Feasibility of fermenting cow dung fertilizer production plant – detailed guide

Introduction
- Dry cow dung contains 10%-20% crude protein, 1%-3% crude fat, 20%-30% nitrogen-free extract, and 15%-30% crude fiber, so it has high nutrients. Green ecological organic fertilizer is made of cow dung and crop straw as the main raw materials and is produced by fermentation using multi-dimensional complex enzyme bacteria. Multi-dimensional complex enzyme bacteria is a microecological fermentation preparation composed of hundreds of beneficial microorganisms such as heat-resistant Bacillus, lactic acid bacteria, bifidobacteria, yeast, etc. that can produce a variety of enzymes. It is non-toxic, pollution-free, and safe to use for humans and animals. It can fix nitrogen, and dissolve phosphorus and potassium. At the same time, it can decompose the residual substances of chemical pesticides and fertilizers. It has the effects of increasing production, improving quality, and resisting diseases in the planting and breeding industries. The cow dung dryer is one of the key equipment in the cow dung fermentation process.
Development trend of Cow Dung Fertilizer
- Due to the continuous advancement of China’s rural policy, the fertilizer industry has been rapidly developed and applied in China, and organic fertilizer equipment has also been developed at a high speed. With the intensification of market segmentation, China’s fertilizer equipment will develop in the direction of lightweight, large-scale, high-end, and integrated. The integration of China’s fertilizer processing machinery industry has further intensified, and organic fertilizer equipment will also develop in the direction of lightweight, large-scale, high-end, and integrated.
- The cow dung after composting has achieved harmless and stable treatment, and has met the basic conditions for resource utilization as organic fertilizer, but it has not yet reached the level of commercial sales in the market. Its application effect and scope of use are still limited. Therefore, it is necessary to further process the compost material into powdered or granular organic fertilizers and organic-inorganic compound fertilizers with commercial properties through subsequent fertilizer-making processes.
- Due to the low overall nutrient content of compost products, they can only be used as a part of base fertilizer, which is different from the existing agronomic planting habits and crop fertilizer requirements. Therefore, it is necessary to add a part of nitrogen, phosphorus, and potassium fertilizers to organic fertilizers to make commercial organic-inorganic compound fertilizers. Organic-inorganic compound fertilizer has dual characteristics, namely, it has the characteristics of long-lasting fertilizer effect, improving soil, and activating inorganic nutrients in the soil, and it also has the characteristics of high nutrients and fast fertilizer effect of inorganic fertilizer. The advantages complement each other and make up for their respective shortcomings, achieving the combination of fast-acting and long-term fertilizer.
- Therefore, the planning and design of organic fertilizer plants usually take organic-inorganic compound fertilizer as the leading product, while taking into account the production of organic fertilizer products.
The process of fermenting cow dung using a cow dung dryer
The production process of commercial organic fertilizer mainly includes crushing, batching, mixing, granulation, Cow dung drying equipment, cooling, screening, and packaging. The production capacity of a single production line should be 1-10t/h. If it is too small, it will not reach the economic scale, and if it is too large, it will increase the difficulty of transportation and storage of raw materials and finished products.
Fermentation method of cow dung
Collect cow dung and urine, mix with hay and rotten silage to make compost, and let it ferment. Use a compost turner to fully ferment the cow dung during the fermentation process. This can only be achieved by timely and uniform compost turning. Now some places are very dry and some places are very wet, which will affect the fermentation quality. It is recommended to use a compost turner.
- Add auxiliary materials
Add 10%-15% of straw, rice bran, and other auxiliary materials to the fresh pig manure to adjust the moisture, ventilation and carbon-nitrogen ratio. The carbon-nitrogen ratio is between 30-40, and the moisture content of the pig manure is controlled at about 60%, which is based on the watermark between the fingers but not dripping. - Inoculation of fermentation agent: Add 0.04% of Rujin probiotic fermentation agent (first mix the fermentation agent with 10 times bran and then add it to the pig manure to mix). After mixing, transfer it to the fermentation tank and stack it in a trapezoidal shape with a width of 2m on the top, 3m on the bottom, and 1.2m high. The length depends on the length of the site. Compact and seal it, and cover it with plastic sheeting or rainproof cloth for anaerobic fermentation. The fermentation time is 15-40 days (depending on the season).
