium sulfate, nitrogen-phosphorus compound fertilizer, nitrogen-phosphorus-potassium compound fertilizer, nitrogen-phosphorus-potassium-phosphate compound fertilizer, nitrogen-phosphorus-potassium-boron compound fertilizer, nitrogen-phosphorus-potassium-sulfur-boron compound fertilizer Fertilizer, peat mixture, organic fertilizer, etc.
- Practice shows that the extrusion properties of potassium chloride, ammonium sulfate, ammonium bicarbonate and urea are very good, while the extrusion properties of ordinary calcium phosphate, lime nitrogen and phosphate rock powder are slightly worse.
Effect of pressure on compound fertilizer extrusion granulation effect
- Another factor that affects the extrusion granulation effect and products is the extrusion operating conditions. It includes the operating pressure, the diameter of the pressure roller and its circumferential linear speed, the surface structure of the pressure roller, the operating gap between the pressure rollers, etc.
- In order to obtain a product with a certain strength and density, sufficient pressure must be applied during the extrusion process. Operating pressure is usually expressed in N/cm, which is the total force applied divided by the width of the roll – the required pressure is also a function of the roll diameter. The operating pressure is related to the granular fertilizer product (essentially the comprehensive characteristics of the raw materials used).
- The production capacity of the extruder and the thickness of the extruded flakes depend on the diameter of the pressure roller. Under a specific pressure, each material has an optimal sheet thickness, which is generally in the range of 0.01% to 0.3% of the diameter of the pressure roller. In order to facilitate the discharge of air extruded from the material and maintain the continuous and smooth operation of the extruder, the circumferential linear speed of the pressure roller usually does not exceed 1.2m/s.
- During the extrusion process, a certain degree of sliding will occur between the material and the surface of the pressure roller due to the characteristics of the material, the surface structure and conditions of the pressure roller. A pressure roller with a smooth surface is not easy to introduce the material into the gap between the two pressure rollers, and is not conducive to discharging the air squeezed out of the material. Therefore, pressure rollers with circular floating grooves, or granular or sinusoidal rollers are often used. Pressure roller.
- The gap between the two pressure rollers of the extruder can be adjusted according to the material conditions and product requirements. If the gap is increased and the thickness of the sheet is increased, the production capacity of the extruder will be increased. But under a certain pressure, the closer the material is to the center, the better. Therefore, if the gap is too large, the extruded sheet will be too thick. This weakening of the flakes will ultimately affect the hardness of the finished granular fertilizer. For this reason, the operating gap between the pressure rollers must not be arbitrarily increased, thereby limiting the method of increasing the thickness of the sheet to increase the production capacity of the extruder.
- In addition, different materials in the formula may undergo chemical reactions after extrusion and granulation. This can lead to particle breakage in some cases.
- Based on the above reasons, after the grades and specifications of raw materials (or mixtures) and products are determined, it is necessary to conduct an extrusion granulation evaluation test. The main contents include the extrudability of the material, the temperature rise of the material during the extrusion process High impact on processing, the most suitable roller surface structure, rotation speed, extrusion pressure, requirements and effects on flake crushing and screening, quality analysis and inspection of granular fertilizer and whether refining processes are required, etc.
What are the advantages of extrusion granulation fertilizer production method?
- Drying and cooling processes are generally not required during the production process, and it is especially suitable for processing heat-sensitive materials while saving investment and energy consumption.
- All operations are carried out under dry conditions, and no wastewater is discharged to pollute the environment. Since the possibility of corrosion is small, general conditions can be used for equipment manufacturing, and the cost is low.
- It can produce fertilizers with a higher concentration than ordinary compound fertilizers, and organic fertilizers can be added to the raw materials as needed.
- According to a study conducted by the International Fertilizer Development Center for developing countries in 1987: For a granular NPK fertilizer device with an annual output of 120,000 tons, the investment of the extrusion granulation method is 20% lower than that of the steam granulation method, and only It is 50% of the traditional chemical method or slurry granulation method.
- Extrusion granulation is simple to operate, and can realize production automation control. If necessary, the grade of the product can be quickly changed, making production convenient and flexible.
- The extrusion granulation device does not have a certain operating scale. The production of small devices is equally economical and feasible. Special fertilizers can also be produced in small batches according to user requirements. Production and operation are relatively flexible.
Since the extrusion granulation method has the above advantages, in addition to being widely used in the potassium fertilizer industry, it has also been gradually extended to the granulation of ammonium sulfate, urea, ammonium bicarbonate, nitrogen-phosphorus and nitrogen-phosphorus-potassium compound fertilizers.
What is the melt condensation granulation fertilizer production method?
