palletizing equipment robotic palletizers for fertilizer plant

What is a compound fertilizer factory robotic Palletizer
A robotic palletizer in the compound fertilizer factory is a commonly used and advanced packaging automation solution. It can effectively reduce labor costs and improve efficiency. The working principle of the palletizer is to stack packaged bagged compound fertilizers onto pallets. . At the same time, the robotic arm can also be equipped with various accessories to accurately pick up smaller packages and form them into neatly arranged loads. As an alternative to traditional/conventional manual palletizing methods, robotic automated palletizers have been widely used and generally praised in major compound fertilizer plants because of their relatively low equipment price, versatility and multi-tasking capabilities.
What role does the robotic palletizer play in compound fertilizer production?
- The robotic palletizer is an advanced system used in compound fertilizer plants, designed to automate the compound fertilizer pallet stacking process and improve efficiency and accuracy. Using the unit loading method, bagged compound fertilizers that normally require manual stacking are systematically arranged on pallets. This method simplifies the manual stacking process and is much more efficient in terms of time.
- The most important aspect of robotic palletizing in fertilizer production is the precision and consistency of the robot. Each bag of compound fertilizer is carefully picked up by a robotic arm and accurately placed on a plastic or wooden pallet according to the arrangement programmed by DCS. This process ensures stable and compact placement and proper loading of wooden pallets, ready for subsequent compound fertilizer storage and transportation. By automating this process, robotic palletizers effectively reduce the manpower and time required for palletizing, minimizing the risk of employee injury.
- To sum up, the robot palletizer has effectively changed the way compound fertilizer is packaged, providing a fast, high-precision, and effective all-in-one complex solution. Next, let us further understand the core advantages of robot palletizing.
How do robotic palletising machines work?
- robotic palletizing machines operate through a complex combination of mechanical engineering, robotics, and software programming. The palletizing robot arm is usually mounted on a fixed base and equipped with advanced sensors and end-of-arm tools.
- The robotic palletizer moves the gripper to the material position through the cooperation of each axis. Just above, when the material positioning signal is sent, the clamp moves downward through the servo motor control movement. When it reaches the height of the clamp to clamp the material, it stops descending, the end clamp opens, clamps the material, the servo motor reverses, and the clamp After rising to a safe height, the materials are sent to the palletizing position through the customer’s preset program, the clamp is opened, and the materials are coded into the designated position.
- Through repeated actions, the robot palletizers automatically stack the bagged, boxed, or other packaged products delivered by the conveyor into pallets according to the working method required by the customer’s process. It can stack multiple layers, and the buzzer alarms to remind you that it has been completed. The palletizing is completed and then rolled out for forklift transportation to the warehouse for storage.
- The entire working process of the robotic palletizing systems can set the running speed and acceleration of the X-axis and Y-axis of the guide rail to reduce the running time of the X-axis and Y-axis of the guide rail to improve efficiency. At the same time, the conveyor belt can also be installed along the X-direction of the guide rail to form an assembly line. mode, thereby greatly improving production efficiency.
What are the 9 types of robot palletizer?
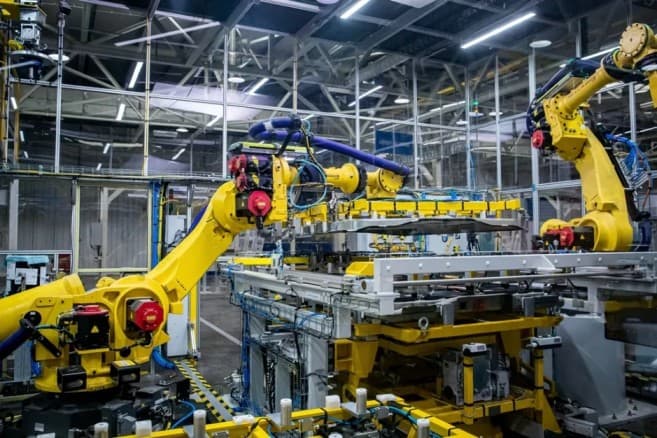
Traditional manual palletizers
In the past fertilizer production process, palletizing operations were mainly completed manually. Workers place the products on shelves or wooden pallets in sequence according to the specifications of the products or packaging boxes, and then package and fix them. Although this manual palletizing method is flexible and can handle many different types of products, it suffers from inefficiency, high labor intensity, and high safety risks. With the development of production automation, the traditional manual palletizing method is gradually replaced by more efficient automated palletizing equipment.
