How to solve compound fertilizer finished product caking/clumping problem?

What is compound fertilizer caking/clumping?
Compound fertilizer caking is a problem often encountered in fertilizer production and storage. It not only affects the quality of the product, but also brings a lot of trouble to farmers when applying fertilizer with the development of mechanization of fertilization. Caking of compound fertilizer is a complex chemical and physical process, involving the influence of internal and external factors of the fertilizer. Only by correctly understanding and mastering the causes of compound fertilizer caking can we take appropriate methods to prevent fertilizer caking.
Does compound fertilizer clumping equal to Agglomeration?
The answer is no. Compound fertilizer caking refers to the caking of finished compound fertilizer due to various reasons. Agglomeration generally refers to the process of compound fertilizer changing from powder to block in the granulator during the granulation stage. Therefore, the focus of our article is on how to solve the caking problem of finished compound fertilizers.
What are the 7 main factors causing compound fertilizer caking?
The main raw materials for compound fertilizer production in my country are: urea, ammonium chloride, ammonium nitrate, ammonium sulfate, diammonium phosphate, monoammonium phosphate, superphosphate, heavy calcium, potassium chloride, potassium sulfate, etc. These fertilizers have larger Solubility, so compound (mixed) fertilizers made from them tend to agglomerate during storage and transportation.The factors that affect the agglomeration of compound (mixed) fertilizers are mainly reflected in the following aspects:
- The moisture content of the product is too high, and the salt between particles dissolves – the easier the crystallization process is, the easier it is to agglomerate.
- Packaging temperature If the packaging temperature is too high, the moisture inside the product cannot be fully released and it is easy to agglomerate; if the product temperature is too low, it is easy to absorb moisture from the air and it is easy to agglomerate.
- Storage Pressure When fertilizer particles are under heavy pressure, the particles are in closer contact, the particles are deformed, and the contact surface is enlarged, causing agglomeration.
- Storage time Fertilizer products will continue to undergo certain reactions for a period of time after packaging, such as moisture absorption, dissolution, recrystallization, metathesis between salts, etc. This process lasts for a long time, so the longer the storage time , the more severe the agglomeration.
- The shape of the particles: The particles are small, irregular in shape, multi-angular, and have a large specific surface area and are more likely to agglomerate.
- Uniformity and hardness of particles If the particles are uneven, the contact area will increase; if the hardness is low, they will be easily crushed, resulting in an increase in the contact area and easy agglomeration.
- The composition and content of impurities in the particles are different. Impurity compositions with different contents will affect the degree of crystallization of salts and the size of crystalline particles, thereby affecting the degree of agglomeration.
Chemical composition of compound fertilizer cause clumping
- The composition of raw materials is an intrinsic factor that affects fertilizer agglomeration. The raw materials used in the production of compound fertilizers mainly include urea, ammonium nitrate, ammonium chloride, ammonium bicarbonate, monoammonium phosphate, diammonium phosphate, heavy calcium, superphosphate, chloride Potassium, potassium sulfate, etc. These raw materials have varying degrees of hygroscopicity. When different raw materials are mixed, the critical hygroscopic point of the mixture and the ratio of the monomer substances will be significantly reduced, making it more hygroscopic.
- In the presence of moisture, chemical reactions can occur between certain ingredients to form double salts and solid solutions. For example:
NH4NO3 + KCl KNO3 + NH4Cl
(NH4)2HPO4+2KNO3 (NH4·K)HPO4+ (K·NH4) (NO3)2
These reactions can continue into the finished product after packaging. During storage, such chemical reactions on the particle surface can easily produce crystal bridges. Therefore, when producing compound fertilizer, it is necessary to fully understand the compatibility of each raw material, and perform pretreatment when necessary, such as superphosphate pretreatment, and control the reaction that may release crystal water inside the compound fertilizer to prevent Clumping.
- Another reason for clumping due to chemical reactions is that the crystal structure of certain substances changes when the temperature changes drastically. For example, at 32.1°C and 84.2°C, the volume of ammonium nitrate also changes with the change of crystal structure, accompanied by energy. absorption or release. Therefore, it is very necessary for ammonium nitrate-containing compound fertilizers to be fully cooled before packaging and storage.