Melt condensation granulation fertilizer production process is to spray the almost waterless hot flowing melt directly into cold coal (cold coal is usually air or a liquid that does not dissolve the melt material, such as mineral oil, etc.). Condensation and solidification into granulation, or the reaction mixture is basically sprayed in the form of anhydrous liquid or melt on the surface of the particles as “crystals” in the granulator, so that the particles grow to meet the required size in the layer-by-layer wrapping. The granular fertilizers are all made by melt condensation and granulation. Although the evaporation or concentration of the solution consumes energy, it is far more efficient than dry granular products in terms of energy utilization; in some productions, the heat of reaction can also be fully utilized to evaporate part or even all of the water.
What is the spray granulation tower prilling method?
- The spray granulation tower process is a form that uses melt condensation granulation method. It was first used for the granulation of single nitrogen fertilizer, and is still widely used for the granulation of urea, and has gradually been extended to the granulation of nitrogen, phosphorus and nitrogen, phosphorus and potassium compound fertilizers.
- There are two types of tower bodies: round and square, with the majority being round. The interior of the tower adopts natural ventilation or forced ventilation depending on the specific conditions. The effective height of the tower is determined by the time required for the melt droplets to cool and condense, so it is related to the material characteristics, particle size and ventilation method.
What is the NPK fertilizer oil immersion granulation Production Method?
- The oil immersion granulation process was first developed by the Dutch Stamicarbon Company for calcium nitrate granulation. The oil immersion granulation process is the same as the spray granulation tower process. The melt is sprayed out and falls into the mineral oil. The droplets solidify into granules after cooling
- The difference between these two processes is that the spray granulation tower process uses air as the cooling medium for droplets, while the oil immersion granulation uses oil as the cooling medium for droplets. Subsequently, the U.S. National Fertilizer Development Center conducted pilot trials of oil-immersed granulation of urea-ammonium polyphosphate mixtures.
- The test uses electrothermal phosphoric acid as the raw material. An ammonium polyphosphate solution containing about 50% P2O5 is first prepared and then mixed with the urea melt. The mixture is sprayed into droplets through a rotating basket or nozzle. The temperature of the droplets is approximately 132°C. The droplets fall from the air into an oil tank containing light oil. The oil temperature is maintained at about 38°C with the help of a water cooling coil. The droplets are cooled and solidified in the oil into particles, and then a centrifuge is used to separate the particles from the oil. The oil is returned to the sump for reuse. The product particle size is 2.8~1.4mm (7~12 mesh). Product grades include 30-30-0, 36-18-0 and 39-13-0.
- Japan’s Mitsui Toya Chemical Company once mixed urea melt with dry and preheated monoammonium phosphate, ammonium chloride, ammonium sulfate, etc. and sprayed it. The droplets are collected in low viscosity oil and solidified into granules. The particles are separated from the oil by a centrifuge. According to reports, the mixing time should not exceed 4 minutes, and the temperature of the mixture must be controlled. The optimal temperature is 125°C when producing 18.6-18.6-18.6. Other grades mentioned are 28-28-0 and 18-21-17.
What is the NPK compound fertilizer tubular reactor granulation process?
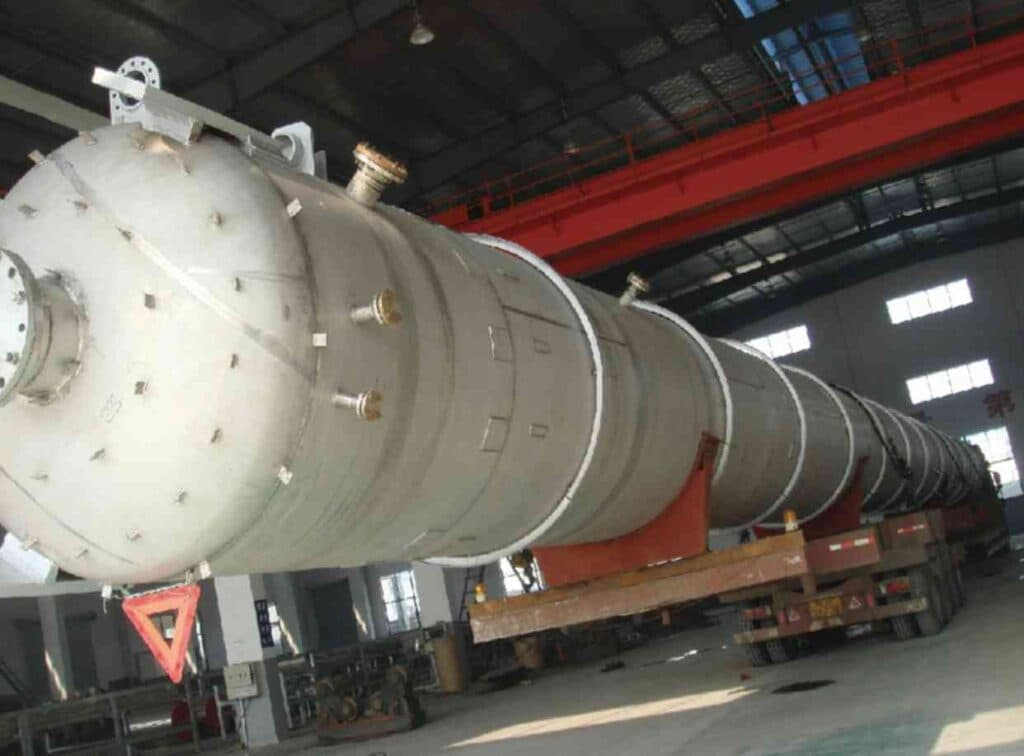
- The tubular reactor granulation method uses phosphoric acid, sulfuric acid and ammonia to react in a tubular reactor with a small solvent. The large amount of chemical reaction heat vaporizes most of the moisture in the feed and makes the temperature of the melt higher than the melting point of the material. The reaction pressure reaches 0.17~0.24MPa, so the melt can be evenly distributed on the material bed of the granulation equipment to make granular fertilizer after leaving the reactor.