Pneumatic automated palletizer
Pneumatic automated palletizers mainly use pneumatic systems to achieve automated palletizing operations. Its working principle is to accurately position the goods to the target position through air pressure, and complete a series of actions such as positioning, translation, and rotation. This equipment has a simple structure and relatively low cost, and is suitable for palletizing some light and medium-weight materials. However, pneumatic automated palletizers are less efficient when handling large or heavy materials and are limited by the performance of the pneumatic system.
Robotic arm palletizing system
The robotic arm palletizer is an automated system that uses a robotic arm to complete palletizing tasks. It mainly consists of robotic arms, actuators, sensors, and control systems. The robotic arm can accurately grab and place materials, and can be programmed to perform complex palletizing operations. Due to their high degree of flexibility and precision, robotic arm palletizing systems are suitable for use in a variety of industries and production environments, and can handle materials of various sizes, shapes, and weights.
Lidar type palletization robot
Lidar-type palletization robots use lidar technology to detect the height, shape and position of materials, and use computer algorithms to automatically plan the palletizing path. The palletization robots arm accurately picks up the objects based on this information and places them at the designated location in the specified order. The advantage of this kind of palletizer is that it is highly automated and intelligent, which can significantly improve production efficiency and palletizing quality and is especially suitable for production occasions with high precision requirements.
Suction cup automatic palletizer
Suction cup automatic palletizers use a suction cup system to grab and place materials. It can accommodate materials of different sizes, shapes and weights automatically, stacking them together through specific programming rules. The suction cup automatic palletizer performs particularly well when handling flat objects. It is often used for palletizing packaging boxes, cardboard and other items. It has the characteristics of easy operation and high efficiency.
Multi-joint robot palletiser
The multi-joint robot palletiser uses a multi-joint robot arm to grab and place materials. Its high flexibility and precision enable it to handle more complex stacking tasks and has a wide range of adaptability. This palletiser can work efficiently in a limited space and is often used in production environments that require precision operations and diverse material handling.
Peel and stack palletizer robot
The peel-and-stack palletizer robot is specially used to peel and stack stacked materials for sorting or reuse. It is usually used in the recycling or remanufacturing process, and can effectively handle different types and shapes of materials, improve resource utilization efficiency, and reduce production costs.
Network automatic palletizer machine
Network automatic palletizer machine stack materials through a series of conveyor belts and grid systems. Materials are transported on conveyor belts and are caught and stacked by grids at specific locations and heights. This kind of automatic palletizer machine is suitable for handling materials of continuous production, has the characteristics of high efficiency and high degree of automation, and is widely used in the logistics and warehousing industry.
AGV (Automated Guided Vehicle) palletizing robots
AGV palletizing robots combines automatic guided vehicle and robotic arm technology. It can operate automatically in a warehouse or factory, stacking and handling materials through palletizing robot arms. AGV palletizing robots have a high degree of flexibility and automation, which can significantly improve the efficiency of production and logistics and adapt to the needs of modern smart factories.
Palletizing equipment advanced features and technologies
- High efficiency: Automated palletizing system can complete a large amount of palletizing work in a short time and are more efficient than manual labor. This is mainly due to its use of high-precision positioning and control systems and optimized palletizing algorithms, which can greatly improve palletizing efficiency while ensuring palletizing quality.
- High precision: The Automated palletizing system has a high-precision positioning function, which can ensure the stability of the stacking structure and avoid product damage. This is due to advanced sensor and machine vision technology, which allows automatic palletizers to accurately identify and position products, thereby achieving high-precision palletizing.
