Rotary Cooler Frequently Asked Questions (FAQs)
Rotary Drum Cooler is an efficient industrial cooling equipment, which rapidly reduces the temperature of the material through the heat exchange between the rotating drum and the cold medium, creating ideal conditions for the subsequent processing, storage and packaging. It is widely used in chemical, food, building materials and other industries.
This article introduces “Frequently Asked Questions (FAQs) about Rotary Coolers”, which provides a comprehensive overview of rotary coolers, detailing their function, commonly handled materials and essential maintenance tips. By answering frequently asked questions, it helps investors understand how rotary coolers work, their benefits, and key aspects of their operation. Valuable to those seeking to optimize the performance and extend the life of their rotary coolers, this guide offers practical advice on everything from energy efficiency to troubleshooting.
Reading this text will help individuals and businesses involved in industrial cooling processes. It provides actionable insights on selecting the right rotary cooler, maintaining it effectively, and implementing energy-saving practices. Whether you are a new user or looking to improve your current system, this FAQ guide will provide you with the knowledge you need to increase efficiency, reduce costs and ensure smooth operation.
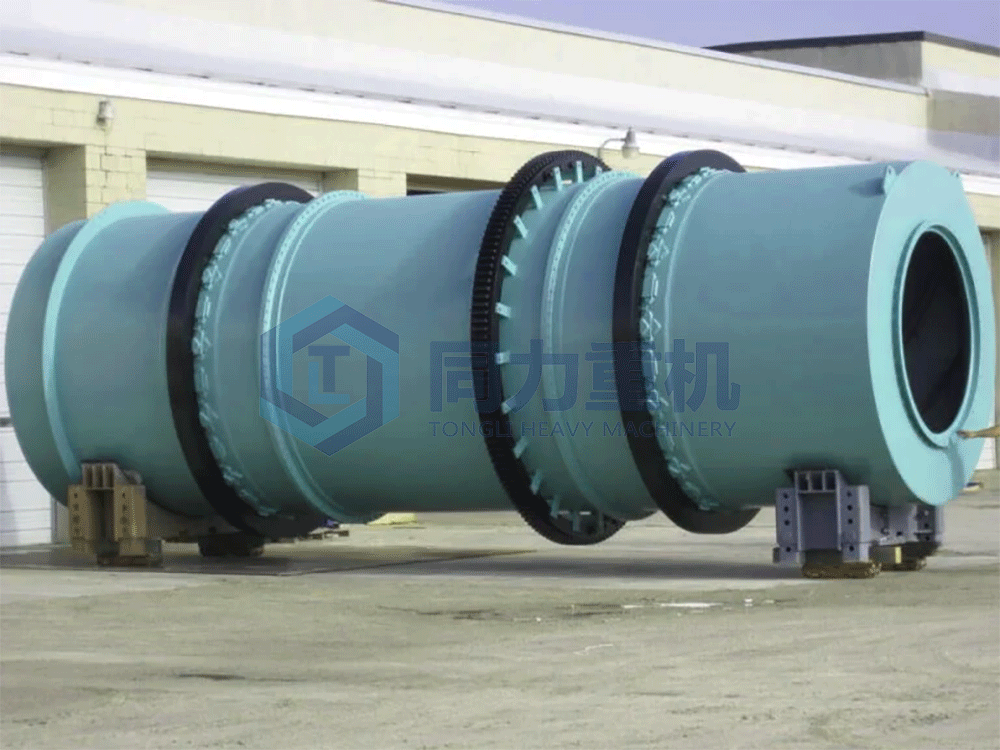
How do rotary coolers work?
A rotary cooler is a highly efficient cooling device used to rapidly cool down materials. Its working principle can be simply summarized as follows: rapid cooling of the material is achieved by friction and heat exchange between the material and the cooling medium.
Specific work process is as follows:
- Material feeding: the material to be cooled through the feed port into the rotating cylinder.
- Rotary motion: rotating cylinder to a certain speed rotation, so that the material in the cylinder roll.
- Cooling medium circulation: cooling medium (usually air or liquid) through the pipe into the rotating cylinder, and the material for full contact.
- Heat exchange: Due to the tilt and rotation of the rotating cylinder, strong friction and turbulence are generated between the material and the cooling medium, which accelerates the heat transfer. The heat in the material is absorbed by the cooling medium, thus realizing the cooling.
- Material discharge: The cooled material is discharged from the discharge port.
What is the difference between direct and indirect coolers?
The main difference between direct and indirect coolers is the contact between the cooling medium and the cooled material.
- Direct cooler: the cooling medium (usually water or air) is directly in contact with the cooled material, and heat exchange is carried out through heat conduction and convection to realize cooling. This way of cooling speed, but the purity of the cooling medium requires high, and easy to produce scaling and other problems.