Hygroscopicity and ambient humidity cause compound fertilizer clumping
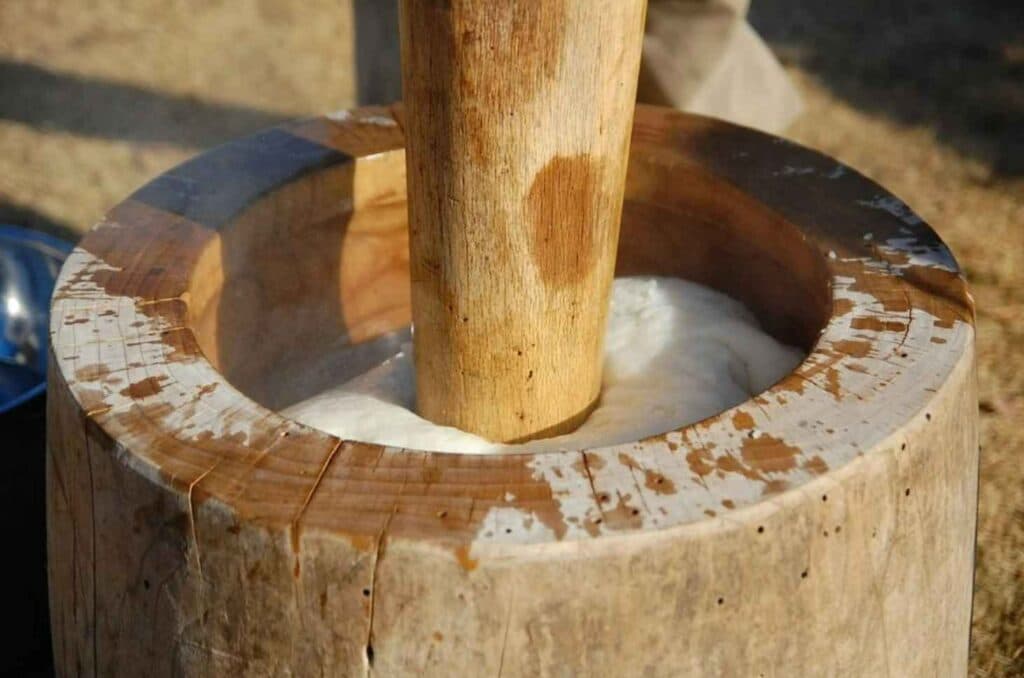
- After the particle surface absorbs water, a saturated solution quickly forms. After that, as the water evaporates or is absorbed by other dry particles, the dissolved components precipitate and crystallize. Therefore, the particle surface continuously undergoes a process of dissolution and recrystallization, forming crystal bridges that lead to Clumping.
- The composition of fertilizer is different, and its critical relative humidity is also different. The critical relative humidity of a mixture of two or more basic fertilizers is usually lower than that of any single fertilizer. For example, the critical relative humidity of a mixture of ammonium nitrate and urea at 30°C is only 18%. Therefore, the use of these two fertilizers should be avoided in the production of compound fertilizers.
- During production, attention should be paid to the influence of environmental humidity. When packaging compound fertilizer, woven bags lined with film that are not easily damaged should be used, and it is best to fold the edges and seams.
Product moisture content affects compound fertilizer clumping: Formulas and theoretical support
- Moisture is the main factor affecting fertilizer caking. Any caking mechanism is related to the liquid phase content of the fertilizer. On the one hand, the presence of moisture will cause capillary adhesion and produce crystal bridges; on the other hand, moisture will cause the fertilizer particles to soften and deform under pressure, increasing the contact area between particles and increasing the bonding between particles. strength.
- There are two main sources of moisture: one is from the residue inside the fertilizer during production, which is squeezed to the surface of the particles under pressure; the other is from the surrounding air, which increases the moisture content of the fertilizer through moisture absorption. The causes of moisture absorption can be summarized as two points: capillary condensation and drop in vapor pressure. Capillary condensation is caused by changes in the saturated vapor pressure of the curved liquid surface. According to Kelvin’s equation:
lnpr/p0=k/r
where pr—the vapor pressure of the liquid on the curved surface;
p0—vapor pressure of plane liquid;
r — radius of curvature of the liquid surface;
k — constant, a constant value for liquid substances at a certain temperature.
- It can be seen that the vapor pressure of the liquid is related to the shape and radius of curvature of the liquid surface. P concave < P0 < P convex. Because the moisture between the particles will form a concave liquid surface, the saturated vapor pressure is lower than the vapor pressure of the flat liquid, and the water vapor in the air can easily reach saturation here, resulting in steam condensation.
- The drop in vapor pressure refers to the saturated solution formed by the inorganic salts on the particle surface dissolved in the adsorbed water. Its vapor pressure is lower than the saturated vapor pressure of pure water. When the water vapor pressure of the air is higher than this value, hygroscopicity will occur.
- The moisture contained in the fertilizer particles promotes the dissolution and recrystallization of the powder surface, causing crystal bridges to form in the pores of the powder. Over time, the crystals combine with each other and gradually form agglomerates. Secondly, it is impossible to achieve complete reaction of chemical fertilizers during the production process. Due to the influence of thermal effects, chemical reactions occur continuously inside the fertilizer. At this time, there is a trace amount of solution in the fertilizer, which dissolves and re-deposits the crystals. As a result, crystal salt bridges are formed and the fertilizer agglomerates. .