- Reliability: The Automated palletizing system has good durability and stability. It is not affected by fatigue, emotion, and other factors during operation and can continue to work for a long time. This greatly reduces work errors and equipment failures caused by human factors.
- Safety: No one enters the dangerous area during the operation of the fully Automated palletizing system, preventing safety hazards caused by human factors. At the same time, the equipment itself also has many safety protection functions, such as emergency stop buttons, safety shields, etc., to ensure the safety of operators.
- Small space occupied: The fully Automated palletizing system is small in size and takes up less space, which can reduce the layout restrictions of the production line. At the same time, the automatic palletizer also adopts a modular design, which can be quickly assembled and adjusted according to actual needs to adapt to different production scenarios.
- Economy: Although the cost of a fully Automated palletizing system is relatively high, as production volume increases, its use cost will become more economical and affordable. In addition, automatic palletizers can also reduce labor costs and reduce the error rate of manual operations, thereby achieving overall economic benefits.
What is the process of robot palletising system?
- Item storage: First, the items to be palletized are fed into the storage port of the palletizer. This step can be done manually or using other automated equipment, such as conveyors or automated guided vehicles (AGVs). Ensure that items enter the palletizer in an orderly manner in a predetermined manner so that subsequent operations can proceed smoothly.
- Palletizing products scan: As soon as products enter the palletizer, they are automatically scanned. The scanning device collects information about the item, including size, weight, shape, etc. This data is critical to subsequent palletizing operations, ensuring that each item is handled and placed correctly.
- Palletizing planning: The palletizing machine automatically plans the best palletizing plan based on the scanned item information. This plan will comprehensively consider factors such as the size, weight, shape, and quantity of the items, as well as the working efficiency and stability of the palletizer. The optimized palletizing solution not only improves efficiency but also ensures stacking safety and stability.
- Palletizing product location: After planning is complete, the product precisely positions each item based on its size and shape. The positioning process ensures items are picked and placed accurately, allowing for efficient palletizing operations.
- grabbing: Palletizing robot arm or other grabbing devices to remove items from the storage opening. The gripping device adjusts according to the characteristics of the item, ensuring a firm and reliable grip every time. The robotic arm moves the items to a predetermined positioning position in preparation for palletizing.
- Automatic palletizing: Once the product is grabbed and positioned in the appropriate location, the palletizer automatically stacks the items according to the planned stack. The weight and stability of the items are taken into consideration during the automatic palletizing process to ensure that each layer of the stack is safe and secure. This process requires a high degree of precision and coordination to avoid items tipping or collapsing.
- Outbound operations: After the robot palletizing is completed, the items will leave the palletizer through the outlet and enter the next logistics link. Outbound delivery can be achieved through automated equipment such as conveyor belts or AGVs, ensuring that items can be quickly and safely transferred to subsequent processing or transportation stages.
Waht are the adventages of palletising robots?
- Palletising robots exhibit excellent flexibility in the production process and can adapt to changing process requirements and diversified production needs.
- Undertake complex manual processes that were difficult to automate in the past and did not meet ergonomic standards, significantly reducing the workload of employees and improving operating comfort.
- Palletising robots significantly reduce the risk of employee injury and infection, such as by using advanced human-machine collaborative grippers to ensure safety and operational precision
- Complete repetitive processes with high quality without the need for additional investments based on workpiece type or production mode, robotic palletizers significantly improve production efficiency and product consistency
- By integrating advanced sensing systems, the robotic palletizing system not only improves productivity but also increases the complexity and intelligence of the equipment, thereby optimizing the entire production process.
The palletising robots can be used in various types of compound fertilizer production lines, including organic and inorganic compound fertilizer production lines, cow manure fertilizer production lines, chicken manure fertilizer production lines and NPK compound fertilizer production lines. Robotic palletizers are used in different types of compound fertilizer production lines because of their versatility and compact design. They are classified according to their configuration and structure. They can be divided into single grippers, double grippers, with stacking trolleys, and without stacking bags. Cars and other types. Other types of palletizers, such as 6-axis and 7-axis ones, are not suitable for compound fertilizer plants due to their high requirements on the working environment.
