How to use Granulator Machine to produce fully Water-soluable Fertilizer

What is high tower wet granulator machine working principle?
High-tower compound fertilizer (full name: high-tower granulated compound fertilizer) is one of the new technologies in the compound fertilizer production process. It is a melt granulation method of urea and potash fertilizer. It uses the principle of rapid crystallization after urea melts to heat ammonium phosphate. By measuring the urine and potassium slurry, and then spraying it into the high tower through the nozzle, compound fertilizer particles are produced. This fertilizer has the characteristics of uniform and smooth particles, melting holes, and no agglomeration. Regardless of appearance, internal quality and crop yield increase, it is far better than ordinary compound fertilizers sold on the market.
How to select the raw material using granulator machine?
The principle should be that the feed ratio of compound fertilizer produced by high tower granulation can be produced within a wide range. However, for urea-based compound fertilizer, since ammonium phosphate will produce a polymerization reaction to thicken the slurry, the dosage must be The w (P2O5) in the product should be controlled to <15%, and monoammonium phosphate with high phosphorus content should be used as much as possible. Diammonium phosphate with slightly poor thermal stability should not be used; the amount of molten urea should be greater than 30%, with due consideration given to the high phosphorus and nitrogen content. Higher.
How to use wet hight tower granulation method to produce nitrate based compound fertilizer?
For nitro compound fertilizer high tower granulation process, since the salt reaction between potassium chloride and ammonium nitrate makes the slurry thicker, potassium sulfate should be used as the potassium source in production. The amount of ammonium nitrate should be greater than 40%. The moisture content of the raw materials used should not be too high. Control w (H2O) to be less than 1%, and the fineness of the raw materials should not be greater than 0.5 mm.
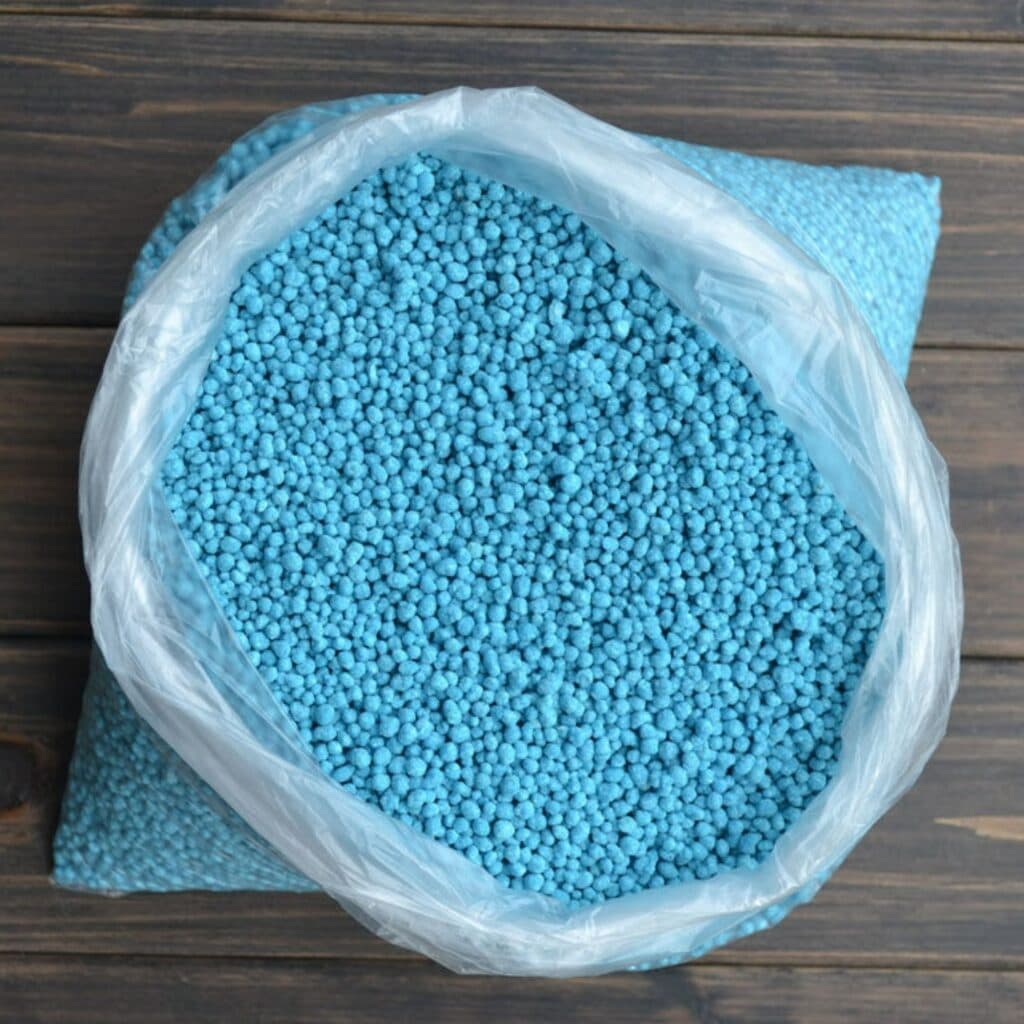
High tower pulping processes of 3 wet granulator machine
- Molten urine (or ammonium nitrate) is stirred and mixed with other ground and heated raw materials.
- Solid urea (or ammonium nitrate) is stirred and mixed with other raw materials and then heated and melted.
- Molten urine (or ammonium nitrate) is mixed with other raw materials and emulsified.
The melting temperature is generally determined by the melting point of the raw material. The melting point of urea is 132.7°C and the melting point of ammonium nitrate is 170.4°C. Adding flux to the formula reduces the melting point and lowering the temperature can reduce the production of biuret for urea, and for ammonium nitrate can reduce the risk of melting.
