Indirect Drying vs. Direct Drying
Rotary dryers are commonly used in industry for drying bulk solids. Their robust construction, reliable operation and ability to handle a wide range of feed materials make them ideal for drying bulk solids.
When people refer to rotary dryers, they can usually default to referring to direct-fired dryers. Direct dryers are more commonly used than indirect dryers because of their high efficiency. However, while direct-fired rotary dryers are the drying method of choice, indirect rotary dryers can be a valuable option for specific processing needs.
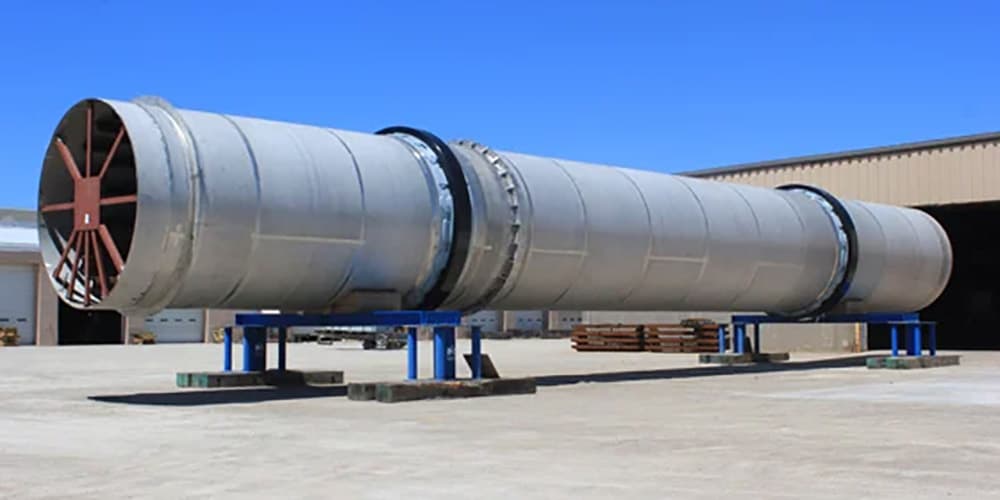
Differences between indirect and direct fired dryers
Principle of operation
Both types of dryers consist of a rotating cylinder in which the material is processed, but they use very different methods to process the material.
Direct-fired dryers rely on direct contact between the material and the process gas to effectively dry the material. Efficiency can be further improved by having lifting plates mounted on the inner walls of the dryer. These lifting plates lift the material, causing it to tumble and pass through the stream of process gases, thus maximizing the heat transfer between the material and the drying medium.
In contrast, indirect combustion dryers do not use direct contact between the process gas and the material to dry the material. In fact, these are two of the main advantages of the indirect rotary dryer:
- It avoids the problem of entrainment of fine particulate material in the process gas, which can be a nuisance when processing fine particulate material in a direct dryer.
- It allows for a tightly controlled processing environment, a highly desirable characteristic for materials that may burn in certain settings or materials that cannot come into contact with the process gas.
Indirect dryers rely on heat from the cylinder shell to dry materials by conduction and radiation. As a result, the indirect dryer will not benefit from the presence of lifting plates since there are no treatment gases passing through the cylinder. In addition, indirect dryers require fewer exhaust gas treatment units because the exhaust gases from the combustion furnace are separated from the process gases.
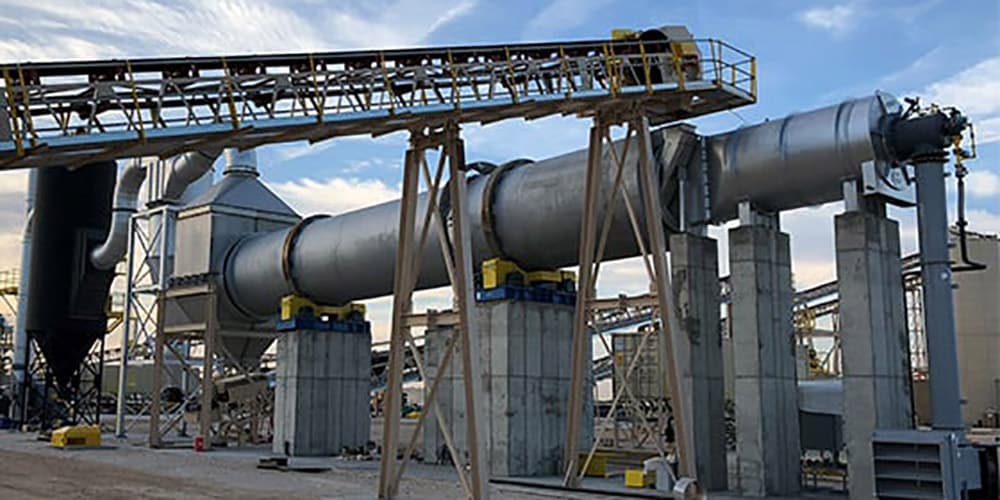
Materials of construction
The main differences between direct and indirect drying in terms of equipment materials are as follows.