How to choose the right palletising robot for fertilizer plant?
- Load and reach: The first step is to evaluate the weight of the fertilizer bag to be palletized, there are 50kg and 25kg and the required load capacity of the palletizing robot arm. Generally, the load capacity and arm span of a palletising robot arm are positively related. Even if the cargo itself is light, if the pallet size is larger, a robotic arm with a longer reach may be required. Therefore, a combination of load capacity and reach length needs to be considered to ensure that the palletizer can cover the required working area and safely handle goods.
- Space and floors: The size of the space and the floor it is located on have a big impact on the choice of palletizer. If you are on the first floor and there is enough space, almost any type of robotic palletizer is an option. But if space is limited, you may want to opt for a compact palletizer. In addition, when installing a palletizer upstairs, you also need to consider the floor height, floor load-bearing, and difficulty in transporting and installing the palletizing automation equipment. Large-scale industrial robots may weigh more than 1 ton, and the floor load-bearing capacity of some old factory buildings may be only 300 kilograms, which may not meet the requirements even through reinforcement. Therefore, it is necessary to select equipment suitable for the load-bearing capacity of the floor.
- Production line rhythm: The production line cycle determines the speed requirements of the palletizers. If the production line speed is fast, you usually need to choose high-speed industrial robots instead of collaborative robots. If the fertilizer production line speed is so high that you need to grab two products at a time to keep up with the beat, you need to consider a palletizer with a higher load capacity. For extremely high-speed production lines, a full layer of palletizers may be required, or two palletizers may be used to work simultaneously to meet demand.
- Cost: Cost is an important factor that must be considered when selecting a palletizing automation system. Imported robotic arms are usually one to two times more expensive than domestic ones. Therefore, enterprises should choose appropriate equipment based on the actual budget. Generally speaking, the price of a robotic arm is directly proportional to its load capacity and arm span. It is recommended to leave a margin when choosing, but do not waste too much.
- Special functional requirements: Some production lines have special functional requirements. For example, multi-variety and small-batch production lines often need to change products and production line configurations, which requires the selection of palletizers that are compatible with multiple specifications. If you need to palletize cartons with labels facing outwards and palletize bags with bag mouths facing inward, you need to choose a robotic equipment with these functions or ask the supplier to customize the design in advance.
Common palletizing mistakes and how to solve them?
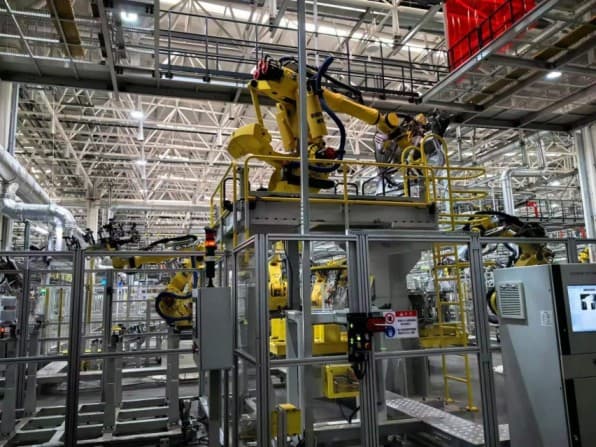
Palletizing solutions: excessive palletizing errors
The main reason for excessive palletizing errors is often due to factors such as insufficient accuracy of the sensor, inaccurate calibration of the robotic arm, or environmental interference. Palletizing solutions include:
- Improve sensor accuracy: increase the number of high-precision sensors and optimize the layout of sensors to ensure that key positions in each palletizing process can be accurately monitored.
- Calibrate the robotic arm: Calibrate the robotic arm regularly to ensure the accuracy of its movement path and grasping position.
- Reduce environmental interference: Set up protective measures in the palletizing area to reduce the interference of environmental factors such as light, dust and temperature on the sensor, thereby improving palletizing accuracy.