- Indirect cooler: cooling medium and the cooled material separated by a layer of heat transfer wall, heat exchange through heat conduction. This way of cooling medium purity requirements are lower, but the cooling rate is relatively slow.
Simply put, direct cooling is like putting ice cubes directly into a drink, while indirect cooling involves separating the ice cubes from the drink by a partition through which the heat is allowed to pass.
The choice of cooler depends largely on the nature of the cooling medium, the temperature requirements of the object to be cooled, the requirements for cooling rate and the requirements for system maintenance.
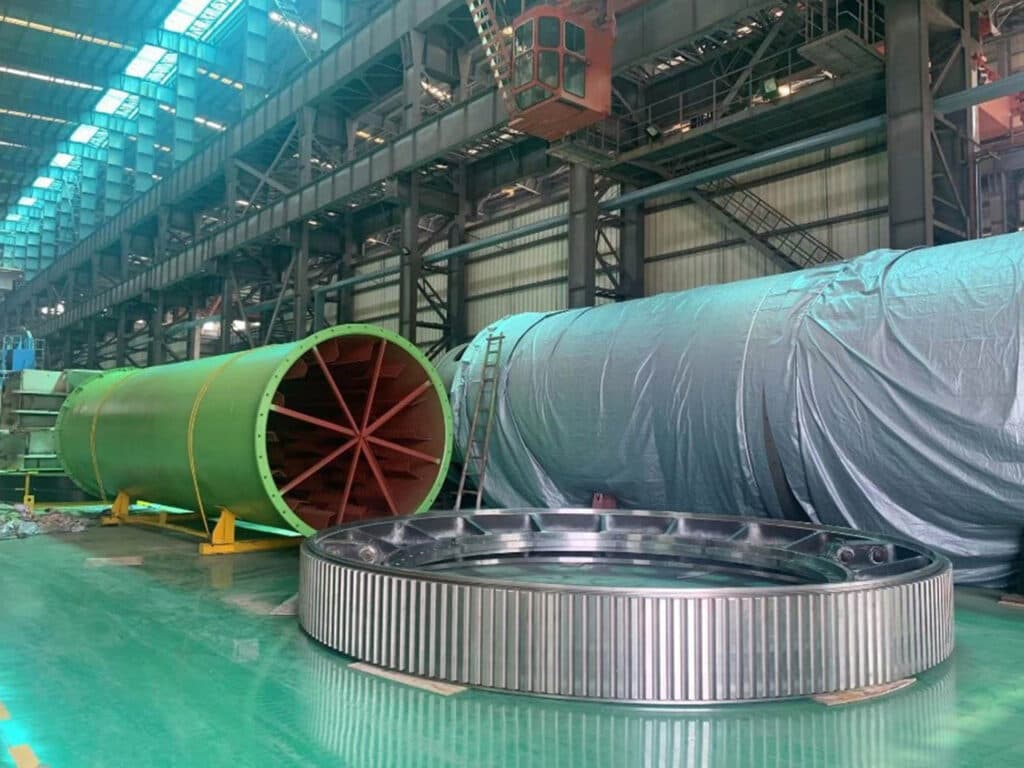
What information is required to design a Drum Cooler?
Multiple data points are required when designing a drum cooler, including the physical and chemical composition of the material, bulk density, inlet and outlet temperatures, moisture content, specific heat, particle size distribution, desired throughput, and the friability of the material or potential for abrasion.
What is the design process of rotary cooler?
The design process of a rotary cooler consists of the following steps: first determine the cooling method, either direct air swept or indirect water cooled; then design the inclined drum structure, including the arrangement of internal lifting scrapers or grills; then design the corresponding cooling system according to the selected cooling method, such as a cold air shower system or water-cooled jacket and nozzle system; design the drive mechanism to ensure the rotation of the drum; design support structures such as concrete columns or steel frames; plan the material conveying system to achieve smooth feeding and discharging; and finally design the temperature monitoring and control system, as well as consider the heat recovery system to improve energy efficiency.
The design of support structures such as concrete columns or steel frames, the planning of the material handling system for smooth feeding and discharging, and finally the design of the temperature monitoring and control system, as well as the consideration of a heat recovery system to improve energy efficiency. The entire design process needs to be optimized according to the specific application, material characteristics and cooling requirements to ensure that the cooling effect is as expected.
What capacity can a Drum Cooler handle?
Drum coolers are high capacity machines capable of handling material throughputs ranging from 1 to 200 tons per hour.
What materials do Drum Coolers consist of?
Depending on the material and process requirements, the Drum Cooler may be constructed from carbon steel, stainless steel, special alloys, explosive composite steel or wear resistant steel.
What additional equipment is required to support the rotary cooler?