- Turning the materials (mechanical or manual): Turning the materials once every 10 days at noon in winter and spring, and once every 5 days in summer and autumn, so that the fermentation temperature of the materials is controlled between 55-70℃. The fermentation temperature can be measured and controlled by a rod-type digital thermometer. Fermentation is successful after turning the pile three times.
What is the process flow of cow dung fertilizer fermentation process?
The characteristics of this process are as follows: the mechanical compost turning operation is highly maneuverable, and the use of strip windrows is conducive to the loss of water in the later stage of composting; the requirements for civil engineering are low, and no matching fermentation tank is required, and the composting can be made outdoors, saving construction investment; the composting site area needs to be relatively large; the outdoor composting in northern regions has poor thermal insulation in winter, and the composting cycle needs to be extended or composting needs to be stopped seasonally; when composting in the open air, the material pile is easily affected in the rainy season, and it is recommended to add a rain shelter if conditions permit.
2. Grinding and mixing of organic cow dung ingredients
- The composted materials and inorganic fertilizers such as N, P, K, and other additives are crushed, proportioned, and mixed in a certain proportion through a material crusher and a horizontal mixer using a batching bin.
- The function of this system is to crush, proportion and mix various raw materials such as composted materials and inorganic fertilizers such as nitrogen, phosphorus and potassium, and other additives in a certain proportion. Based on many years of experience, the equipment-matching recommendations are as follows:
- The vertical crusher is used to crush cow dung compost, which is not easy to stick to the wall and is not easy to block. The multi-layer turbulent chain hammer structure improves the crushing performance; the continuous automatic batching system is suitable for the dynamic metering and batching control of organic fertilizer raw materials; the mixing operation is equipped with a double-shaft continuous mixer, which has good sealing and sticky materials are not easy to adhere to the root of the mixing shaft.
3. Cow dung fermentation Granulation process
- A new type of organic fertilizer granulator is used to granulate the material. The function of this system is to make the material into granules after the crushed ingredients are fully mixed.
- The flat die granulator is suitable for granulation. Its advantages are: wide adaptability of raw materials, especially suitable for organic materials, wide requirements for raw material density and raw material moisture, and raw materials do not need to be dried;
- The roller diameter is large, the template can be used on both sides, the material is evenly distributed in the compression chamber, the granulation is stable, the granulation rate is high, and the finished granules are uniform in appearance and not easy to break;
- No water is added during the entire granulation process, saving the cost of subsequent granule drying;
- The raw material grinding fineness requirement is not high, and the granulation raw materials (after composting) generally do not need to be finely ground, fine stones can be directly crushed, which is not easy to block the die holes of the pressing plate
4. Cow dung granular particle screening and recycling system
- The granules output from the granulation molding system have certain differences in particle size and need to be screened and graded. The selected rotary screening machine requires low vibration, low noise, easy screen change, and a screen surface cleaning device.
- It is recommended to equip the automatic return system to screen out the unqualified large and small particles through the belt elevator, and then re-crush them and send them to the granulator for further granulation, which helps to improve the continuous operation capacity of the production line.
5. Cow dung organic fertilizer drying
Use an organic fertilizer dryer, or cow dung processing machine, to further remove moisture from the sieved particles to meet the standard requirements for organic fertilizer moisture content. Generally, a rotary dryer is used.
6. Organic fertilizer cooling
Cooling the pellets with a cooler helps to store and maintain the pellets. The hot pellets output by the cow dung drying machine enter the countercurrent cooler from above. Dry air enters from the bottom of the cooler under the action of the cooling fan and fully exchanges heat with the hot and humid pellets falling from above. After cooling, the difference between the pellet temperature and the ambient temperature is less than 5°C.