Uneven robotic palletising stacking problem
The uneven robotic palletising of pallets is usually caused by the platform that the palletizer moves up and down is not stable enough or the traction force is uneven. Solutions include:
- Add rollers: Add rollers under the palletizing platform to reduce friction and improve the stability of the platform.
- Adjust the motor speed: Optimize the motor speed control to make the traction force more uniform and stable, thereby ensuring the stability of the palletizing platform when moving up and down.
- Regular maintenance of the platform: Regularly check and maintain the balance and stability of the palletizing platform, and replace worn parts in a timely manner to ensure that the platform remains flat during the work process.
Robotic palletizing loss of item problem
Loss of items from the palletizer may be caused by the machine’s swing arm being too long, too fast, or the grip being weak, causing boxes to fall.
- Adjust the length of the swing arm: According to specific production needs, reasonably adjust the length of the machine’s swing arm to avoid unstable grasping caused by too long a swing arm.
- Adjust the speed: According to the complexity of the palletizing task, appropriately reduce the working speed of the machine to ensure the stability of the grabbing and handling process.
- Improve the grabbing mechanism: Optimize the design of the grabbing mechanism, add anti-skid devices, improve the grabbing force, and ensure that the material can be firmly controlled during each grabbing process.
Insufficient closure of robotic palletizing systems
The robotic palletizing systems is not closed enough, which can easily cause boxes to fall and scatter, and it can also cause safety hazards to surrounding personnel. Solutions include:
- Add fences and guards: Increase or adjust the height and density of fences and guards around the palletizer to form a more enclosed operating area and prevent materials from falling.
- Safety protection devices: Install safety protection devices, such as safety doors, light curtains, etc., to ensure that the robotic palletizing systems automatically stops working when personnel approach the dangerous area.
- Regular inspection: Regularly check the integrity and safety of closed facilities, repair or replace damaged fences and guards in a timely manner, and ensure the effectiveness of closed measures.
Robot palletising system control failures
The control failure of the robot palletising system may be caused by program errors, sensor failure, motor drive system failure, etc. Solutions include:
- Check electrical connections: Regularly check the electrical connections of the palletizer to ensure that all connections are secure and not loose or damaged.
- Change the control program: When a program error is discovered, promptly change and update the control program of the electronic control panel to ensure that the system logic is correct and runs smoothly.
- Maintain sensors and motors: Regularly inspect and maintain sensors and motor drive systems to ensure they are working properly. If necessary, replace failed sensors or faulty motors.
- System testing: After each maintenance and update, comprehensive system testing is performed to ensure that the robot palletising system control can operate normally under various working conditions.
How much does a Fanuc/Abb robot palletizer system cost?

- Let’s take the M410B model commonly used in compound fertilizer production lines as an example. The market price of an M410B fanuc brand palletizer ranges from about US$35,000 to US$55,000 depending on the configuration, while ABB’s palletizing robot of the same model slightly more expensive, around US$40,000 to US$80,000. Well-known brands such as ABB, FANUC, KUKA, and Yaskawa are relatively expensive due to their high quality and reliability. Domestic brands such as the compound fertilizer-specific palletizing robot produced by Tongli have advantages in terms of cost performance.
- But we should pay attention to that the automatic palletizer machine is not only a mechanical arm but also has a corresponding electrical control system and operating system. In the compound fertilizer production line, a palletizing robot packaging line consists of multiple parts, such as grippers, conveyor belts, and other components. Automatic bag sewing machine, fully automatic folding machine, etc., so just buying a palletizing robot is not enough. The detailed price must be adjusted based on the customer’s needs.
- Installation and commissioning costs of the robotic palletizing system vary depending on the complexity of the equipment and plant conditions, but usually range from US$5,000 to US$20,000. Regular maintenance and upkeep costs approximately $1,000 to $5,000 per year, depending on frequency of use and work environment. Operator training and after-sales service costs also need to be included in the budget.