In addition to inlet and outlet conveyors, rotary coolers require additional equipment to ensure efficient and environmentally friendly operation. Exhaust and particulate handling systems are essential and typically include a baghouse or scrubber and an induced draft fan (ID). For materials with excessive carryover, a cyclone separator can improve particle capture.
To handle particularly high temperature feeds, it may be necessary to inject water directly into the feed opening and protect the drum shell with a refractory lining. In addition, a waste heat recovery system captures the hot air generated during the cooling process for reuse in the upstream process, thereby reducing fuel and energy consumption.
Which is better for my application, a drum cooler or a fluidized bed cooler?
Both types of industrial coolers offer effective options for reducing the temperature of bulk solids materials. Factors in choosing between the two typically include available space footprint, uniformity of feed, and industry preference. Fluid bed coolers are preferred for applications such as fine chemicals, pharmaceuticals and food, while drum coolers are better suited for industrial applications such as mineral and fertilizer processing.

At what temperatures do Drum Coolers typically operate?
Depending on the temperature of the incoming material and the desired discharge temperature, a drum cooler may operate at any temperature between 150°F and over 1,000°F.
Can a Drum Cooler be automated?
The operation of a Drum Cooler can be made more stable and reliable by equipping it with an automated system. An automated system reduces the risk of human error by minimizing manual intervention, while increasing overall equipment utilization. In addition, by analyzing historical data, process parameters can be optimized to further enhance cooling efficiency.
What sizes of rotary coolers are available?
Drum coolers are available in diameters ranging from 3 feet to 15 feet.
Can roller coolers be customized?
The customized design of drum cooler involves several aspects, including:
- Material selection: According to the corrosive, temperature, abrasive and other characteristics of the material, select the appropriate rotor material and lining material to ensure the durability and safety of the equipment.
- Optimization of internal structure: Improve the heat transfer efficiency and shorten the cooling time by optimizing the design of internal spiral blades, spraying system and other components.
- Selection of drive mode: According to the process requirements and site conditions, select the appropriate drive mode, such as sprocket drive, gear drive, etc., to ensure the smooth and reliable operation of the equipment.
- Control system customization: Provide flexible control system to realize precise control of the cooling process and meet different process requirements.

How to improve the performance of rotary drum cooler?
The performance improvement of rotary drum cooler mainly focuses on several key aspects: firstly, optimizing the heat transfer process, increasing the heat transfer area and improving the distribution of cooling medium; secondly, improving the structure of the rotor, choosing the right material and optimizing the tilt angle of the rotor; and thirdly, upgrading the control system to achieve precise control and real-time monitoring.
What materials can be processed by the drum cooler?
Drum coolers have a wide range of applications and can handle all kinds of bulk solid materials, including fertilizers, feeds, chemicals, ores and so on. Whether it is high temperature material from a dryer or material that has been calcined at high temperatures in a kiln, it can be efficiently cooled by a Drum Cooler.
Below, we will explore some of the common products treated with rotary coolers and their applications.
1. Cement: The use of rotary coolers in the cement industry is very common. After clinker is generated in the kiln, the temperature of the clinker is very high. Rotary coolers are used to reduce the temperature of clinker to a more manageable level, which helps in maintaining product quality and ensures proper handling and storage.
2. Fertilizers: Rotary coolers are used to cool granules or pellets after production when in a fertilizer product line. Rapid and efficient cooling of these materials is essential to maintain their quality and ensure their flowability.
3. Mineral processing: Rotary coolers are used to process minerals such as ores and concentrates. The cooling process helps to maintain the properties of the minerals, which is essential for subsequent processing stages, and prevents agglomeration during processing.
4. Food processing: In the food industry, rotary coolers can be used to cool granular or pelletized food products. This cooling step is necessary to maintain product freshness and extend shelf life.
5. Chemical products: Various chemical products including powders and granules can be cooled by rotary coolers. Proper cooling ensures that these products meet quality standards and remain stable during storage and transportation.
6. Slag: In the metallurgical industry, rotary coolers are used to cool slag, a by-product of metal smelting. Effective cooling helps in the treatment and disposal of slag and ensures that it is properly solidified for subsequent use or recycling.
Why are all Drum Coolers in a counter current air flow configuration?
Counter current air flow configuration is commonly used in drum coolers as opposed to downflow configuration. This is because the counter current configuration makes full use of the thermodynamic principle, so that the high temperature material and the relatively cooler air flow in the opposite direction, thus realizing an efficient heat exchange. This configuration minimizes the outlet material temperature and increases cooling efficiency.
What are the different ways to cool the air used in a Drum Cooler?
There are a number of ways to cool the air used for drum coolers, including ammonia chillers, refrigeration and swamp coolers.
When selecting a rotary cooler, the following key factors need to be considered to ensure that the equipment meets your specific needs and achieves optimum performance:
- Material characteristics: Consider the type, particle size and temperature of the material to be cooled. Different materials may require specific cooling methods or equipment designs.
