A Look at Indirect Coolers
Indirect rotary cooler is a special type of industrial cooler, specially used to solve the cooling problems of bulk solid materials. Compared with direct rotary cooler, indirect rotary cooler has the advantages of good cooling effect, strong applicability, stable operation, simple structure, convenient maintenance, environmental protection and energy saving, so it is widely used in chemical industry, building materials, metallurgy, food, environmental protection and other fields.

The working principle of indirect cooler
The indirect rotary cooler cools the material through the contact between the material and the drum shell, instead of using cold air flow. This way can effectively avoid the direct contact between the material and the cold air, preventing the material from oxidation, deterioration and other problems. In addition, the indirect rotary cooler can also control the cooling effect by adjusting the rotational speed of the drum shell and the temperature of the cooling water, thus providing a more controllable processing environment for the materials.
Working Process:
- The fixed shell surrounds the rotating drum to ensure that the material does not come into direct contact with the cooling water.
- As the material moves within the rotating drum, water is continuously showered on the drum shell, hence the name “indirect water spray cooler”.
- The cooling water indirectly cools the material inside through contact with the drum shell.
Water circulation system:
- A continuous or recirculating supply of water is required to cool the outer surface of the rotating drum.
- If a recirculation system is used, the used water needs to be cooled by a heat exchanger.
- The cooled water is circulated back to the tank to restart the process of showering and cooling the rotating drum.
This design not only cools the material efficiently, but also maintains a controlled processing environment and is particularly suitable for scenarios where direct contact of the material with the cooling medium needs to be avoided.
Main components of the indirect cooler
The Indirect Cooler consists of the following main components:
- Rotating drum: used to hold and transport the material to be cooled.
- Fixed housing: wraps around the rotating drum to ensure that the material does not come into direct contact with the cooling water.
- Water Tank: Used to store and supply cooling water.
- Water collection system: collects the used cooling water for recycling or discharge.
- Heat exchanger core: is the core component of the indirect cooler and can be of plate-fin, tube or plate-tube construction. It contains two unconnected air flow paths, which achieve heat exchange through the intervening walls.
- Water spray system: Used to continuously flush cooling water over the outer surface of the rotating drum.
- Heat exchanger: If a recirculating water system is used, a heat exchanger is required to cool the recovered water so that it can be reused.
These components work together to achieve cooling of the material by means of indirect contact, whilst maintaining separation of the material from the cooling medium. This design is particularly suited to application scenarios where controlled environments or the handling of lightweight materials are required.

Advantages of Indirect Rotary Coolers
Indirect Rotary Coolers provide a safe and controlled cooling method for specialised materials by achieving cooling through indirect contact between the material and the cooling drum shell.
The main applications and advantages of indirect rotary coolers include.
- Ideal for cooling lightweight materials to avoid loss of material being carried away by the cooling airflow.
- Suitable for applications where a controlled environment is required to prevent oxidisation or combustion of materials in direct contact with air.
- Commonly used for cooling special materials such as pigments and powders.
- Provides a controlled cooling environment and reduces product loss, suitable for industries requiring precise temperature control.
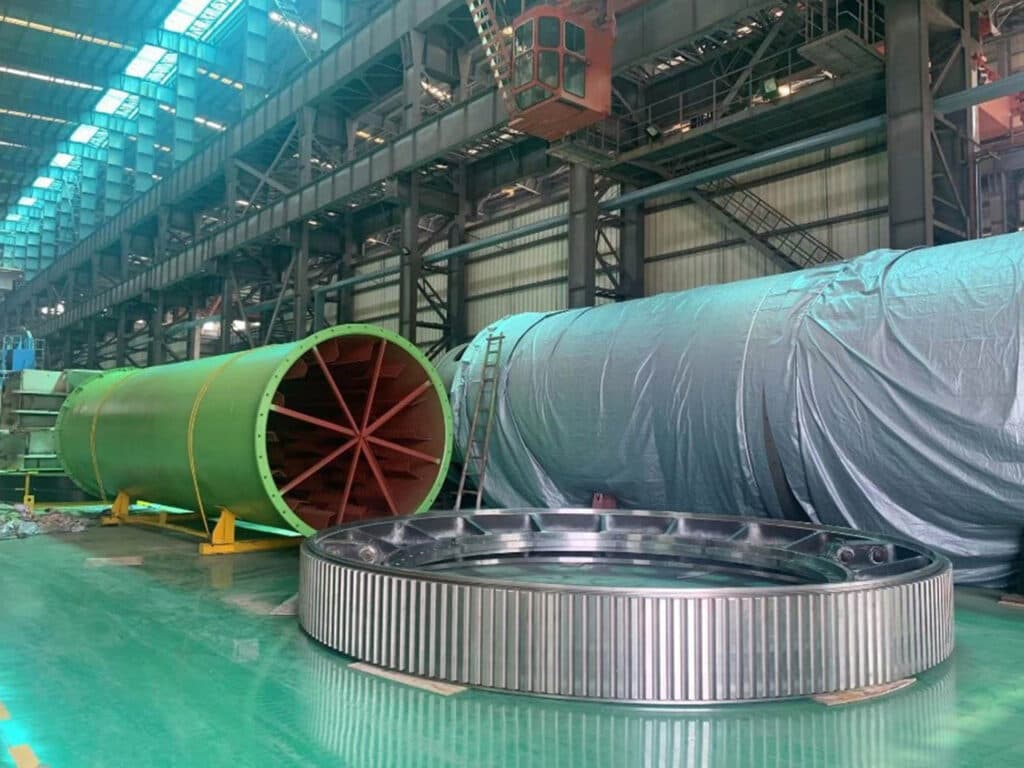
Indirect Rotary Cooler Application Areas
Indirect rotary cooler is widely used in chemical industry, building materials, metallurgy, food, environmental protection and other fields, mainly used to cool the following materials:
- Chemical industry: cooling fertiliser, pesticide, pigment, dye, etc.
- Building materials industry: cooling cement, lime, gypsum, etc.
- Metallurgical industry: cooling ores, concentrates, alumina, etc.
- Food industry: cooling grain, oilseeds, soybean meal, etc.
- Environmental protection industry: cooling flue gas desulphurisation lime, sewage sludge, etc.
Indirect coolers play a key role in fertiliser production. Usually, fertiliser production lines are equipped with indirect coolers to effectively cool the freshly produced high temperature fertiliser granules, preventing them from melting or clumping, and thus maintaining the shape and quality of the fertiliser granules.
Indirect coolers have the advantage of providing a controlled cooling environment for specialised materials, reducing product loss and avoiding the adverse reactions that can occur when certain materials come into contact with air. Indirect coolers are an important process equipment option for industries that require precise temperature control and prevention of material contamination.

TONGLI specialises in rugged, high quality indirect rotary coolers that meet the challenges of specific applications. We can custom design rotary coolers to meet the characteristics of each unique material. In addition to special structural designs, our indirect rotary cooler drums are made of stainless steel for effective protection against water corrosion. For particularly hot materials, special alloys can be used at the inlet to avoid damage to the stainless steel drum.
TONGLI Indirect Rotary Coolers are popular with our customers for their environmentally friendly and energy efficient operation and customisability. For more information about customised coolers to meet your individual processing needs, please feel free to contact us!