The world’s leading palletizing robot company: ABB/Fanuc/kuka/yasakawa
- FANUC is a world-renowned automated palletizing manufacturer headquartered in Japan, focusing on providing CNC systems, CNC devices for automated production lines, and industrial robots. It was founded in 1956 and developed from Fujitsu Fanuc, a subsidiary of Japan’s Fujitsu Communications Manufacturing Co., Ltd. (now Fujitsu Corporation) responsible for the automation business. At the beginning of its establishment, Fanuc was committed to the research, development and promotion of factory automation. In 1972, it became independent from Fujitsu and became an independent company. Since then, FANUC has made remarkable achievements in the fields of CNC systems and robotics, becoming a leader in the global industrial automation field.
- ABB: ABB was founded in 1988. It is a famous large-scale automated palletizer multinational company in Switzerland. It is headquartered in Zurich, Switzerland and is one of the top ten multinational companies in Switzerland. Acebram Baffari is one of the world’s largest companies producing industrial, energy, and automation products. Processing industry: chemistry, petrochemicals, pharmaceuticals, pulp and paper, oil refining; Instrumentation and facilities: electronic instruments, television and data transmission equipment, generators, water conservancy facilities; Communication channels: integrated systems, collection and release systems; Construction industry: commercial and Industrial buildings.
- KUKA Palletizing Robot Co., Ltd. was established in Augsburg, Bavaria, Germany in 1898. It is one of the world’s leading industrial palletization robot manufacturers. KUKA Robotics has more than 20 subsidiaries around the world, most of which are sales and service centers, including: the United States, Mexico, Brazil, Japan, South Korea, Taiwan, India and most European countries.
- Yasakawa is a leading global robotic palletizer manufacturer in Japan. Its industrial palletizing products division provides various types of robot palletiser to meet the needs of different industries. Yaskawa palletising machines are known for their high quality, efficiency and reliability and are widely used in various fields of manufacturing.
Special concerns when you choose the palletizing equipment
- Consider the factory’s on-site working conditions: The environmental factors of the factory are crucial to the selection and installation of palletizer robot. Factors such as space limitations and layout limitations will affect the selection and use of robots. When selecting a robot palletizers, the actual conditions of the factory must be fully considered to ensure that the selected robot can operate normally in that environment and will not affect other production activities.
- Reliability and Maintenance: When purchasing a palletizing robot arm, you need to consider its reliability and maintenance costs. Highly reliable, easy-to-maintain robotic equipment can reduce production interruptions and repair costs and increase production efficiency. Therefore, when choosing a robotic palletising, you must not only pay attention to its performance and functionality but also consider its long-term operation stability and maintenance costs.
- Special function requirements: Some production lines may have special functional requirements, such as multi-variety and small-batch production, which require rapid change of working modes. In this case, it is necessary to choose a automatic palletizing robot that can meet a variety of specifications. Therefore, understanding the special functional requirements of the production line can help determine the appropriate robotic palletizer.
Conclusion: The future development trend of palletizing automation
- Multifunctionality: In the future, palletising robots will not only be limited to a single function but will increasingly have multiple functions. In addition to completing traditional palletizing tasks, they can also have other production functions, such as packaging, marking, inspection, etc. By integrating multiple functions into one, the number of equipment and floor space on the production line can be reduced, thereby reducing production costs and improving production efficiency.
- Networking: Automatic palletizer of the future will be connected to other devices, systems, and the Internet to enable real-time data collection, analysis, and sharing. They will become an important part of factory intelligence, seamlessly connecting with production planning systems, warehouse management systems, etc., to realize the automation and intelligence of production lines. Through networking, real-time monitoring and remote control of the production process, as well as remote access and analysis of production data, can be achieved, thereby further improving production efficiency and management levels.
- Environment Friendly: In the future, palletizing solutions will pay more and more attention to environmental protection and energy saving. They will use more environmentally friendly materials and technologies to achieve the goals of low-carbon production and efficient use of energy. For example, through optimized design and energy-saving control systems, energy consumption and waste emissions can be reduced; at the same time, the use of renewable energy and environmentally friendly materials can reduce negative impacts on the environment. Through green robot palletizing, sustainable development and environmentally friendly production models can be achieved.