- Capacity: Evaluate the required cooling capacity, including material volume and cooling rate, to ensure that the equipment meets your production needs.
- Cooling efficiency: Compare the cooling efficiencies of different models to find a balance between performance and energy consumption.
- Energy consumption: Review the energy consumption of the equipment. Efficient designs may cost more initially, but can lead to long-term savings.
- Size and space requirements: Ensure that the equipment is sized for your site and is easy to integrate with existing systems.
- Maintenance requirements: Reduce downtime and maintenance costs by selecting a model that can be easily inspected and serviced on a regular basis.
- Environmental conditions: Consider factors such as temperature and humidity of the operating environment, which can affect equipment performance and life.
- Cost-effectiveness: Compare the initial and long-term operating costs of different models to assess overall economics.
- Vendor support: Evaluate the availability of installation support, technical service and spare parts from your vendor.
By considering these factors thoroughly, you can select the rotary cooler that best suits your operational needs, increasing productivity and bringing long-term benefits to your industrial processes.

Maintenance requirements for rotary coolers
Proper maintenance of rotary coolers is critical to their efficient operation and long life. The following are some of the major maintenance requirements:
1. Periodic Inspection
Regularly inspect drums, bearings, seals and drive mechanism for damage, abnormal vibration or noise.
2. Lubrication
Regularly lubricate moving parts (such as bearings and gears) according to the manufacturer’s recommendations to avoid excessive or inadequate lubrication.
3. Alignment and Balancing
Ensure parts are properly aligned and balanced to prevent uneven wear and mechanical stress. Check and adjust regularly.
4. Cleaning
Periodically clean the inner and outer surfaces of the cooler to remove material buildup to maintain cooling efficiency.
5. Inspection of seals
Regularly inspect seals and gaskets to ensure there is no wear or cracks and replace damaged parts promptly.
6. Monitor consumable parts
Regularly inspect consumable parts such as lifting devices, nozzles and refractory linings and replace them as needed.
7. Calibrate control systems
Calibrate temperature sensors and manometers regularly to ensure accurate readings and efficient operation.
8. Record maintenance
Keep detailed records of all maintenance activities, including inspections, repairs, and replacements to track performance and plan for future maintenance.
By following these maintenance requirements, you can improve the performance and longevity of your rotary cooler and ensure smooth industrial production.
How to troubleshoot common rotary cooler problems?
It’s not uncommon to encounter problems when using rotary coolers, but quickly identifying and resolving them can prevent costly downtime and ensure optimal performance. Here are some common problems and their solutions:
1. Inadequate cooling performance
If a rotary cooler is not cooling as well as expected, several factors may be at play. First, check airflow and material feed. Inadequate airflow or material feed obstructions may seriously affect cooling performance. Make sure fans and ducts are free of obstructions and operating properly. Also, check the cooling drum for buildup or damage, which can affect heat transfer.
2. Excessive wear
Wear can take different forms, including increased vibration, noise or physical damage to rotary cooler components. Regularly inspect the drum liners, drive system and support rollers for signs of wear. Replace any damaged parts and make sure all parts are in good alignment and lubricated. 3.
3. Abnormal Noise or Vibration
Abnormal noise or vibration can indicate multiple problems such as imbalance or misalignment. Check the rotary cooler drums for signs of imbalance and verify that all bearings and rollers are functioning properly. Tighten any loose bolts and make sure the foundation is secure to minimize vibration.
4. System Leaks
Leaks in the rotary cooler can cause efficiency problems and potential damage. Check all seals and gaskets for signs of leakage, and inspect the cooling chamber for cracks or damage. Repair or replace any damaged seals, and address any structural damage quickly.
5. Inefficient heat transfer
Inefficient heat transfer can be caused by a number of factors, including material deposits on the cooling drum or inadequate airflow. Clean the rollers and their associated parts to remove any residue that may impede heat transfer. Ensure that the airflow system is properly tuned to promote effective cooling.
6. Module overheating
If components are overheating, it may be due to inadequate cooling or overloading of the rotary cooler. Check that the cooling system is operating properly and verify that the cooler is not exceeding its capacity. Reduce material feed or adjust cooling settings as needed to control temperature.

Conclusion
Drum coolers provide an effective method of cooling almost all types of bulk solids, from ores to chemicals. To ensure an efficient and reliable solution, it is advisable to work with an expert.
TONGLI has been the world’s leading manufacturer of rotary coolers since 1958. With advanced technology and innovative designs, TONGLI’s rotary coolers are known for their superior quality and reliable performance. We provide customized rotary cooler solutions according to the specific needs of our customers and offer a full range of after-sales services. If you would like to know more about our rotary coolers, please feel free to contact us!