7. Packaging
The cooled granular cow dung materials are transported to the finished product warehouse by bucket elevators. The granular materials are quantitatively weighed and packaged by automatic packaging scales.
Cow dung fermented fertilizer production line control system
The entire production line has many equipments. To ensure normal and orderly continuous production, the control system is recommended to adopt a combination of centralized display, centralized control and on-site control in the central control room. A control cabinet, a console with a simulation screen, and a computer system are set up in the control room. The equipment can be started and stopped through the simulation screen. For equipment such as granulators that are far away, an on-site control cabinet is equipped to facilitate on-site operation. The computer controls the batching and mixing system in real-time according to the formula, and can dynamically monitor the operating status of the equipment. It has the functions of setting, modifying, and storing formulas and batches, and has the functions of generating and printing shift, daily and monthly reports of various materials, and total output, which is convenient for production management.
Organic cow dung/chicken manure fertilizer manufacturing flow chart
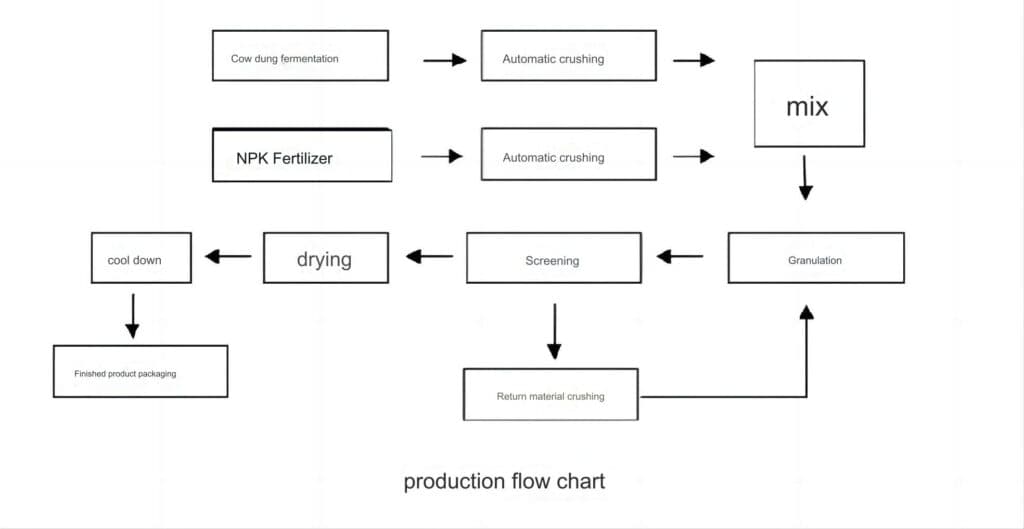
Cost calculation
The cost of raw materials such as cow dung and licorice is low and can be ignored. The budget for the main production equipment is as follows:
Production equipment | Amount Required | Remark |
---|---|---|
Such as fermenting bacteria | 2857.14-4285.71 US Dollars | Determined according to production scale |
Compost turning machine | 37140-57142 US Dollars | |
Material crusher 2 sets | 7000-10000US Dollars | |
Organic fertilizer granulation and drying equipment | 150000-200000 US Dollars | |
Cooling machine | 140000-180000 US Dollars | |
Packaging machine | 30000~60000 US Dollars | Determined according to specific production situation |
Labor cost | To be estimated | |
Total | 500000$ |
The above production process needs to be carried out indoors. It is recommended to build a light steel structure factory with an area of about 500 square meters and a cost of about 50000 US dollars but notice this is just an estimate and in reality, the equipment specification and process flow will be more complex and more expensive, also like eletronic control system, cables, installation material, freight, tax are not included in the price above. So just to give you an idea of how much the project might cost.