Direct drying equipment.
- Usually made of carbon steel.
- Because the internal temperature of the direct drying equipment is relatively low, there is no need for special high-temperature resistant materials.
Indirect drying equipment.
- Usually made of high-temperature alloy materials.
- This is because the cylinder shell of indirect drying equipment needs to withstand continuous high temperature environment.
The reasons for using high temperature alloys in indirect drying equipment are.
- In the process of indirect drying, the heat is transferred to the material through the cylinder shell, and the cylinder shell is in the high temperature state for a long time.
- High-temperature alloys have better high-temperature resistance and strength, which can maintain the structural integrity of the equipment in a high-temperature environment.
- The use of high-temperature alloy can extend the service life of the equipment, reduce the equipment damage caused by high temperature.
This difference in material selection directly affects the cost and applicability of the two types of drying equipment. Indirect drying equipment is typically more expensive to manufacture than direct drying equipment due to the use of more expensive high temperature alloys. However, this choice of material allows indirect dryers to operate under more severe conditions and is particularly suited to handling temperature sensitive or flammable and explosive materials.

Industrial Uses/Applications
The main differences between direct and indirect drying in terms of fields of application are as follows.
Application fields of direct drying.
- Widely used in chemical industry, light industry, medicine and many other industries.
- Applicable to the drying of most common bulk solid materials.
- Commonly used to deal with high temperature resistant, non-flammable and non-explosive materials.
- Suitable for mass production and continuous operation.
Application fields of indirect drying.
- Mainly used in some industries with special needs, such as sugar, medicine, chemical fertilizer, compound fertilizer and so on.
- Suitable for materials that are flammable, explosive or cannot be in direct contact with gas.
- Suitable for dealing with fine, easy to fly materials, such as pigments.
- Suitable for products with high requirements on drying environment.
- Commonly used in the drying of heat-sensitive materials, can better control the drying temperature and environment.
Special application.
- Indirect drying is more suitable to deal with temperature-sensitive materials, such as some pharmaceutical and food materials.
- Direct drying is more suitable for industrial materials that require high efficiency and high volume processing.
Environmental control.
- Indirect drying can better control the drying environment, suitable for product quality requirements of strict occasions.
- Direct drying is more suitable for common industrial products with less strict requirements for environmental control.
In general, direct drying is widely used in most industrial fields because of its high efficiency and wide range of application. Indirect drying is more often used for special needs, especially in the treatment of flammable, explosive, heat-sensitive or fine materials with obvious advantages. The choice of which drying method needs to be based on specific material characteristics, production needs and quality requirements to be considered comprehensively.

Cost comparison
Indirect drying and direct drying have the following main differences in cost.
Equipment cost.
- Indirect drying equipment usually costs more. This is because indirect drying equipment needs to be made of high temperature resistant alloy materials to withstand the continuous high temperature environment.
- Direct drying equipment is generally made of ordinary carbon steel, which is relatively low cost.
Energy efficiency.
- Direct drying is usually more energy efficient because the heat is directly transferred to the material, reducing the heat loss in the intermediate link.
- Indirect drying, because the heat needs to be transferred through the walls of the equipment, is relatively inefficient and may lead to increased operating costs.
TONGLI has always been at the forefront of the industry with over 60 years of expertise in the field of heat treatment. We offer direct and indirect rotary dryers that are flexible enough to respond to the changing needs of various industries, ensuring efficient and reliable drying solutions.
If you would like to learn more about our direct or indirect rotary dryers, please contact us today! We look forward to providing you with professional support and service.