High tower prilling Mix granulator machine: Mixing is important
The melt and other solid raw materials are mixed under a certain stirring intensity. The end linear speed of the stirring blade and the type of stirring blade are determined according to the viscosity of the material to ensure uniform mixing of the material. An emulsifier can also be used for emulsification to improve the slurry. granulation performance. The solid raw materials before mixing are generally preheated with a heater to ensure that a large amount of solid materials will not be rapidly cooled and solidified in the mixing tank. Of course, cold materials are also used for mixing, but a reasonable mixing procedure must be designed to avoid the negative effects of cold materials.
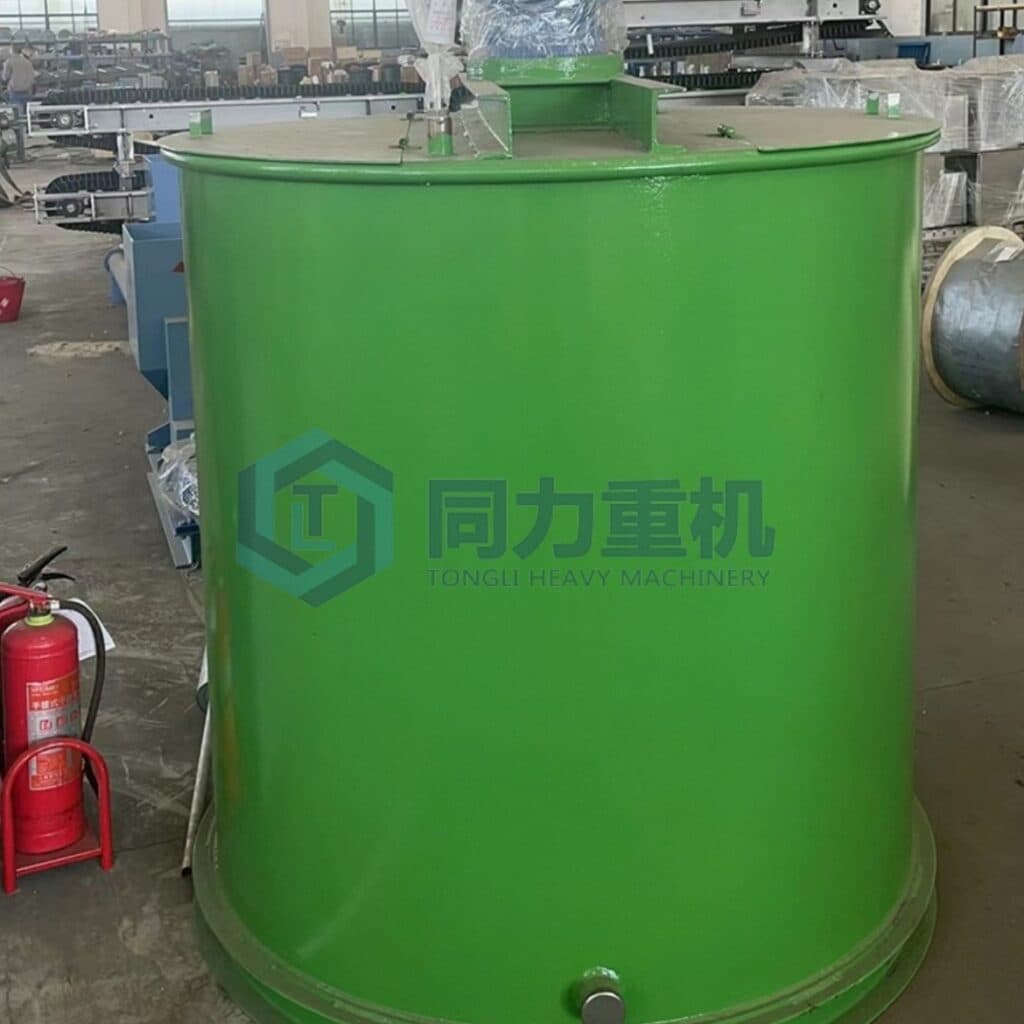
Waht is the working principle of hight tower wet granulation?
Due to the eutectic point of the mixed salt, its melting mixing temperature will be significantly lower than its melting point. Urine group is generally 100~130℃, and nitro group is generally 140~170℃. For urea-based compound fertilizer, urea and ammonium phosphate will produce a polymerization reaction:
(NH2)2CO+2NH4H2PO4(NH4)2H2P2O7+CO2+2NH3.
This reaction will cause the mixture to bubble and the viscosity to rise sharply. Therefore, the mixing time should be as long as possible. Short, on the premise of ensuring uniform mixing, it should generally be less than 4 minutes and no more than 8 minutes at most.
How to select the right type of spray granulator machine nozzle?
Granulating nozzles generally include rotating differential nozzles, fixed nozzles and vibrating nozzles. Compound fertilizer tower granulation should use rotating differential nozzles. The nozzle is driven by the inner and outer shafts, the inner shaft drives the scraper, and the outer shaft drives the spray basket, and rotates in the same direction or in the opposite direction at a certain speed difference.

What are the design consideration of wet high tower granulation spray nozzle?
The speed of the granulating nozzle should be determined based on the design output and the size of the nozzle hole. It is also an important indicator for selecting the tower diameter. The maximum linear speed of the spray basket should be 3 to 6 m/s. The nozzle holes are arranged in a spiral shape on the spray basket. The nozzle holes gradually increase from bottom to top. The diameter of the nozzle holes is generally 2.2 to 4.5 mm, and the hole spacing is 3 to 3 mm. 9mm. During processing and production, the nozzle holes must be kept round and free of burrs, otherwise it will easily increase grain breakage.