- Therefore, the allowable moisture content (free water) requirements in finished fertilizers are proposed for different compositions and contents of fertilizers. The lower the moisture content of the pellets, the less likely they are to clump. Generally speaking, fertilizers with high nitrogen content require a higher degree of drying, especially for compound fertilizers containing ammonium nitrate or urea.
Effect of temperature on caking of finished fertilizer products
The influence of temperature on caking is mainly reflected in packaging and storage.
Why packaging temperature is crucial to prevent product compound fertilizer from clumping?
Packaging temperature has a particularly significant impact on caking. If the temperature during packaging is too high, the inorganic salts dissolved in the residual moisture during cooling will crystallize out and form salt bridges. For example, if ammonium nitrate is packaged at a temperature of 70°C and a moisture content of 1%, then when cooled to 10°C, more than 35kg of crystals can be precipitated from 1 ton of product, which means that enough crystal bridges will be formed, leading to serious Caking, so the material should be fully cooled before packaging. For fertilizers that are directly packaged, excessive temperature will destroy the temperature of the packaging materials. Generally, they need to be cooled to below 54°C before packaging.
Why storage temperature is important to keep finished product compound fertilizer from clumping?
The higher the storage temperature of fertilizer, the more likely it is to agglomerate. During the storage process, if there is a temperature change, on the one hand, in the presence of moisture, it will cause dissolution and crystallization to occur repeatedly, prompting the formation of crystal bridges; on the other hand, it will also cause physical and chemical effects of certain substances, such as crystalline transformation. For this purpose the fertilizer must be cooled before being packed or sent to bulk storage. The storage temperature of ammonium nitrate and compound fertilizers containing ammonium nitrate should be lower than 54°C. Ammonium phosphate, ammonium sulfate or urea-ammonium phosphate only requires cooling to 71°C. The maximum storage temperature mentioned here is for drying to the specified moisture content. As the moisture content increases, the storage temperature becomes more sensitive to caking.
Important caking factor 3: Particle shape
If the roundness of the product particles is not good or fine powder is entrained, the contact area between the particles increases, promoting agglomeration. Relatively large particles and no fines will reduce the contact points between particles, thus reducing the tendency for agglomeration. If the powder contains moisture, it is more likely to cause solid dissolution and crystallization, making the fertilizer more likely to agglomerate. Therefore, there is a requirement to specify the content of qualified particles in the production of granular fertilizer.
Important caking factor 4: Particle Compressive strength
If the particles have low hardness or mechanical strength, they are prone to deformation and fragmentation during transportation and storage, and the fine powder produced increases the contact points between particles, making them prone to agglomeration.
Crucial caking factor 5: compound fertilizer Storage pressure
Increasing the storage pressure will increase the possibility of particle deformation and the contact area between particles, increasing the possibility of crystal cross-linking, thus increasing the possibility of agglomeration. Generally, fertilizers that are prone to agglomeration should be avoided from being piled too high. For example, for a 50kg package of fertilizer, the pressure on the bottom package of 20 packages is 0.35 kg/cm2. Non-clumping fertilizer can be stacked in stacks of 30 bags or more. The average pressure at the bottom of a conical fertilizer pile in a bulk warehouse can be calculated as hd/3. Among them, d is the bulk density of fertilizer kg/m3, and h is the pile height m. The pressure on the hypotenuse of the conical pile is equal to zero, and the maximum pressure at the bottom center is 2hd/3.
Crucial caking factor 6: Storage time that effects clumping
The longer the storage time, the more times the salt solution recrystallization-dissolution process on the surface of the fertilizer is carried out. If the fertilizer is under a certain pressure for a long time, the greater the deformation of the fertilizer will be, and the more obvious the tendency of agglomeration will be. Therefore, the storage time of fertilizer should be shortened as much as possible.
Crucial caking factor 6: Impurities and content that contribute to caking
High-concentration compound fertilizers are more likely to clump than low-concentration compound fertilizers. When producing high-concentration compound fertilizer, adding some water-insoluble inert substances can reduce the binding force between crystal bonds and reduce agglomeration. For example, adding more than 5% of attapulgite powder, china clay or fly ash and other inert substances to the raw materials can greatly reduce the possibility of agglomeration. In fact, it is difficult to distinguish which factor is causing caking. Fertilizer caking is usually the result of a combination of factors.
Conclusion: What are the factors causing compound fertilizer clumping
In this article, we focus on the reasons and theoretical analysis of the caking of finished compound fertilizers. We also introduce the factors that may cause the caking of finished compound fertilizers, including moisture, temperature, chemical composition, storage conditions, etc. I hope that after reading this article, you can better prevent compound fertilizer from clumping. In our next article we will focus on another way to prevent compound fertilizer from clumping, which is to use anti-caking agents. Interested friends please click on the link below to learn more.
https://youtu.be/bq8KXVNDz90?si=10iCMCWeXRiNphz1
Click here to learn more