- The patent of German IG Farben in 1927 proposed a production method similar to the principle of tubular reactor. From the mid-1940s to the mid-1960s, there were patents describing the reaction of single phosphoric acid, nitric acid, sulfuric acid, or mixed acid with liquid ammonia, gas ammonia or ammonia solution in a tubular reactor to produce powdered monoammonium phosphate or polyphosphoric acid. Ammonium, ammonium nitrate, and liquid fertilizers based on ammonium phosphate, etc.
- Since the mid-1960s, TVA in the United States and Cros Company in Spain have successively reported some technological development results related to tubular reactors, and have gradually applied these results to the industrial production of chemical fertilizers. As in the spray granulation tower process introduced earlier, Norsk Hydro’s urea-ammonium phosphate and urea-ammonium potassium phosphate (UAP/UAPK) pilot processes are used to produce MAP and use MAP melt and solid urea/KCl to produce UAP// UAPK, are all examples of application of tubular reactors.
- Through production practice, the tubular reactor granulation process has shown many advantages, mainly including: simple structure, convenient operation, easy production control and maintenance; using it to replace the pre-neutralizer can save the pumps and pipelines for transporting slurry , valves and slurry metering devices, thus the investment cost can be reduced by about 30% compared to the pre-neutralization-drum ammoniation granulation system of the same production scale.
What is the fluidized granulation process of NPK compound fertilizer?
- The fluidized granulation method is to introduce a strong air flow from the porous plate of the fluidized bed to fluidize the return material and fine-grained materials used as “crystal seeds” in the fluidized bed. At the same time, the melt, slurry, or solution that needs to be granulated is atomized with compressed air into particles and coated on the surface of the “seed crystal” to form a thin film.
- Since the fluidized material is tumbling and moving in the fluidized bed, the gas and solid are in good contact, which is conducive to mass transfer and heat transfer. Therefore, if the feed is molten material, the molten material film coated on the surface of the “seed crystal” will solidify quickly;
- If the feed is slurry or solution, a thin film of slurry or solution coated on the surface of the “seed crystal” will dry due to rapid evaporation of water. The “seed crystal” in which the film has been solidified or dried is then coated with atomized melt, slurry, or solution particles, and then solidified or dried.
- By repeating this process continuously, the “seed crystals” gradually grow, and when the particles reach the required size, they are removed from the fluidized bed. The subsequent processes, such as cooling, screening, crushing, wrapping (if necessary) and exhaust gas evolution, are the same as the usual granulation process.
- The air flow that fluidizes the materials in the fluidized bed also plays a role in cooling and drying the particles. If the inlet temperature of the air and the amount of returned material can be controlled and the heat balance inside the fluidized bed can be maintained, the fluidized bed can be operated stably. Therefore, the fluidized granulation process is relatively easy to operate, has high production intensity, compact equipment, and low investment costs.
- The particle size of the granular fertilizer produced by the fluidized granulation process can be adjusted within a wide range and can adapt to different needs of agricultural production. The granular fertilizer produced by this method has high strength and is not easy to agglomerate and be crushed. The particles in the fluidized bed are prone to a certain degree of wear due to intense movement, so the exhaust gas needs evolutionary treatment, and the recovered fine powder is used as the product.
Conclusion:
In this article, we introduce a total of 8 types of compound fertilizer production processes around the world. However, to make good compound fertilizer, high-quality compound fertilizer production equipment is indispensable. Next, we introduce zhejiang tongli heavy machinery, China’s largest manufacturer of compound fertilizer production equipment